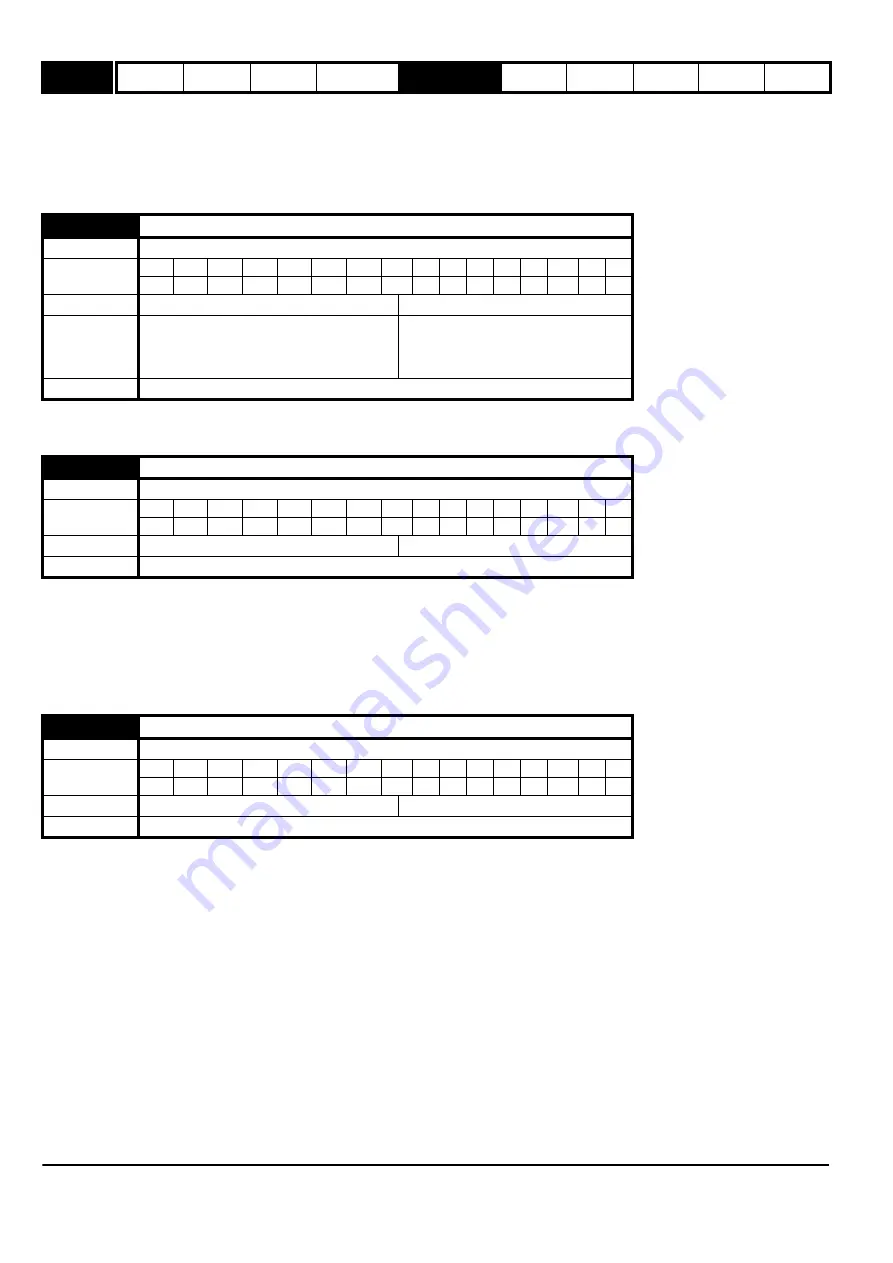
Menu 6
Parameter
structure
Keypad and
display
Parameter
x.00
Parameter
description format
Advanced parameter
descriptions
Macros
Serial comms
protocol
Electronic
nameplate
Performance RFC mode
148
Unidrive SP Advanced User Guide
www.controltechniques.com Issue Number: 10
The active rectifier status signals are monitored in one of the following ways:
1. When SPMAxxx drives are connected in parallel the status of the individual rectifiers is monitored through the parallel module control interface
system.
2. When SPMDxxx drives are connected in parallel the status of the individual rectifiers is combined and is monitored when the combined status
signals are connected to power module one.
3. When an external rectifier is used, these monitoring features are provided via digital I/O terminals using the rectifier monitoring feature of the
variable selector blocks (see menu 12).
The mains loss detection level can be adjusted using this parameter. If the value is reduced below the default value the default value is used by the
drive. If the level is set too high so that mains loss detection becomes active under normal operating conditions the motor will coast to a stop.
When power modules are connected in parallel various trips can be initiated from the power modules themselves. To aid identification of the source of
the trip the module number of the source can be stored in the module number and trip time log (Pr
10.41
to Pr
10.51
). If the drive is a single module
drive (Sp1xxx to SP6xxx) the module number that is stored is normally zero.
However, a SPMAxxxx or SPMDxxxx drive is installed with the interface circuits normally intended for parallel operation, so if a SPMAxxxx or
SPMDxxxx drive is used as a single module then a module number of 1 is stored. If Pr
6.49
is zero the module number is stored in the module
number and trip time log. If this parameter is one, either the powered-up clock or run time clock is stored in the module number and trip time log as
defined by Pr
6.28
. It should be noted that changing this parameter clears the trip, and module number and trip time logs.
The drive comms system 128 bytes buffer used with ANSI or Modbus rtu protocols via the 485 connector can be controlled by a Solutions Module
under certain circumstances. This parameter shows which node has control of the buffer (0 (drv) = drive, 1 (Slot1) = Solutions Module in slot 1, etc. If
a Solutions Module has control of the buffer the drive will use an alternative buffer for 485 comms and the following restrictions will apply:
1. Comms messages via the 485 port are limited to a maximum of 32 bytes
2. The 6 pin keypad port will operate correctly with an LED keypad, but it will no longer operate with an LCD keypad
3. Modbus messages using the CMP protocol can only route messages to nodes within the drive. It will not be possible for these to be routed further,
i.e. via CT Net on an SM Applications module.
6.48
Mains loss ride through detection level
Drive modes
Open-loop, Closed-loop vector, Servo, Regen
Coding
Bit
SP
FI
DE
TE
VM
DP
ND RA NC NV PT US RW BU PS
1
1
1
1
1
Range
Open-loop,Closed-loop vector, Servo
0 to DC_VOLTAGE_SET_MAX V
Default
Open-loop,Closed-loop vector, Servo
200V rated drive 205
400V rated drive 410
575V rated drive 540
690V rated drive 540
Update rate
Background read
6.49
Disable multi-module drive module number storing on trip
Drive modes
Open-loop, Closed-loop vector, Servo, Regen
Coding
Bit
SP
FI
DE
TE
VM
DP
ND RA NC NV PT US RW BU PS
1
1
1
Default
Open-loop, Closed-loop vector, Servo, Regen
0
Update rate
Background read
6.50
Drive comms state
Drive modes
Open-loop, Closed-loop vector, Servo, Regen
Coding
Bit
SP
FI
DE
TE
VM
DP
ND RA NC NV PT US RW BU PS
1
1
1
1
1
Default
Open-loop,Closed-loop vector, Servo, Regen
0 to 3
Update rate
Background write
Summary of Contents for unidrive sp
Page 419: ......
Page 420: ...0471 0002 10 ...