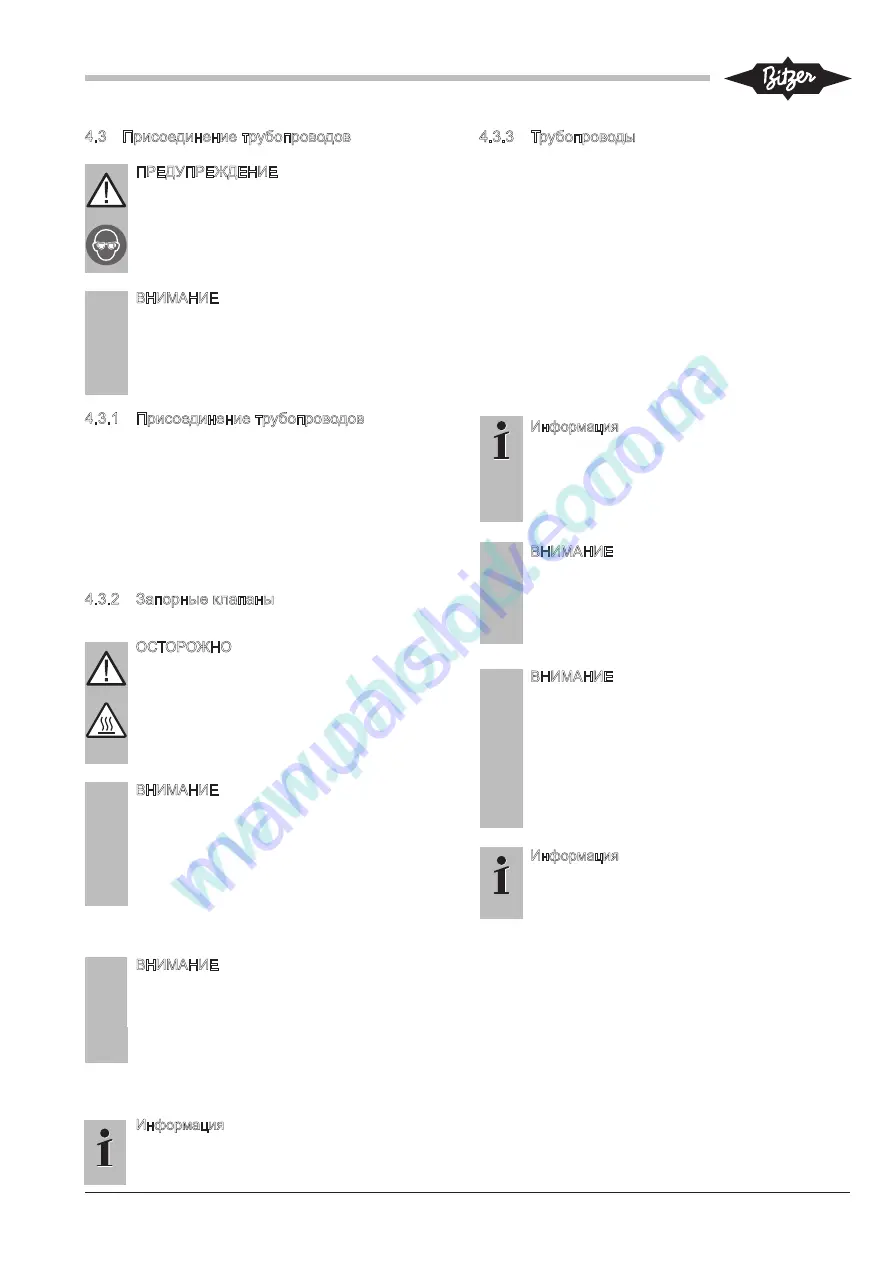
SB-170-9 RUS
77
SB-170-9
25
5.4.2 CM-SW-01
Standard for all CSW105 compressors
The compressor module integrates the entire electronic
periphery of the compressor: It allows monitoring the
essential operating parameters of the compressor: mo-
tor and discharge gas temperature, phase and rotation
direction monitoring, oil supply and application limits
and thus protects the compressor from operation under
critical conditions. For further information, see Tech-
nical Information ST-150.
!
!
NOTICE
The compressor module may be damaged or
fail!
Never apply any voltage to the terminals of CN7
to CN12 – not even for test purposes!
The voltage applied to the terminals of CN13
must not exceed 10 V!
The voltage applied to terminal 3 of CN14 must
not exceed 24 V! Do no apply voltage to the
other terminals!
The following components are completely installed and
wired in the state of delivery:
• Slider position indicator.
• Oil monitoring (OLC-D1).
• Solenoid valves for capacity control and V
i
.
• Discharge gas temperature sensor.
• Low pressure and high pressure transmitter.
Modification to these components or their wiring is not
required and should not be done without consulting
BITZER.
The following components are not installed and wired in
the state of delivery and need to be connected:
• Motor temperature monitoring (PTC sensor in motor
winding).
• Phase monitoring (in case of a phase failure or inad-
missibly high phase asymmetry).
The compressor module internally supplies voltage to
the peripheral devices (solenoid valves, oil monitoring
device and slider position indicator) and to the terminal
strips CN7 to CN12.
Please refer to the Technical Information ST-150 for in-
formation on all connections.
5.4.3 SE-i1
This protection device with extended monitoring func-
tions can be used as an option for all HS.53 .. HS.85
compressors and CSH and CSW compressors.
Monitoring functions:
• Temperature monitoring.
• Monitoring of the PTC control circuit to detect any
short-circuit or line break/sensor failure.
• Rotation direction monitoring.
• Monitoring of phase failure and asymmetry.
• Monitoring of the maximum cycling rate.
For further information, see Technical Information
CT-110.
5.4.4 SE-E2
Optional protection device for operation with frequency
inverter and soft starter (for a ramp time shorter than
1 s).
• Dimensions and integration in the control identical to
SE-E1.
• Suitable for all CS. compressors.
• Monitoring functions are basically identical to those
of SE-E1. However, the SE-E2 monitors phase fail-
ure during the entire running time of the compressor.
For further information, see Technical Information
ST-122.
5.4.5 Monitoring of the oil circuit
• For short circuits without liquid injection (LI) for addi-
tional cooling and for small system volume and small
refrigerant charge: Indirect monitoring with oil tem-
perature sensor (standard)
!
!
NOTICE
Lack of oil leads to a too high increase in tem-
perature.
Risk of damage to the compressor!
• For circuits with liquid injection (LI) for additional
cooling and / or for great system volume as well as
parallel compounding: Monitor oil level directly with
opto-electronic oil level monitoring (option), see
chapter Opto-electronic oil level monitoring OLC-D1-
S, page 26. The connection is on the compressor
housing, see chapter Connections and dimensional
drawings, page 14, position 8.
SB-170-9
77
4.3 Raccordements de tuyauterie
AVERTISSEMENT
Le compresseur est sous pression !
Risque de blessures graves.
Évacuer la pression du compresseur !
Porter des lunettes de protection !
!
!
AVIS
Risque de réactions chimiques en cas d'intro-
duction d'air !
Travailler rapidement et maintenir les vannes
d'arrêt fermées jusqu'à la mise sous vide.
4.3.1 Raccordements de tuyauterie
Les raccordements sont exécutés de façon à ce que
les tubes usuels en millimètres et en pouces puissent
être utilisés. Les raccords à braser ont plusieurs dia-
mètres successifs. Suivant la section, le tube sera insé-
ré plus ou moins profon - dément. Si nécessaire, l'ex-
trémité avec le plus grand diamètre peut être sciée.
