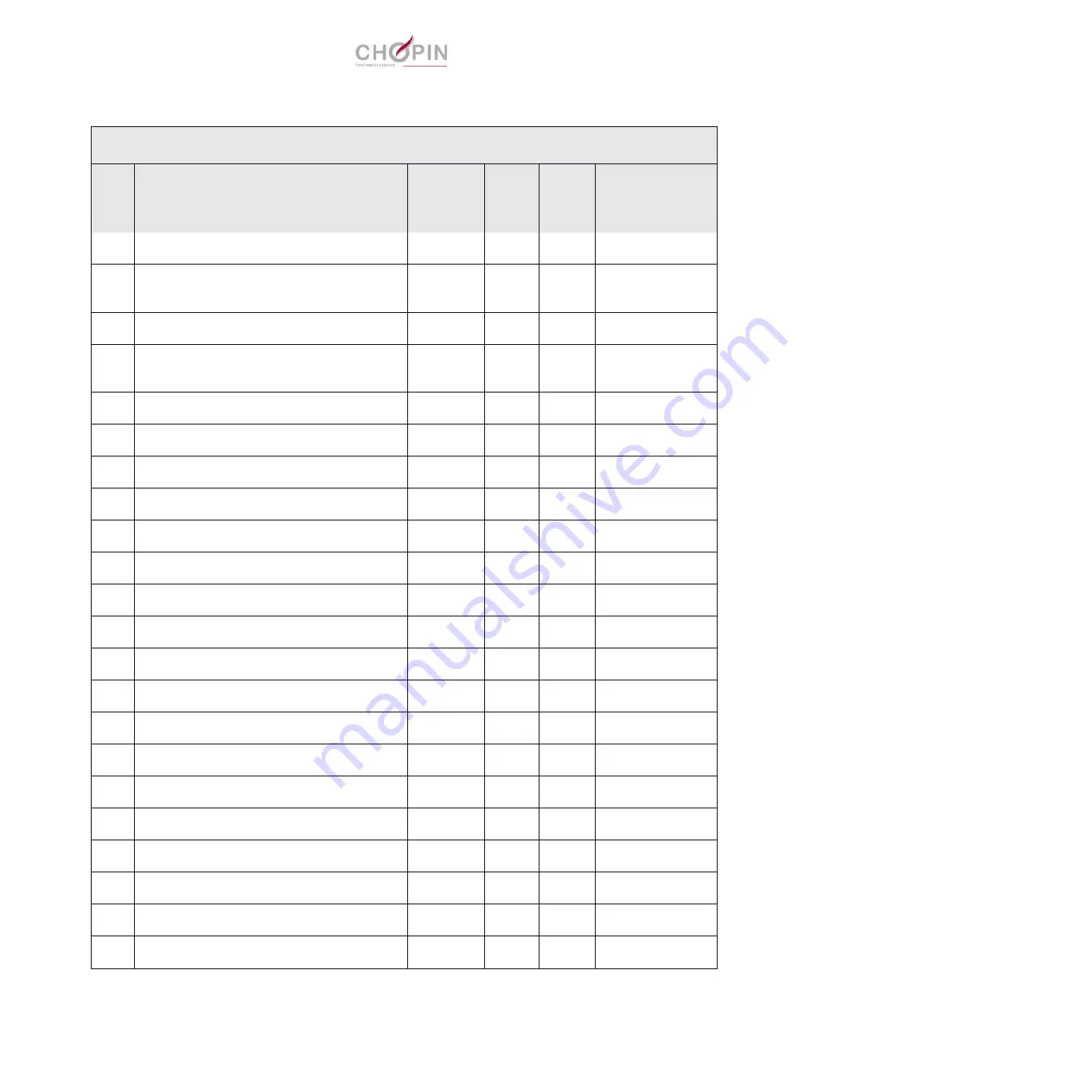
Chapter 4 Spare parts
135
Maintenance manual
MM-MIXO-EN Ind. 0
04/2012
Mixolab
Mixolab - Compressor and CPU support
item
Description
CHOPIN
Part no.
Qty
Min.
qty p.
order
Note
1
INDUCTOR - WIRED, 1.2A ARMATURE
MIX 12
1
2
SCREW - HSHC M5X12, STAINLESS
STEEL
2
3
WASHER - RLC 5MM DIA
2
4
SOLENOID VALVE - WIRED,
COMPRESSOR
MIX 183
1
5
WASHER - RLC 4X10MM DIA
2
6
SCREW - HSHC 3X6I
7
COMPRESSOR - MEMBRANE
MIX 6
1
8
SUPPLY BOARD
SEN 150
1
9
SCREW - HSHC M3X6, STAINLESS STEEL
4
10
SUPPLY BOARD - 24 V
CB 159
1
11
CPU BOARD - MIXOLAB
SEN 162
1
12
SCREW - HSHC M3X6, STAINLESS STEEL
4
13
WASHER - RLC 5MM DIA
2
Summary of Contents for Mixolab
Page 2: ......
Page 4: ......
Page 6: ...Mixolab 6 Maintenance manual MM MIXO EN Ind 0 04 2012...
Page 8: ...8 Maintenance manual MM MIXO EN Ind 0 04 2012 Mixolab...
Page 15: ...15 Maintenance manual MM MIXO EN Ind 0 04 2012 Mixolab Chapter 2 TROUBLESHOOTING...
Page 16: ...16 Maintenance manual MM MIXO EN Ind 0 04 2012 Mixolab...
Page 31: ...31 Maintenance manual MM MIXO EN Ind 0 04 2012 Mixolab Chapter 3 REPAIR...
Page 32: ...32 Maintenance manual MM MIXO EN Ind 0 04 2012 Mixolab...
Page 38: ...38 Chapter 3 Repair Maintenance manual MM MIXO EN Ind 0 04 2012 Mixolab...
Page 122: ...122 Chapter 3 Repair Maintenance manual MM MIXO EN Ind 0 04 2012 Mixolab...
Page 123: ...123 Maintenance manual MM MIXO EN Ind 0 04 2012 Mixolab Chapter 4 SPARE PARTS...
Page 124: ...124 Maintenance manual MM MIXO EN Ind 0 04 2012 Mixolab...
Page 126: ...126 Chapter 4 Spare parts Maintenance manual MM MIXO EN Ind 0 04 2012 Mixolab...
Page 144: ...144 Chapter 4 Spare parts Maintenance manual MM MIXO EN Ind 0 04 2012 Mixolab...