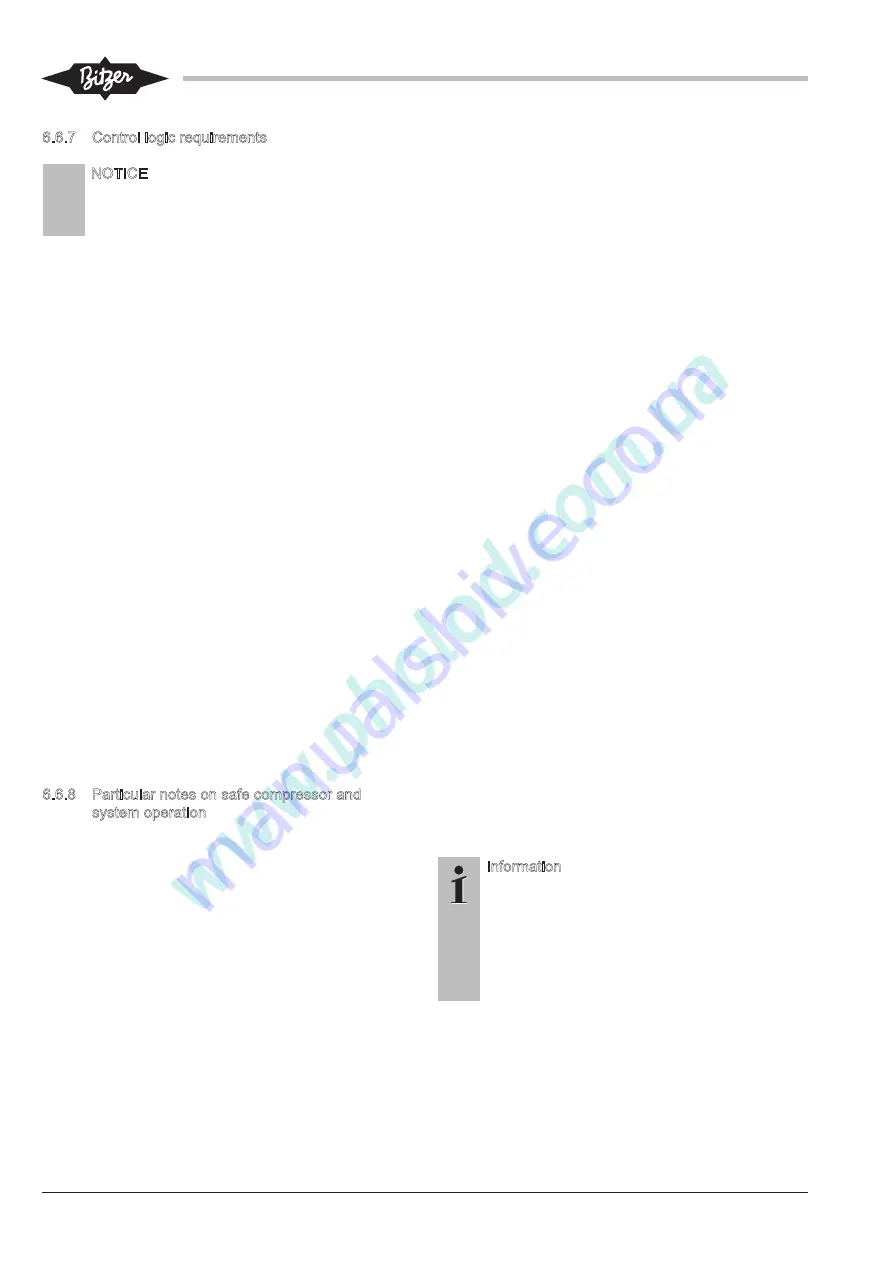
SB-170-9 RUS
30
SB-170-9
90
5.1 Raccordements réseau
Lors du dimensionnement des contacteurs du moteur,
des conduites d'amenée et des fusibles :
• Prendre en considération le courant de service maxi-
mal ou la puissance absorbée maximale du moteur.
• Choisir des contacteurs de la catégorie d'utilisation
AC3.
• Régler le relais thermique sur le courant de service
maximal du compresseur.
5.2 Versions moteur
!
!
AVIS
Risque de défaillance de compresseur !
N'utiliser le compresseur que dans le sens de
rotation prescrit !
Les séries de compresseurs CS.65, CS.75, CS.85,
CSH76 et CSH86 sont équipées de série de moteurs à
bobinage partiel (Part Winding, « PW ») avec
connexion Δ/ΔΔ. En option, elles peuvent également
être équipées de moteurs à étoile/triangle (Y/Δ). Pour
des informations détaillées, se reporter au manuel
SH-170.
Les modèles CS.95, CSH96 et CSW105 sont générale-
ment équipés de moteurs à étoile/triangle (Y/Δ).
Moteurs à bobinage partiel (PW)
Méthodes de démarrage :
• Démarrage à bobinage partiel pour réduire le cou-
rant de démarrage.