4.3.2 Vannes d'arrêt
ATTENTION
En fonction de l'utilisation, les vannes d'arrêt
sont susceptibles d'être très froides ou très
chaudes.
Risque de brûlure ou de gelure !
Porter une protection appropriée !
!
!
AVIS
Ne pas surchauffer les vannes d'arrêt !
Refroidir les vannes et l'adaptateur de brasage
pendant et après le brasage.
Température de brasage maximale : 700°C !
Pour souder, démonter les raccords de tubes et
les douilles.
Si les vannes d'arrêt doivent être tournées ou remon-
tées :
!
!
AVIS
Risque d'endommagement du compresseur.
Serrer les vis au couple de serrage prescrit et
en croix, en 2 étapes minimum.
Avant la mise en service, essayer l'étanchéité !
Lors du montage ultérieur de la vanne d'arrêt ECO :
Information
Pour augmenter la protection anticorrosion, il
est conseillé de peindre la vanne d'arrêt ECO.
4.3.3 Conduites
En règle générale, n’utiliser que des conduites et des
composants d’installation qui
• sont propres et secs à l’intérieur (sans calamine, ni
copeaux de métal, ni couches de rouille ou de phos-
phate) et
• qui sont livrés hermétiquement fermés.
Selon la version, les compresseurs sont livrés avec des
rondelles de fermeture au niveau des raccords de tube
ou des vannes d’arrêt. Avant de contrôler la résistance
à la pression et l’étanchéité et de mettre le système en
service, il faut retirer ces rondelles.
Information
Les rondelles de fermeture ne sont conçues que
comme protection pour le transport. Elles ne
sont pas faites pour séparer les différents tron-
çons de l'installation durant l'essai de résistance
à la pression.
!
!
AVIS
Sur les installations ayant des conduites
longues ou lorsque le brasage se fait sans gaz
de protection :
Monter un filtre de nettoyage à l'aspiration (taille
des mailles < 25 µm).
!
!
AVIS
Risque d'endommagement du compresseur !
Étant donné le grand degré de sécheresse et
pour permettre une stabilisation chimique du cir-
cuit, utiliser des filtres déshydrateurs de grande
taille et de qualité appropriée (tamis molécu-
laires avec taille de pores spécifiquement adap-
tée).
Information
Pour les remarques relatives au montage de
filtres de nettoyage côté aspiration, se reporter
au manuel SH-170.
Installer les conduites de façon à ce que, quand la ma-
chine est à l’arrêt, le compresseur ne puisse pas être
inondé par l’huile ou noyé par le fluide frigorigène sous
forme liquide. Tenir compte absolument des remarques
du manuel SH-170.
Les conduites optionnelles pour l’économiseur (ECO)
(pas pour CSH95), voir figure 5, page 78 et/ou l’injec-
tion de liquide (LI), voir figure 6, page 78 doivent tout
d’abord être passées vers le haut à partir du raccord.
Cela évite le déplacement d’huile et l’endommagement
des composants à cause de pointes de pression (cf.
manuel SH-170).
4.3 Присоединение трубопроводов
ПРЕДУПРЕЖДЕНИЕ
Компрессор находится под давлением!
Возможны серьёзные повреждения.
Сбросьте давление в компрессоре!
Наденьте защитные очки!
ВНИМАНИЕ
При проникновении воздуха возможно
протекание химических реакций!
Выполняйте работы быстро. Запорные
клапаны должны оставаться закрытыми до
начала вакуумирования.
4.3.1 Присоединение трубопроводов
Соединительные элементы выполнены так, что могут
применяться трубы со стандартными размерами в
миллиметрах и дюймах. Соединительные элементы
под пайку имеют ступенчатые диаметры. Труба
вдвигается внутрь на разную глубину в зависимости
от ее диаметра. При необходимости конец патрубка с
большим диаметром также можно отрезать.
4.3.2 Запорные клапаны
ОСТОРОЖНО
В зависимости от эксплуатации запорные
клапаны могут становиться очень холодным
или очень горячими.
Опасность получения ожогов и обморожений!
Используйте соответствующее защитное
снаряжение!
ВНИМАНИЕ
Не перегревайте запорные клапаны!
Во время и после завершения пайки
охлаждайте корпус клапанов и адаптеры.
Максимальная температура пайки 700° C!
Демонтируйте трубные соединения и втулки
при сварке!
При повороте запорных клапанов или установке новых:
ВНИМАНИЕ
Опасность повреждения компрессора.
Затягивайте винты с установленным моментом
затяжки крест-накрест и как минимум в
два приема. Перед вводом в эксплуатацию
проведите проверку на плотность!
При дооснащении запорным клапаном ECO:
Информация
Для обеспечения лучшей защиты от коррозии,
рекомендуется дополнительно окрасить
запорный клапан ECO.
SB-170-9
11
4.3 Connecting the pipelines
WARNING
The compressor is under pressure!
Serious injuries are possible.
Depressurize the compressor!
Wear safety goggles!
!
!
NOTICE
Potential chemical reactions due to air penetra-
tion!
Proceed swiftly and keep shut-off valves closed
until evacuation.
4.3.1 Pipe connections
The pipe connections are suitable for pipes in all com-
mon dimensions in millimetres and inches. Brazed con-
nections have stepped diameters. The pipe will im-
merge more or less depending on its dimensions. If ne-
cessary, the bushing may even be cut at the end with
the largest diameter.
4.3.2 Shut-off valves
CAUTION
Depending on the operation mode, the shut-off
valves may become very cold or very hot.
Risk of burning or frostbite!
Wear suitable protective equipment!
!
!
NOTICE
Do not overheat the shut-off valves!
Cool the valve body and the brazing adapter
during and after the brazing operation.
Maximum brazing temperature 700°C!
For welding, dismount the pipe connections and
the bushes.
When turning or mounting shut-off valves:
!
!
NOTICE
Risk of damage to the compressor.
Tighten screws crosswise in at least 2 steps to
the prescribed tightening torque.
Test tightness before commissioning!
When retrofitting the ECO shut-off valve:
Information
To increase the corrosion protection, it is recom-
mended to coat the surface of the ECO shut-off
valve.
4.3.3 Pipelines
Use only pipelines and system components which are
• clean and dry inside (free from slag, swarf, rust and
phosphate coatings) and
• which are delivered with an air-tight seal.
Depending on the compressor versions, they are sup-
plied with blanking plates on the pipe connections or
shut-off valves. These must be removed before per-
forming the strength pressure and tightness tests and
commissioning the system.
Information
The blanking plates are only designed to serve
as a transport protection. They are not suitable
as a separation between different system sec-
tions during the strength pressure test.
!
!
NOTICE
For systems with rather long pipelines or for
brazing operations without protective gas:
Install the suction-side cleaning filter (mesh size
< 25 μm).
!
!
NOTICE
Risk of compressor damage!
Generously sized filter dryers should be used to
ensure a high degree of dehydration and to
maintain the chemical stability of the circuit.
Make sure to choose a suitable quality (molecu-
lar sieves with specially adapted pore sizes).
Information
Notice for mounting the suction-side cleaning fil-
ter, see manual SH-170.
SB-170-9
11
4.3 Connecting the pipelines
WARNING
The compressor is under pressure!
Serious injuries are possible.
