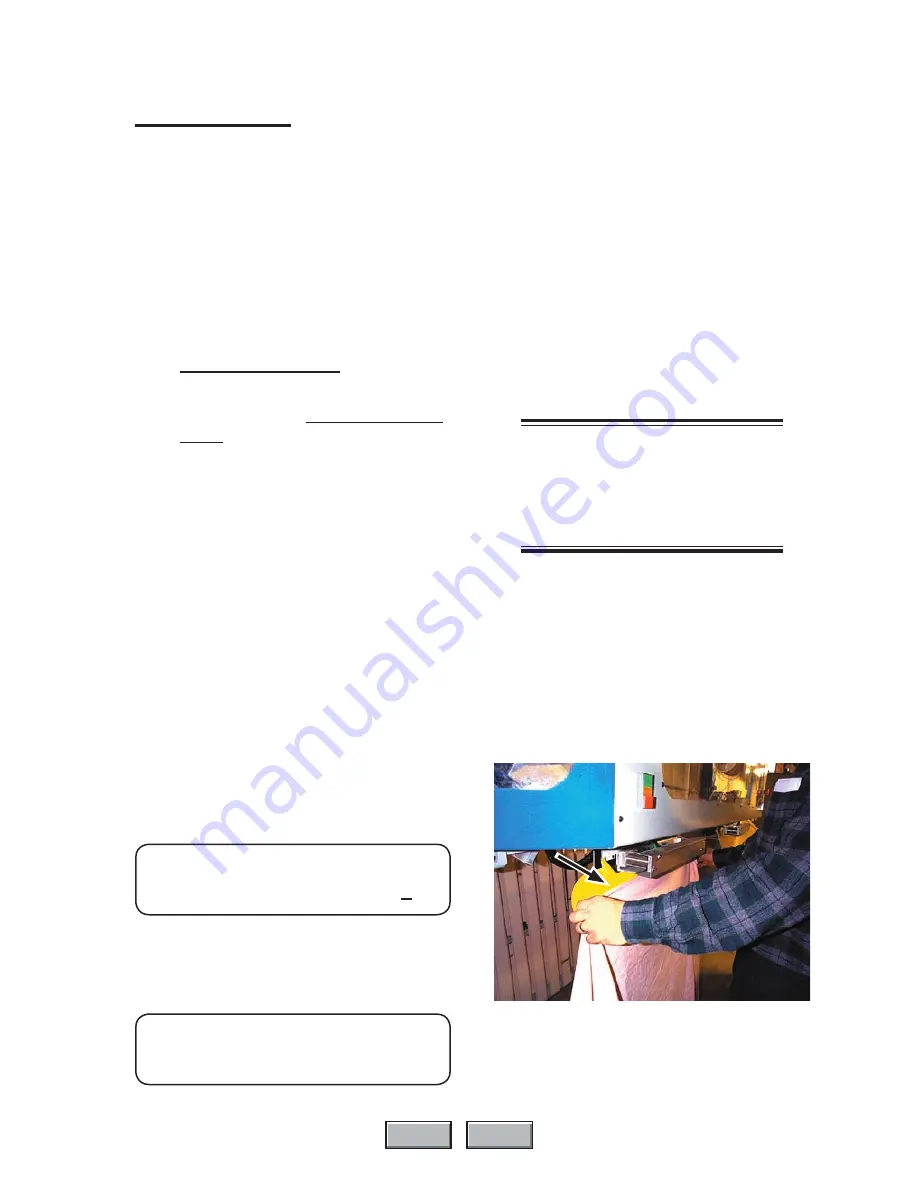
King Edge Vac
Operating Guidelines
3-9
Flatwork Handling
The way that operators use the feeder is very
important. They can increase productivity, extend
the life of the unit, and most importantly, promote
safety.
Safety
Always follow the site standards to
avoid repetitive motion injury.
If an item jams, do not reach inside the
unit while the power is on. Refer to
Handling a Jam Safely
.
If an item falls, leave it until the end of
the batch. Refer to
Handling Misfeeds
Safely
.
Program Selection
Pressing a STATION key will select a preset
program by number and item type. The presets
are for KING Sheet’s, COTTON and 75/25, and
QUEEN Sheet’s, COTTON and 75/25.
Pressing a STATION key until the light goes
off leaves the feeder running in stand-by mode.
Set Pacing (Option)
If the unit is equipped with the optional pacing
lights, follow theses steps to set the unit to signal
whether the pace is being met on a hourly basis.
On the CHI Panel, press and hold the AD-
JUST button; then, press the ENTER but-
ton. Release both buttons. The SELECT
ADJUSTMENT menu displays:
SELECT ADJUSTMENT
INL TRN SPR FEED IRN CHI
The flashing cursor is under CHI.
Press the ENTER button. The Program
Adjustments (CHI) menu displays:
FAST=10” LSP290 TORQ.08S
AIR.16S GAP-07” PACE=420
•
•
•
1.
2.
Press the CURSOR button until it is under
the pace setting.
Press the + or - key as appropriate to set
the desired hourly standard. The range is
from 240 to 660 pieces per hour, in 20
piece increments.
When the correct value is displayed, press
ENTER.
The SELECT ADJUSTMENT menus
displays. Press ENTER again to return to
normal operation.
Feeding Sheets (large pieces)
NOTE:
The unit is designed to
process large pieces of flatwork
ranging in size from 48” (1220
mm) to 120” (3050 mm). It is NOT
designed to feed folded flatwork.
Remove a sheet from the laundry basket.
Place the approximate center of the long
edge of the sheet up along the yellow
station table guide between the carriage
clamps (Figure 3-9).
3.
4.
5.
6.
1.
2.
Figure 3-9: Place the approximate center of the
long edge of the sheet up along the
yellow guide into the feed conveyor
clamps.
TOC
INDEX
Summary of Contents for King Edge VAc
Page 12: ......
Page 40: ......
Page 54: ......
Page 78: ......
Page 250: ...3038 015e King Edge VAC PL 32 This page intentionally left blank TOC INDEX PL TOC...
Page 262: ...SC 2 460V Motor Circuit SC TOC TOC INDEX...
Page 264: ...SC 4 208 230V Motor Circuit SC TOC TOC INDEX...
Page 266: ...SC 6 Control Power Communications SC TOC TOC INDEX...
Page 268: ...SC 8 Controller Inputs SC TOC TOC INDEX...
Page 270: ...SC 10 Control Outputs SC TOC TOC INDEX...
Page 273: ...King Edge Vac 3210 437b SC 13 This page intentionally left blank SC TOC TOC INDEX...
Page 274: ...SC 14 Prefeeder Control Circuit SC TOC TOC INDEX...
Page 276: ...3210 437b King Edge Vac SC 16 This page intentionally left blank SC TOC TOC INDEX...
Page 277: ...SC 17 24 VAC Control Circuit SC TOC TOC INDEX...
Page 278: ...SC 18 Interlock Circuit system E stop SC TOC TOC INDEX...
Page 279: ...SC 19 Pneumatic Diagram SC TOC TOC INDEX...
Page 280: ...SC 20 Prefeeder Electrical Panel SC TOC TOC INDEX...
Page 282: ...SC 22 Disconnect Panel SC TOC TOC INDEX...
Page 284: ...SC 24 Main Eletrical Panel SC TOC TOC INDEX...
Page 285: ......
Page 286: ......
Page 287: ......
Page 288: ......
Page 290: ......
Page 292: ......
Page 302: ......