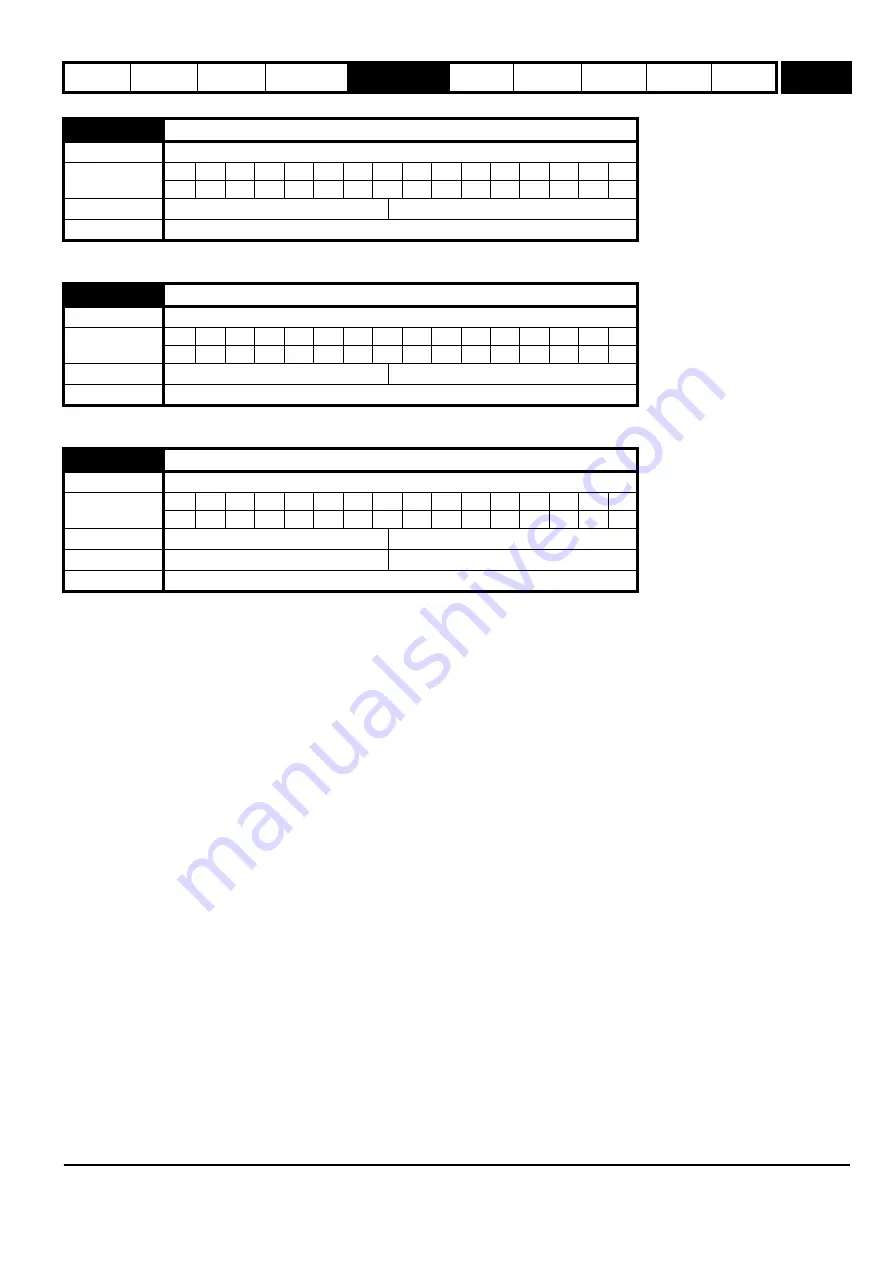
Parameter
structure
Keypad and
display
Parameter
x.00
Parameter
description format
Advanced parameter
descriptions
Macros
Serial comms
protocol
Electronic
nameplate
Performance RFC mode
Menu 1
Unidrive SP Advanced User Guide
41
Issue Number: 10 www.controltechniques.com
Indicates the reference currently selected
Indicates the preset reference currently being selected
Selects the value of the keypad control mode (Pr
1.17
) at power-up as follows:
0
rESEt zero
1
LASt
last value used before power-down
2
PrS1
Preset 1, Pr
1.21
, before power-down
1.49
Reference selected indicator
Drive modes
Open-loop, Closed-loop vector, Servo
Coding
Bit
SP
FI
DE Txt VM DP ND RA NC NV
PT
US RW BU PS
1
1
1
1
Range
Open-loop, Closed-loop vector, Servo
1 to 5
Update rate
4ms write
1.50
Preset reference selected indicator
Drive modes
Open-loop, Closed-loop vector, Servo
Coding
Bit
SP
FI
DE Txt VM DP ND RA NC NV
PT
US RW BU PS
1
1
1
1
Range
Open-loop, Closed-loop vector, Servo
1 to 8
Update rate
4ms write
1.51
Power-up keypad control mode reference
Drive modes
Open-loop, Closed-loop vector, Servo
Coding
Bit
SP
FI
DE Txt VM DP ND RA NC NV
PT
US RW BU PS
1
1
1
1
Range
Open-loop, Closed-loop vector, Servo
0 to 2
Default
Open-loop, Closed-loop vector, Servo
0
Update rate
N/A
Summary of Contents for unidrive sp
Page 419: ......
Page 420: ...0471 0002 10 ...