Depressurize the compressor!
Wear safety goggles!
!
!
NOTICE
Potential chemical reactions due to air penetra-
tion!
Proceed swiftly and keep shut-off valves closed
until evacuation.
4.3.1 Pipe connections
The pipe connections are suitable for pipes in all com-
mon dimensions in millimetres and inches. Brazed con-
nections have stepped diameters. The pipe will im-
merge more or less depending on its dimensions. If ne-
cessary, the bushing may even be cut at the end with
the largest diameter.
4.3.2 Shut-off valves
CAUTION
Depending on the operation mode, the shut-off
valves may become very cold or very hot.
Risk of burning or frostbite!
Wear suitable protective equipment!
!
!
NOTICE
Do not overheat the shut-off valves!
Cool the valve body and the brazing adapter
during and after the brazing operation.
Maximum brazing temperature 700°C!
For welding, dismount the pipe connections and
the bushes.
When turning or mounting shut-off valves:
!
!
NOTICE
Risk of damage to the compressor.
Tighten screws crosswise in at least 2 steps to
the prescribed tightening torque.
Test tightness before commissioning!
When retrofitting the ECO shut-off valve:
Information
To increase the corrosion protection, it is recom-
mended to coat the surface of the ECO shut-off
valve.
4.3.3 Pipelines
Use only pipelines and system components which are
• clean and dry inside (free from slag, swarf, rust and
phosphate coatings) and
• which are delivered with an air-tight seal.
Depending on the compressor versions, they are sup-
plied with blanking plates on the pipe connections or
shut-off valves. These must be removed before per-
forming the strength pressure and tightness tests and
commissioning the system.
Information
The blanking plates are only designed to serve
as a transport protection. They are not suitable
as a separation between different system sec-
tions during the strength pressure test.
!
!
NOTICE
For systems with rather long pipelines or for
brazing operations without protective gas:
Install the suction-side cleaning filter (mesh size
< 25 μm).
!
!
NOTICE
Risk of compressor damage!
Generously sized filter dryers should be used to
ensure a high degree of dehydration and to
maintain the chemical stability of the circuit.
Make sure to choose a suitable quality (molecu-
lar sieves with specially adapted pore sizes).
Information
Notice for mounting the suction-side cleaning fil-
ter, see manual SH-170.
SB-170-9
11
4.3 Connecting the pipelines
WARNING
The compressor is under pressure!
Serious injuries are possible.
Depressurize the compressor!
Wear safety goggles!
!
!
NOTICE
Potential chemical reactions due to air penetra-
tion!
Proceed swiftly and keep shut-off valves closed
until evacuation.
4.3.1 Pipe connections
The pipe connections are suitable for pipes in all com-
mon dimensions in millimetres and inches. Brazed con-
nections have stepped diameters. The pipe will im-
merge more or less depending on its dimensions. If ne-
cessary, the bushing may even be cut at the end with
the largest diameter.
4.3.2 Shut-off valves
CAUTION
Depending on the operation mode, the shut-off
valves may become very cold or very hot.
Risk of burning or frostbite!
Wear suitable protective equipment!
!
!
NOTICE
Do not overheat the shut-off valves!
Cool the valve body and the brazing adapter
during and after the brazing operation.
Maximum brazing temperature 700°C!
For welding, dismount the pipe connections and
the bushes.
When turning or mounting shut-off valves:
!
!
NOTICE
Risk of damage to the compressor.
Tighten screws crosswise in at least 2 steps to
the prescribed tightening torque.
Test tightness before commissioning!
When retrofitting the ECO shut-off valve:
Information
To increase the corrosion protection, it is recom-
mended to coat the surface of the ECO shut-off
valve.
4.3.3 Pipelines
Use only pipelines and system components which are
• clean and dry inside (free from slag, swarf, rust and
phosphate coatings) and
• which are delivered with an air-tight seal.
Depending on the compressor versions, they are sup-
plied with blanking plates on the pipe connections or
shut-off valves. These must be removed before per-
forming the strength pressure and tightness tests and
commissioning the system.
Information
The blanking plates are only designed to serve
as a transport protection. They are not suitable
as a separation between different system sec-
tions during the strength pressure test.
!
!
NOTICE
For systems with rather long pipelines or for
brazing operations without protective gas:
Install the suction-side cleaning filter (mesh size
< 25 μm).
!
!
NOTICE
Risk of compressor damage!
Generously sized filter dryers should be used to
ensure a high degree of dehydration and to
maintain the chemical stability of the circuit.
Make sure to choose a suitable quality (molecu-
lar sieves with specially adapted pore sizes).
Information
Notice for mounting the suction-side cleaning fil-
ter, see manual SH-170.
SB-170-9
11
4.3 Connecting the pipelines
WARNING
The compressor is under pressure!
Serious injuries are possible.
Depressurize the compressor!
Wear safety goggles!
!
!
NOTICE
Potential chemical reactions due to air penetra-
tion!
Proceed swiftly and keep shut-off valves closed
until evacuation.
4.3.1 Pipe connections
The pipe connections are suitable for pipes in all com-
mon dimensions in millimetres and inches. Brazed con-
nections have stepped diameters. The pipe will im-
merge more or less depending on its dimensions. If ne-
cessary, the bushing may even be cut at the end with
the largest diameter.
4.3.2 Shut-off valves
CAUTION
Depending on the operation mode, the shut-off
valves may become very cold or very hot.
Risk of burning or frostbite!
Wear suitable protective equipment!
!
!
NOTICE
Do not overheat the shut-off valves!
Cool the valve body and the brazing adapter
during and after the brazing operation.
Maximum brazing temperature 700°C!
For welding, dismount the pipe connections and
the bushes.
When turning or mounting shut-off valves:
!
!
NOTICE
Risk of damage to the compressor.
Tighten screws crosswise in at least 2 steps to
the prescribed tightening torque.
Test tightness before commissioning!
When retrofitting the ECO shut-off valve:
Information
To increase the corrosion protection, it is recom-
mended to coat the surface of the ECO shut-off
valve.
4.3.3 Pipelines
Use only pipelines and system components which are
• clean and dry inside (free from slag, swarf, rust and
phosphate coatings) and
• which are delivered with an air-tight seal.
Depending on the compressor versions, they are sup-
plied with blanking plates on the pipe connections or
shut-off valves. These must be removed before per-
forming the strength pressure and tightness tests and
commissioning the system.
Information
The blanking plates are only designed to serve
as a transport protection. They are not suitable
as a separation between different system sec-
tions during the strength pressure test.
!
!
NOTICE
For systems with rather long pipelines or for
brazing operations without protective gas:
Install the suction-side cleaning filter (mesh size
< 25 μm).
!
!
NOTICE
Risk of compressor damage!
Generously sized filter dryers should be used to
ensure a high degree of dehydration and to
maintain the chemical stability of the circuit.
Make sure to choose a suitable quality (molecu-
lar sieves with specially adapted pore sizes).
Information
Notice for mounting the suction-side cleaning fil-
ter, see manual SH-170.
4.3.3 Трубопроводы
Используйте только трубопроводы и компоненты,
которые
• чистые и сухие внутри (отсутствуют частицы
окалины, металлической стружки, ржавчины и
фосфатных покрытий) и
• поставляются с герметичными заглушками.
В зависимости от варианта исполнения компрессоры
поставляются с заглушками на трубопроводных
присоединениях или с запорными клапанами. Перед
проведением испытаний на прочность давлением и на
плотность, а также перед вводом в эксплуатацию их
следует удалить.