• Démarrage direct.
Retard de temps avant l’allumage du 2ème bobinage
partiel : 0,5 s max. !
Effectuer correctement les raccordements ! Une erreur
d’arrangement des raccords électriques aboutit à des
champs tournants contraires ou à l’angle de phase dé-
calé, et donc à un blocage du moteur !
Raccorder les bornes du moteur au couvercle de la
boîte de raccordement conformément aux instructions.
Tenir compte absolument de l’ordre des bobinages par-
tiels !
• 1er bobinage partiel (contacteur K1) : Raccords 1 /
2 / 3.
• 2ème bobinage partiel (contacteur K2) : Raccords 7 /
8 / 9.
• Partage de bobinage 50%/50%.
• Répartition des contacteurs moteur :
– 1er contacteur (PW 1) : 60% du courant de ser-
vice max.
– 2ème contacteur (PW 2) : 60% du courant de ser-
vice max.
Moteur à étoile-triangle
Le retard de temps entre la mise en route du compres-
seur d’un côté et, de l’autre, la commutation entre
l’opération en étoile et celle en triangle ne doit pas dé-
passer les 2 s.
Effectuer correctement les raccordements !
Toute erreur d’arrangement des raccords électriques
aboutit à un court-circuit !
Information
Les contacteurs réseau et triangles doivent être
calculés à au moins 60% du courant de service
max., le contacteur étoile à 33%.
5.3 Essai de haute tension (test de résistance
d'isolation)
Les compresseurs ont déjà été soumis avant leur sortie
d’usine à un essai de haute tension conformément à la
norme EN12693 ou conformément aux normes UL984
ou UL60335-2-34 pour la version UL.
!
!
AVIS
Risque d'endommagement de l'isolant et de dé-
faillance du moteur !
Il ne faut surtout pas répéter l'essai de haute
tension de la même manière !
Un nouvel essai de haute tension ne doit être réalisé
qu’à une tension alternative max. de 1000 V CA.
SB-170-9
30
6.6.7 Control logic requirements
!
!
NOTICE
Risk of motor failure!
The specified requirements must be ensured by
the control logic!
• Desirable minimum running time: 5 minutes!
• Switching the compressor off:
When using a star-delta motor, shut it off from the
25%-CR stage!
• Minimum standstill time:
– 5 minutes (CSW105: 10 minutes).
This is the time the control slider needs to reach
the optimal start position.
– 1 minute.
Only if the compressor has been shut off from the
25%-CR stage!
– Also observe minimum standstill times during
maintenance work!
• Maximum cycling rate:
– CS.65 and CS.75: max. 6 starts per hour.
– CS.85, CS.95 and CSW105: max. 4 starts per
hour.
• Switching time of the motor contactors:
– Part winding: 0.5 s.
– Star-delta: 1 to 2 s for CS.65, CS.75 and CS.85.
– Star-delta: 1.5 to 2 s for CS.95 and CSW105.
6.6.8 Particular notes on safe compressor and
system operation
Analysis show that compressor failures are most often
due to an inadmissible operating mode. This applies
especially to damage resulting from lack of lubrication:
• Function of the expansion valve – observe the manu-
facturer's notes!
– Position the temperature sensor correctly at the
suction gas line and fasten it.
– When using a liquid suction line heat exchanger:
Position the sensor as usual after the evaporator
and not after the heat exchanger.
– Ensure sufficiently high suction gas superheat,
while also taking into account the minimum dis-
charge gas temperatures.
– Stable operating mode under all operating and
load conditions (also part-load, summer/winter op-
eration).
– Solid liquid at the expansion valve inlet, during
ECO operation already before entering the liquid
subcooler.
• Avoid refrigerant migration from the high-pressure
side to the low-pressure side or into the compressor
during long shut-off periods!
– Always maintain oil heater operation when the
system is at standstill. This is valid for all applica-
tions.
When installing the system in zones where the
temperatures are low, it may be necessary to in-
sulate the oil separator. At compressor start, the
oil temperature, that is measured under the oil
sight glass, should be 15 .. 20 K above the ambi-
ent temperature.
– Automatic sequence change for systems with sev-
eral refrigerating circuits (approximately every 2
hours).
– Mount an additional check valve in the discharge
gas line if no temperature and pressure compens-
ation is reached even after long standstill times.
– If needed, mount a time and pressure-dependant
controlled pump down system or liquid separators
on the suction side – particularly for high refriger-
ant charges and/or when the evaporator may be-
come hotter than the suction gas line or the com-
pressor.
• For further information about pipe layout, see
manual SH-170.
Information
In the case of refrigerants with low isentropic ex-
ponent (e.g. R134a), a heat exchanger between
the suction gas line and the liquid line may have
a positive effect on the system's operating mode
and coefficient of performance.
Arrange the temperature sensor of the expan-
sion valve as described above.