Информация
Заглушки предназначены исключительно для
защиты при транспортировке. Они не подходят
для разделения отдельных участков системы
при проведении испытания на прочность
давлением.
ВНИМАНИЕ
В системах с трубами значительной длины,
а также с трубопроводами, паянными без
защитного газа, устанавливаются фильтры
тонкой очистки на всасывании (размер ячеек
<25 μm).
ВНИМАНИЕ
Возможно повреждение компрессора!
Для обеспечения высокой степени осушения
холодильного контура и для поддержания
химической стабильности системы следует
применять высококачественные фильтры-
осушители большой емкости (молекулярные
фильтры со специально подобранным
размером ячеек).
Информация
Рекомендации по установке фильтра
тонкой очистки на стороне всасывания см. в
руководстве по применению SH-170.
Трубопроводы должны монтироваться таким образом,
чтобы исключить возможность залива компрессора
маслом или жидким хладагентом во время стоянки.
Соблюдайте рекомендации руководства SH-170.
Опциональные линии экономайзера (ECO) (не для
CSH95), см. рис. 5, стр. 78 и/или впрыска жидкости
(LI), см. рис. 6, стр. 78 должны быть направлены
вертикально вверх от места присоединения. Это
предотвращает миграцию масла и повреждение
компонентов вследствие гидравлических ударов (см.
руководство SH-170).
SB-170-9
11
4.3 Connecting the pipelines
WARNING
The compressor is under pressure!
Serious injuries are possible.
Depressurize the compressor!
Wear safety goggles!
!
!
NOTICE
Potential chemical reactions due to air penetra-
tion!
Proceed swiftly and keep shut-off valves closed
until evacuation.
4.3.1 Pipe connections
The pipe connections are suitable for pipes in all com-
mon dimensions in millimetres and inches. Brazed con-
nections have stepped diameters. The pipe will im-
merge more or less depending on its dimensions. If ne-
cessary, the bushing may even be cut at the end with
the largest diameter.
4.3.2 Shut-off valves
CAUTION
Depending on the operation mode, the shut-off
valves may become very cold or very hot.
Risk of burning or frostbite!
Wear suitable protective equipment!
!
!
NOTICE
Do not overheat the shut-off valves!
Cool the valve body and the brazing adapter
during and after the brazing operation.
Maximum brazing temperature 700°C!
For welding, dismount the pipe connections and
the bushes.
When turning or mounting shut-off valves:
!
!
NOTICE
Risk of damage to the compressor.
Tighten screws crosswise in at least 2 steps to
the prescribed tightening torque.
Test tightness before commissioning!
When retrofitting the ECO shut-off valve:
Information
To increase the corrosion protection, it is recom-
mended to coat the surface of the ECO shut-off
valve.
4.3.3 Pipelines
Use only pipelines and system components which are
• clean and dry inside (free from slag, swarf, rust and
phosphate coatings) and
• which are delivered with an air-tight seal.
Depending on the compressor versions, they are sup-
plied with blanking plates on the pipe connections or
shut-off valves. These must be removed before per-
forming the strength pressure and tightness tests and
commissioning the system.
Information
The blanking plates are only designed to serve
as a transport protection. They are not suitable
as a separation between different system sec-
tions during the strength pressure test.
!
!
NOTICE
For systems with rather long pipelines or for
brazing operations without protective gas:
Install the suction-side cleaning filter (mesh size
< 25 μm).
!
!
NOTICE
Risk of compressor damage!
Generously sized filter dryers should be used to
ensure a high degree of dehydration and to
maintain the chemical stability of the circuit.
Make sure to choose a suitable quality (molecu-
lar sieves with specially adapted pore sizes).
Information
Notice for mounting the suction-side cleaning fil-
ter, see manual SH-170.
SB-170-9
11
4.3 Connecting the pipelines
WARNING
The compressor is under pressure!
Serious injuries are possible.
Depressurize the compressor!
Wear safety goggles!
!
!
NOTICE
Potential chemical reactions due to air penetra-
tion!
Proceed swiftly and keep shut-off valves closed
until evacuation.
4.3.1 Pipe connections
The pipe connections are suitable for pipes in all com-
mon dimensions in millimetres and inches. Brazed con-
nections have stepped diameters. The pipe will im-
merge more or less depending on its dimensions. If ne-
cessary, the bushing may even be cut at the end with
the largest diameter.
4.3.2 Shut-off valves
CAUTION
Depending on the operation mode, the shut-off
valves may become very cold or very hot.
Risk of burning or frostbite!
Wear suitable protective equipment!
!
!
NOTICE
Do not overheat the shut-off valves!
Cool the valve body and the brazing adapter
during and after the brazing operation.
Maximum brazing temperature 700°C!
For welding, dismount the pipe connections and
the bushes.
When turning or mounting shut-off valves:
!
!
NOTICE
Risk of damage to the compressor.
Tighten screws crosswise in at least 2 steps to
the prescribed tightening torque.
Test tightness before commissioning!
When retrofitting the ECO shut-off valve:
Information
To increase the corrosion protection, it is recom-
mended to coat the surface of the ECO shut-off
valve.
4.3.3 Pipelines
Use only pipelines and system components which are
• clean and dry inside (free from slag, swarf, rust and
phosphate coatings) and
• which are delivered with an air-tight seal.
Depending on the compressor versions, they are sup-
plied with blanking plates on the pipe connections or
shut-off valves. These must be removed before per-
forming the strength pressure and tightness tests and
commissioning the system.
Information
The blanking plates are only designed to serve
as a transport protection. They are not suitable
as a separation between different system sec-
tions during the strength pressure test.
!
!
NOTICE
For systems with rather long pipelines or for
brazing operations without protective gas:
Install the suction-side cleaning filter (mesh size
< 25 μm).
!
!
NOTICE
Risk of compressor damage!
Generously sized filter dryers should be used to
ensure a high degree of dehydration and to
maintain the chemical stability of the circuit.
Make sure to choose a suitable quality (molecu-
lar sieves with specially adapted pore sizes).
Information
Notice for mounting the suction-side cleaning fil-
ter, see manual SH-170.
SB-170-9
11
4.3 Connecting the pipelines
WARNING
The compressor is under pressure!
Serious injuries are possible.
Depressurize the compressor!
Wear safety goggles!
!
!
NOTICE
Potential chemical reactions due to air penetra-
tion!
Proceed swiftly and keep shut-off valves closed
until evacuation.
4.3.1 Pipe connections
The pipe connections are suitable for pipes in all com-
mon dimensions in millimetres and inches. Brazed con-
nections have stepped diameters. The pipe will im-
merge more or less depending on its dimensions. If ne-
cessary, the bushing may even be cut at the end with
the largest diameter.
4.3.2 Shut-off valves
CAUTION
Depending on the operation mode, the shut-off
valves may become very cold or very hot.
Risk of burning or frostbite!
Wear suitable protective equipment!
!
!
NOTICE
Do not overheat the shut-off valves!
Cool the valve body and the brazing adapter
during and after the brazing operation.
Maximum brazing temperature 700°C!
For welding, dismount the pipe connections and
the bushes.
When turning or mounting shut-off valves:
!
!
NOTICE
Risk of damage to the compressor.
Tighten screws crosswise in at least 2 steps to
the prescribed tightening torque.
Test tightness before commissioning!
When retrofitting the ECO shut-off valve:
Information
To increase the corrosion protection, it is recom-
mended to coat the surface of the ECO shut-off
valve.
4.3.3 Pipelines
Use only pipelines and system components which are
• clean and dry inside (free from slag, swarf, rust and
phosphate coatings) and
• which are delivered with an air-tight seal.
Depending on the compressor versions, they are sup-
plied with blanking plates on the pipe connections or
shut-off valves. These must be removed before per-
forming the strength pressure and tightness tests and
commissioning the system.
Information
The blanking plates are only designed to serve
as a transport protection. They are not suitable
as a separation between different system sec-
tions during the strength pressure test.
!
!
NOTICE
For systems with rather long pipelines or for
brazing operations without protective gas:
Install the suction-side cleaning filter (mesh size
< 25 μm).
!
!
NOTICE
Risk of compressor damage!
Generously sized filter dryers should be used to
ensure a high degree of dehydration and to
maintain the chemical stability of the circuit.
Make sure to choose a suitable quality (molecu-
lar sieves with specially adapted pore sizes).
Information
Notice for mounting the suction-side cleaning fil-
ter, see manual SH-170.
SB-170-9
11
4.3 Connecting the pipelines
WARNING
The compressor is under pressure!
Serious injuries are possible.
Depressurize the compressor!
Wear safety goggles!
!
!
NOTICE
Potential chemical reactions due to air penetra-
tion!
Proceed swiftly and keep shut-off valves closed
until evacuation.
4.3.1 Pipe connections
The pipe connections are suitable for pipes in all com-
mon dimensions in millimetres and inches. Brazed con-
nections have stepped diameters. The pipe will im-
merge more or less depending on its dimensions. If ne-
cessary, the bushing may even be cut at the end with
the largest diameter.
4.3.2 Shut-off valves
CAUTION
Depending on the operation mode, the shut-off
valves may become very cold or very hot.
Risk of burning or frostbite!
Wear suitable protective equipment!
!
!
NOTICE
Do not overheat the shut-off valves!
Cool the valve body and the brazing adapter
during and after the brazing operation.
Maximum brazing temperature 700°C!
For welding, dismount the pipe connections and
the bushes.
When turning or mounting shut-off valves:
!
!
NOTICE
Risk of damage to the compressor.
Tighten screws crosswise in at least 2 steps to
the prescribed tightening torque.
Test tightness before commissioning!
When retrofitting the ECO shut-off valve:
Information
To increase the corrosion protection, it is recom-
mended to coat the surface of the ECO shut-off
valve.
4.3.3 Pipelines
Use only pipelines and system components which are
• clean and dry inside (free from slag, swarf, rust and
phosphate coatings) and
• which are delivered with an air-tight seal.
Depending on the compressor versions, they are sup-
plied with blanking plates on the pipe connections or
shut-off valves. These must be removed before per-
forming the strength pressure and tightness tests and
commissioning the system.
Information
The blanking plates are only designed to serve
as a transport protection. They are not suitable
as a separation between different system sec-
tions during the strength pressure test.
!
!
NOTICE
For systems with rather long pipelines or for
brazing operations without protective gas:
Install the suction-side cleaning filter (mesh size
< 25 μm).
!
!
NOTICE
Risk of compressor damage!
Generously sized filter dryers should be used to
ensure a high degree of dehydration and to
maintain the chemical stability of the circuit.
Make sure to choose a suitable quality (molecu-
lar sieves with specially adapted pore sizes).
Information
Notice for mounting the suction-side cleaning fil-
ter, see manual SH-170.
SB-170-9
11
4.3 Connecting the pipelines
WARNING
The compressor is under pressure!
Serious injuries are possible.
Depressurize the compressor!
Wear safety goggles!
!
!
NOTICE
Potential chemical reactions due to air penetra-
tion!
Proceed swiftly and keep shut-off valves closed
until evacuation.
4.3.1 Pipe connections
The pipe connections are suitable for pipes in all com-
mon dimensions in millimetres and inches. Brazed con-
nections have stepped diameters. The pipe will im-
merge more or less depending on its dimensions. If ne-
cessary, the bushing may even be cut at the end with
the largest diameter.
4.3.2 Shut-off valves
CAUTION
Depending on the operation mode, the shut-off
valves may become very cold or very hot.
Risk of burning or frostbite!
Wear suitable protective equipment!
!
!
NOTICE
Do not overheat the shut-off valves!
Cool the valve body and the brazing adapter
during and after the brazing operation.
Maximum brazing temperature 700°C!
For welding, dismount the pipe connections and
the bushes.
When turning or mounting shut-off valves:
!
!
NOTICE
Risk of damage to the compressor.
Tighten screws crosswise in at least 2 steps to
the prescribed tightening torque.
Test tightness before commissioning!
When retrofitting the ECO shut-off valve:
Information
To increase the corrosion protection, it is recom-
mended to coat the surface of the ECO shut-off
valve.
4.3.3 Pipelines
Use only pipelines and system components which are
• clean and dry inside (free from slag, swarf, rust and
phosphate coatings) and
• which are delivered with an air-tight seal.
Depending on the compressor versions, they are sup-
plied with blanking plates on the pipe connections or
shut-off valves. These must be removed before per-
forming the strength pressure and tightness tests and
commissioning the system.
Information
The blanking plates are only designed to serve
as a transport protection. They are not suitable
as a separation between different system sec-
tions during the strength pressure test.
!
!
NOTICE
For systems with rather long pipelines or for
brazing operations without protective gas:
Install the suction-side cleaning filter (mesh size
< 25 μm).
!
!
NOTICE
Risk of compressor damage!
Generously sized filter dryers should be used to
ensure a high degree of dehydration and to
maintain the chemical stability of the circuit.
Make sure to choose a suitable quality (molecu-
lar sieves with specially adapted pore sizes).
Information
Notice for mounting the suction-side cleaning fil-
ter, see manual SH-170.
SB-170-9
11
4.3 Connecting the pipelines
WARNING
The compressor is under pressure!
Serious injuries are possible.
Depressurize the compressor!
Wear safety goggles!
!
!
NOTICE
Potential chemical reactions due to air penetra-
tion!
Proceed swiftly and keep shut-off valves closed
until evacuation.
4.3.1 Pipe connections
The pipe connections are suitable for pipes in all com-
mon dimensions in millimetres and inches. Brazed con-
nections have stepped diameters. The pipe will im-
merge more or less depending on its dimensions. If ne-
cessary, the bushing may even be cut at the end with
the largest diameter.
4.3.2 Shut-off valves
CAUTION
Depending on the operation mode, the shut-off
valves may become very cold or very hot.
Risk of burning or frostbite!
Wear suitable protective equipment!
!
!
NOTICE
Do not overheat the shut-off valves!
Cool the valve body and the brazing adapter
during and after the brazing operation.
Maximum brazing temperature 700°C!
For welding, dismount the pipe connections and
the bushes.
When turning or mounting shut-off valves:
!
!
NOTICE
Risk of damage to the compressor.
Tighten screws crosswise in at least 2 steps to
the prescribed tightening torque.
Test tightness before commissioning!
When retrofitting the ECO shut-off valve:
Information
To increase the corrosion protection, it is recom-
mended to coat the surface of the ECO shut-off
valve.
4.3.3 Pipelines
Use only pipelines and system components which are
• clean and dry inside (free from slag, swarf, rust and
phosphate coatings) and
• which are delivered with an air-tight seal.
Depending on the compressor versions, they are sup-
plied with blanking plates on the pipe connections or
shut-off valves. These must be removed before per-
forming the strength pressure and tightness tests and
commissioning the system.
Information
The blanking plates are only designed to serve
as a transport protection. They are not suitable
as a separation between different system sec-
tions during the strength pressure test.
!
!
NOTICE
For systems with rather long pipelines or for
brazing operations without protective gas:
Install the suction-side cleaning filter (mesh size
< 25 μm).
!
!
NOTICE
Risk of compressor damage!
Generously sized filter dryers should be used to
ensure a high degree of dehydration and to
maintain the chemical stability of the circuit.
Make sure to choose a suitable quality (molecu-
lar sieves with specially adapted pore sizes).
Information
Notice for mounting the suction-side cleaning fil-
ter, see manual SH-170.
SB-170-9
11
4.3 Connecting the pipelines
WARNING
The compressor is under pressure!
Serious injuries are possible.
Depressurize the compressor!
Wear safety goggles!
!
!
NOTICE
Potential chemical reactions due to air penetra-
tion!
Proceed swiftly and keep shut-off valves closed
until evacuation.
4.3.1 Pipe connections
The pipe connections are suitable for pipes in all com-
mon dimensions in millimetres and inches. Brazed con-
nections have stepped diameters. The pipe will im-
merge more or less depending on its dimensions. If ne-
cessary, the bushing may even be cut at the end with
the largest diameter.
4.3.2 Shut-off valves
CAUTION
Depending on the operation mode, the shut-off
valves may become very cold or very hot.
Risk of burning or frostbite!
Wear suitable protective equipment!
!
!
NOTICE
Do not overheat the shut-off valves!
Cool the valve body and the brazing adapter
during and after the brazing operation.
Maximum brazing temperature 700°C!
For welding, dismount the pipe connections and
the bushes.
When turning or mounting shut-off valves:
!
!
NOTICE
Risk of damage to the compressor.
Tighten screws crosswise in at least 2 steps to
the prescribed tightening torque.
Test tightness before commissioning!
When retrofitting the ECO shut-off valve:
Information
To increase the corrosion protection, it is recom-
mended to coat the surface of the ECO shut-off
valve.
4.3.3 Pipelines
Use only pipelines and system components which are
• clean and dry inside (free from slag, swarf, rust and
phosphate coatings) and
• which are delivered with an air-tight seal.
Depending on the compressor versions, they are sup-
plied with blanking plates on the pipe connections or
shut-off valves. These must be removed before per-
forming the strength pressure and tightness tests and
commissioning the system.
Information
The blanking plates are only designed to serve
as a transport protection. They are not suitable
as a separation between different system sec-
tions during the strength pressure test.
!
!
NOTICE
For systems with rather long pipelines or for
brazing operations without protective gas:
Install the suction-side cleaning filter (mesh size
< 25 μm).
!
!
NOTICE
Risk of compressor damage!
Generously sized filter dryers should be used to
ensure a high degree of dehydration and to
maintain the chemical stability of the circuit.
Make sure to choose a suitable quality (molecu-
lar sieves with specially adapted pore sizes).
Information
Notice for mounting the suction-side cleaning fil-
ter, see manual SH-170.
SB-170-9
11
4.3 Connecting the pipelines
WARNING
The compressor is under pressure!
Serious injuries are possible.
Depressurize the compressor!
Wear safety goggles!
!
!
NOTICE
Potential chemical reactions due to air penetra-
tion!
Proceed swiftly and keep shut-off valves closed
until evacuation.
4.3.1 Pipe connections
The pipe connections are suitable for pipes in all com-
mon dimensions in millimetres and inches. Brazed con-
nections have stepped diameters. The pipe will im-
merge more or less depending on its dimensions. If ne-
cessary, the bushing may even be cut at the end with
the largest diameter.
4.3.2 Shut-off valves
CAUTION
Depending on the operation mode, the shut-off
valves may become very cold or very hot.
Risk of burning or frostbite!
Wear suitable protective equipment!
!
!
NOTICE
Do not overheat the shut-off valves!
Cool the valve body and the brazing adapter
during and after the brazing operation.
Maximum brazing temperature 700°C!
For welding, dismount the pipe connections and
the bushes.
When turning or mounting shut-off valves:
!
!
NOTICE
Risk of damage to the compressor.
Tighten screws crosswise in at least 2 steps to
the prescribed tightening torque.
Test tightness before commissioning!
When retrofitting the ECO shut-off valve:
Information
To increase the corrosion protection, it is recom-
mended to coat the surface of the ECO shut-off
valve.
4.3.3 Pipelines
Use only pipelines and system components which are
• clean and dry inside (free from slag, swarf, rust and
phosphate coatings) and
• which are delivered with an air-tight seal.
Depending on the compressor versions, they are sup-
plied with blanking plates on the pipe connections or
shut-off valves. These must be removed before per-
forming the strength pressure and tightness tests and
commissioning the system.
Information
The blanking plates are only designed to serve
as a transport protection. They are not suitable
as a separation between different system sec-
tions during the strength pressure test.
!
!
NOTICE
For systems with rather long pipelines or for
brazing operations without protective gas:
Install the suction-side cleaning filter (mesh size
< 25 μm).
!
!
NOTICE
Risk of compressor damage!
Generously sized filter dryers should be used to
ensure a high degree of dehydration and to
maintain the chemical stability of the circuit.
Make sure to choose a suitable quality (molecu-
lar sieves with specially adapted pore sizes).
Information
Notice for mounting the suction-side cleaning fil-
ter, see manual SH-170.
SB-170-9
11
4.3 Connecting the pipelines
WARNING
The compressor is under pressure!
Serious injuries are possible.
Depressurize the compressor!
Wear safety goggles!
!
!
NOTICE
Potential chemical reactions due to air penetra-
tion!
Proceed swiftly and keep shut-off valves closed
until evacuation.
4.3.1 Pipe connections
The pipe connections are suitable for pipes in all com-
mon dimensions in millimetres and inches. Brazed con-
nections have stepped diameters. The pipe will im-
merge more or less depending on its dimensions. If ne-
cessary, the bushing may even be cut at the end with
the largest diameter.
4.3.2 Shut-off valves
CAUTION
Depending on the operation mode, the shut-off
valves may become very cold or very hot.
Risk of burning or frostbite!
Wear suitable protective equipment!
!
!
NOTICE
Do not overheat the shut-off valves!
Cool the valve body and the brazing adapter
during and after the brazing operation.
Maximum brazing temperature 700°C!
For welding, dismount the pipe connections and
the bushes.
When turning or mounting shut-off valves:
!
!
NOTICE
Risk of damage to the compressor.
Tighten screws crosswise in at least 2 steps to
the prescribed tightening torque.
Test tightness before commissioning!
When retrofitting the ECO shut-off valve:
Information
To increase the corrosion protection, it is recom-
mended to coat the surface of the ECO shut-off
valve.
4.3.3 Pipelines
Use only pipelines and system components which are
• clean and dry inside (free from slag, swarf, rust and
phosphate coatings) and
• which are delivered with an air-tight seal.
Depending on the compressor versions, they are sup-
plied with blanking plates on the pipe connections or
shut-off valves. These must be removed before per-
forming the strength pressure and tightness tests and
commissioning the system.
Information
The blanking plates are only designed to serve
as a transport protection. They are not suitable
as a separation between different system sec-
tions during the strength pressure test.
!
!
NOTICE
For systems with rather long pipelines or for
brazing operations without protective gas:
Install the suction-side cleaning filter (mesh size
< 25 μm).
!
!
NOTICE
Risk of compressor damage!
Generously sized filter dryers should be used to
ensure a high degree of dehydration and to
maintain the chemical stability of the circuit.
Make sure to choose a suitable quality (molecu-
lar sieves with specially adapted pore sizes).
Information
Notice for mounting the suction-side cleaning fil-
ter, see manual SH-170.
SB-170-9
11
4.3 Connecting the pipelines
WARNING
The compressor is under pressure!
Serious injuries are possible.
Depressurize the compressor!
Wear safety goggles!
!
!
NOTICE
Potential chemical reactions due to air penetra-
tion!
Proceed swiftly and keep shut-off valves closed
until evacuation.
4.3.1 Pipe connections
The pipe connections are suitable for pipes in all com-
mon dimensions in millimetres and inches. Brazed con-
nections have stepped diameters. The pipe will im-
merge more or less depending on its dimensions. If ne-
cessary, the bushing may even be cut at the end with
the largest diameter.
4.3.2 Shut-off valves
CAUTION
Depending on the operation mode, the shut-off
valves may become very cold or very hot.
Risk of burning or frostbite!
Wear suitable protective equipment!
!
!
NOTICE
Do not overheat the shut-off valves!
Cool the valve body and the brazing adapter
during and after the brazing operation.
Maximum brazing temperature 700°C!
For welding, dismount the pipe connections and
the bushes.
When turning or mounting shut-off valves:
!
!
NOTICE
Risk of damage to the compressor.
Tighten screws crosswise in at least 2 steps to
the prescribed tightening torque.
Test tightness before commissioning!
When retrofitting the ECO shut-off valve:
Information
To increase the corrosion protection, it is recom-
mended to coat the surface of the ECO shut-off
valve.
4.3.3 Pipelines
Use only pipelines and system components which are
• clean and dry inside (free from slag, swarf, rust and
phosphate coatings) and
• which are delivered with an air-tight seal.
Depending on the compressor versions, they are sup-
plied with blanking plates on the pipe connections or
shut-off valves. These must be removed before per-
forming the strength pressure and tightness tests and
commissioning the system.
Information
The blanking plates are only designed to serve
as a transport protection. They are not suitable
as a separation between different system sec-
tions during the strength pressure test.
!
!
NOTICE
For systems with rather long pipelines or for
brazing operations without protective gas:
Install the suction-side cleaning filter (mesh size
< 25 μm).
!
!
NOTICE
Risk of compressor damage!
Generously sized filter dryers should be used to
ensure a high degree of dehydration and to
maintain the chemical stability of the circuit.
Make sure to choose a suitable quality (molecu-
lar sieves with specially adapted pore sizes).
Information
Notice for mounting the suction-side cleaning fil-
ter, see manual SH-170.
SB-170-9
11
4.3 Connecting the pipelines
WARNING
The compressor is under pressure!
Serious injuries are possible.
Depressurize the compressor!
Wear safety goggles!
!
!
NOTICE
Potential chemical reactions due to air penetra-
tion!
Proceed swiftly and keep shut-off valves closed
until evacuation.
4.3.1 Pipe connections
The pipe connections are suitable for pipes in all com-
mon dimensions in millimetres and inches. Brazed con-
nections have stepped diameters. The pipe will im-
merge more or less depending on its dimensions. If ne-
cessary, the bushing may even be cut at the end with
the largest diameter.
4.3.2 Shut-off valves
CAUTION
Depending on the operation mode, the shut-off
valves may become very cold or very hot.
Risk of burning or frostbite!
Wear suitable protective equipment!
!
!
NOTICE
Do not overheat the shut-off valves!
Cool the valve body and the brazing adapter
during and after the brazing operation.
Maximum brazing temperature 700°C!
For welding, dismount the pipe connections and
the bushes.
When turning or mounting shut-off valves:
!
!
NOTICE
Risk of damage to the compressor.
Tighten screws crosswise in at least 2 steps to
the prescribed tightening torque.
Test tightness before commissioning!
When retrofitting the ECO shut-off valve:
Information
To increase the corrosion protection, it is recom-
mended to coat the surface of the ECO shut-off
valve.
4.3.3 Pipelines
Use only pipelines and system components which are
• clean and dry inside (free from slag, swarf, rust and
phosphate coatings) and
• which are delivered with an air-tight seal.
Depending on the compressor versions, they are sup-
plied with blanking plates on the pipe connections or
shut-off valves. These must be removed before per-
forming the strength pressure and tightness tests and
commissioning the system.
Information
The blanking plates are only designed to serve
as a transport protection. They are not suitable
as a separation between different system sec-
tions during the strength pressure test.
!
!
NOTICE
For systems with rather long pipelines or for
brazing operations without protective gas:
Install the suction-side cleaning filter (mesh size
< 25 μm).
!
!
NOTICE
Risk of compressor damage!
Generously sized filter dryers should be used to
ensure a high degree of dehydration and to
maintain the chemical stability of the circuit.
Make sure to choose a suitable quality (molecu-
lar sieves with specially adapted pore sizes).
Information
Notice for mounting the suction-side cleaning fil-
ter, see manual SH-170.
SB-170-9
11
4.3 Connecting the pipelines
WARNING
The compressor is under pressure!
Serious injuries are possible.
Depressurize the compressor!
Wear safety goggles!
!
!
NOTICE
Potential chemical reactions due to air penetra-
tion!
Proceed swiftly and keep shut-off valves closed
until evacuation.
4.3.1 Pipe connections
The pipe connections are suitable for pipes in all com-
mon dimensions in millimetres and inches. Brazed con-
nections have stepped diameters. The pipe will im-
merge more or less depending on its dimensions. If ne-
cessary, the bushing may even be cut at the end with
the largest diameter.
4.3.2 Shut-off valves
CAUTION
Depending on the operation mode, the shut-off
valves may become very cold or very hot.
Risk of burning or frostbite!
Wear suitable protective equipment!
!
!
NOTICE
Do not overheat the shut-off valves!
Cool the valve body and the brazing adapter
during and after the brazing operation.
Maximum brazing temperature 700°C!
For welding, dismount the pipe connections and
the bushes.
When turning or mounting shut-off valves:
!
!
NOTICE
Risk of damage to the compressor.
Tighten screws crosswise in at least 2 steps to
the prescribed tightening torque.
Test tightness before commissioning!
When retrofitting the ECO shut-off valve:
Information
To increase the corrosion protection, it is recom-
mended to coat the surface of the ECO shut-off
valve.
4.3.3 Pipelines
Use only pipelines and system components which are
• clean and dry inside (free from slag, swarf, rust and
phosphate coatings) and
• which are delivered with an air-tight seal.
Depending on the compressor versions, they are sup-
plied with blanking plates on the pipe connections or
shut-off valves. These must be removed before per-
forming the strength pressure and tightness tests and
commissioning the system.
Information
The blanking plates are only designed to serve
as a transport protection. They are not suitable
as a separation between different system sec-
tions during the strength pressure test.
!
!
NOTICE
For systems with rather long pipelines or for
brazing operations without protective gas:
Install the suction-side cleaning filter (mesh size
< 25 μm).
!
!
NOTICE
Risk of compressor damage!
Generously sized filter dryers should be used to
ensure a high degree of dehydration and to
maintain the chemical stability of the circuit.
Make sure to choose a suitable quality (molecu-
lar sieves with specially adapted pore sizes).
Information
Notice for mounting the suction-side cleaning fil-
ter, see manual SH-170.
SB-170-9
11
4.3 Connecting the pipelines
WARNING
The compressor is under pressure!
Serious injuries are possible.
Depressurize the compressor!
Wear safety goggles!
!
!
NOTICE
Potential chemical reactions due to air penetra-
tion!
Proceed swiftly and keep shut-off valves closed
until evacuation.
4.3.1 Pipe connections
The pipe connections are suitable for pipes in all com-
mon dimensions in millimetres and inches. Brazed con-
nections have stepped diameters. The pipe will im-
merge more or less depending on its dimensions. If ne-
cessary, the bushing may even be cut at the end with
the largest diameter.
4.3.2 Shut-off valves
CAUTION
Depending on the operation mode, the shut-off
valves may become very cold or very hot.
Risk of burning or frostbite!
Wear suitable protective equipment!
!
!
NOTICE
Do not overheat the shut-off valves!
Cool the valve body and the brazing adapter
during and after the brazing operation.
Maximum brazing temperature 700°C!
For welding, dismount the pipe connections and
the bushes.
When turning or mounting shut-off valves:
!
!
NOTICE
Risk of damage to the compressor.
Tighten screws crosswise in at least 2 steps to
the prescribed tightening torque.
Test tightness before commissioning!
When retrofitting the ECO shut-off valve:
Information
To increase the corrosion protection, it is recom-
mended to coat the surface of the ECO shut-off
valve.
4.3.3 Pipelines
Use only pipelines and system components which are
• clean and dry inside (free from slag, swarf, rust and
phosphate coatings) and
• which are delivered with an air-tight seal.
Depending on the compressor versions, they are sup-
plied with blanking plates on the pipe connections or
shut-off valves. These must be removed before per-
forming the strength pressure and tightness tests and
commissioning the system.
Information
The blanking plates are only designed to serve
as a transport protection. They are not suitable
as a separation between different system sec-
tions during the strength pressure test.
!
!
NOTICE
For systems with rather long pipelines or for
brazing operations without protective gas:
Install the suction-side cleaning filter (mesh size
< 25 μm).
!
!
NOTICE
Risk of compressor damage!
Generously sized filter dryers should be used to
ensure a high degree of dehydration and to
maintain the chemical stability of the circuit.
Make sure to choose a suitable quality (molecu-
lar sieves with specially adapted pore sizes).
Information
Notice for mounting the suction-side cleaning fil-
ter, see manual SH-170.
SB-170-9
11
4.3 Connecting the pipelines
WARNING
The compressor is under pressure!
Serious injuries are possible.
Depressurize the compressor!
Wear safety goggles!
!
!
NOTICE
Potential chemical reactions due to air penetra-
tion!
Proceed swiftly and keep shut-off valves closed
until evacuation.
4.3.1 Pipe connections
The pipe connections are suitable for pipes in all com-
mon dimensions in millimetres and inches. Brazed con-
nections have stepped diameters. The pipe will im-
merge more or less depending on its dimensions. If ne-
cessary, the bushing may even be cut at the end with
the largest diameter.
4.3.2 Shut-off valves
CAUTION
Depending on the operation mode, the shut-off
valves may become very cold or very hot.
Risk of burning or frostbite!
Wear suitable protective equipment!
!
!
NOTICE
Do not overheat the shut-off valves!
Cool the valve body and the brazing adapter
during and after the brazing operation.
Maximum brazing temperature 700°C!
For welding, dismount the pipe connections and
the bushes.
When turning or mounting shut-off valves:
!
!
NOTICE
Risk of damage to the compressor.
Tighten screws crosswise in at least 2 steps to
the prescribed tightening torque.
Test tightness before commissioning!
When retrofitting the ECO shut-off valve:
Information
To increase the corrosion protection, it is recom-
mended to coat the surface of the ECO shut-off
valve.
4.3.3 Pipelines
Use only pipelines and system components which are
• clean and dry inside (free from slag, swarf, rust and
phosphate coatings) and
• which are delivered with an air-tight seal.
Depending on the compressor versions, they are sup-
plied with blanking plates on the pipe connections or
shut-off valves. These must be removed before per-
forming the strength pressure and tightness tests and
commissioning the system.
Information
The blanking plates are only designed to serve
as a transport protection. They are not suitable
as a separation between different system sec-
tions during the strength pressure test.
!
!
NOTICE
For systems with rather long pipelines or for
brazing operations without protective gas:
Install the suction-side cleaning filter (mesh size
< 25 μm).
!
!
NOTICE
Risk of compressor damage!
Generously sized filter dryers should be used to
ensure a high degree of dehydration and to
maintain the chemical stability of the circuit.
Make sure to choose a suitable quality (molecu-
lar sieves with specially adapted pore sizes).
Information
Notice for mounting the suction-side cleaning fil-
ter, see manual SH-170.
SB-170-9
11
4.3 Connecting the pipelines
WARNING
The compressor is under pressure!
Serious injuries are possible.
Depressurize the compressor!
Wear safety goggles!
!
!
NOTICE
Potential chemical reactions due to air penetra-
tion!
Proceed swiftly and keep shut-off valves closed
until evacuation.
4.3.1 Pipe connections
The pipe connections are suitable for pipes in all com-
mon dimensions in millimetres and inches. Brazed con-
nections have stepped diameters. The pipe will im-
merge more or less depending on its dimensions. If ne-
cessary, the bushing may even be cut at the end with
the largest diameter.
4.3.2 Shut-off valves
CAUTION
Depending on the operation mode, the shut-off
valves may become very cold or very hot.
Risk of burning or frostbite!
Wear suitable protective equipment!
!
!
NOTICE
Do not overheat the shut-off valves!
Cool the valve body and the brazing adapter
during and after the brazing operation.
Maximum brazing temperature 700°C!
For welding, dismount the pipe connections and
the bushes.
When turning or mounting shut-off valves:
!
!
NOTICE
Risk of damage to the compressor.
Tighten screws crosswise in at least 2 steps to
the prescribed tightening torque.
Test tightness before commissioning!
When retrofitting the ECO shut-off valve:
Information
To increase the corrosion protection, it is recom-
mended to coat the surface of the ECO shut-off
valve.
4.3.3 Pipelines
Use only pipelines and system components which are
• clean and dry inside (free from slag, swarf, rust and
phosphate coatings) and
• which are delivered with an air-tight seal.
Depending on the compressor versions, they are sup-
plied with blanking plates on the pipe connections or
shut-off valves. These must be removed before per-
forming the strength pressure and tightness tests and
commissioning the system.
Information
The blanking plates are only designed to serve
as a transport protection. They are not suitable
as a separation between different system sec-
tions during the strength pressure test.
!
!
NOTICE
For systems with rather long pipelines or for
brazing operations without protective gas:
Install the suction-side cleaning filter (mesh size
< 25 μm).
!
!
NOTICE
Risk of compressor damage!
Generously sized filter dryers should be used to
ensure a high degree of dehydration and to
maintain the chemical stability of the circuit.
Make sure to choose a suitable quality (molecu-
lar sieves with specially adapted pore sizes).
Information
Notice for mounting the suction-side cleaning fil-
ter, see manual SH-170.