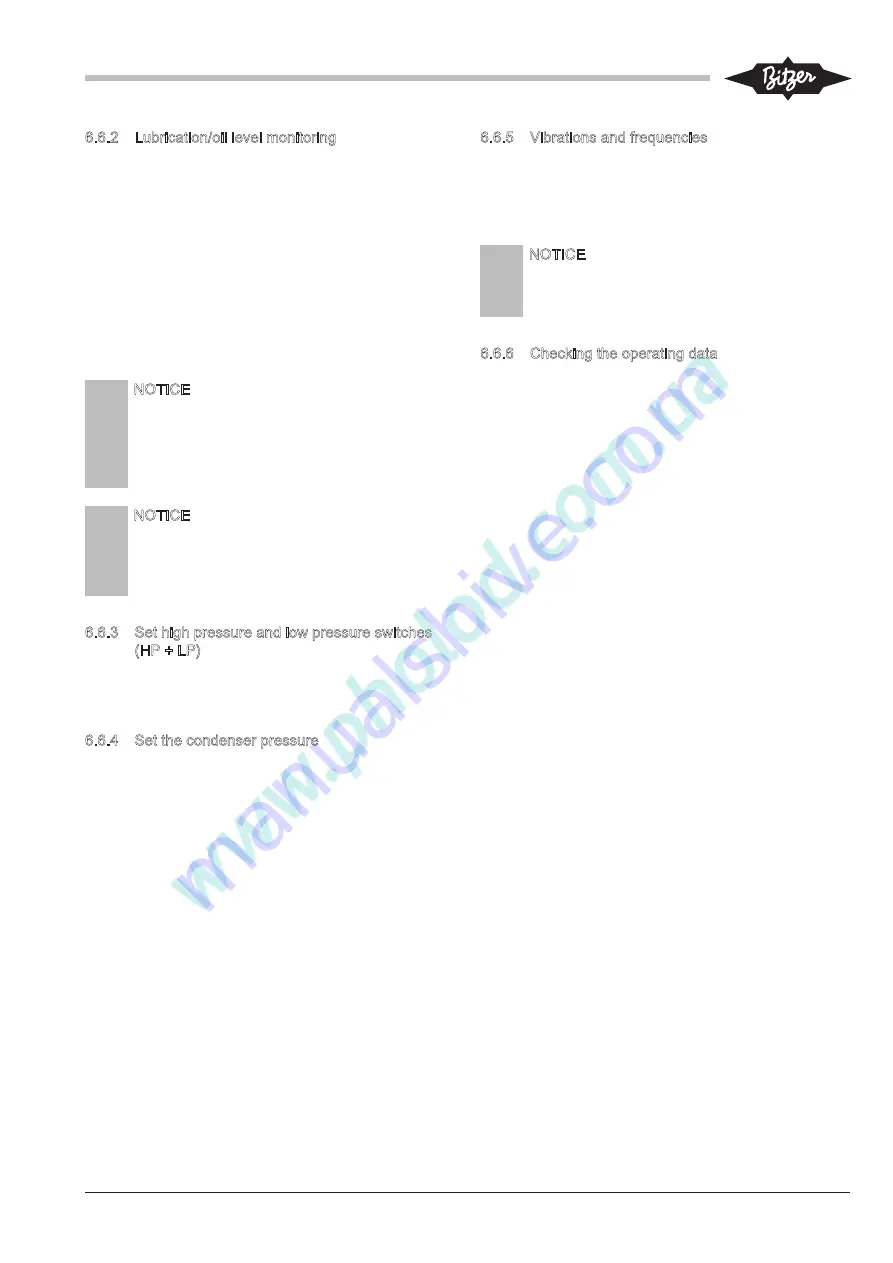
SB-170-9 RUS
29
SB-170-9
25
5.4.2 CM-SW-01
Standard for all CSW105 compressors
The compressor module integrates the entire electronic
periphery of the compressor: It allows monitoring the
essential operating parameters of the compressor: mo-
tor and discharge gas temperature, phase and rotation
direction monitoring, oil supply and application limits
and thus protects the compressor from operation under
critical conditions. For further information, see Tech-
nical Information ST-150.
!
!
NOTICE
The compressor module may be damaged or
fail!
Never apply any voltage to the terminals of CN7
to CN12 – not even for test purposes!
The voltage applied to the terminals of CN13
must not exceed 10 V!
The voltage applied to terminal 3 of CN14 must
not exceed 24 V! Do no apply voltage to the
other terminals!
The following components are completely installed and
wired in the state of delivery:
• Slider position indicator.
• Oil monitoring (OLC-D1).
• Solenoid valves for capacity control and V
i
.
• Discharge gas temperature sensor.
• Low pressure and high pressure transmitter.
Modification to these components or their wiring is not
required and should not be done without consulting
BITZER.
The following components are not installed and wired in
the state of delivery and need to be connected:
• Motor temperature monitoring (PTC sensor in motor
winding).
• Phase monitoring (in case of a phase failure or inad-
missibly high phase asymmetry).
The compressor module internally supplies voltage to
the peripheral devices (solenoid valves, oil monitoring
device and slider position indicator) and to the terminal
strips CN7 to CN12.
Please refer to the Technical Information ST-150 for in-
formation on all connections.
5.4.3 SE-i1
This protection device with extended monitoring func-
tions can be used as an option for all HS.53 .. HS.85
compressors and CSH and CSW compressors.
Monitoring functions:
• Temperature monitoring.
• Monitoring of the PTC control circuit to detect any
short-circuit or line break/sensor failure.
• Rotation direction monitoring.
• Monitoring of phase failure and asymmetry.
• Monitoring of the maximum cycling rate.
For further information, see Technical Information
CT-110.
5.4.4 SE-E2
Optional protection device for operation with frequency
inverter and soft starter (for a ramp time shorter than
1 s).
• Dimensions and integration in the control identical to
SE-E1.
• Suitable for all CS. compressors.
• Monitoring functions are basically identical to those
of SE-E1. However, the SE-E2 monitors phase fail-
ure during the entire running time of the compressor.
For further information, see Technical Information
ST-122.
5.4.5 Monitoring of the oil circuit
• For short circuits without liquid injection (LI) for addi-
tional cooling and for small system volume and small
refrigerant charge: Indirect monitoring with oil tem-
perature sensor (standard)
!
!
NOTICE
Lack of oil leads to a too high increase in tem-
perature.
Risk of damage to the compressor!
• For circuits with liquid injection (LI) for additional
cooling and / or for great system volume as well as
parallel compounding: Monitor oil level directly with
opto-electronic oil level monitoring (option), see
chapter Opto-electronic oil level monitoring OLC-D1-
S, page 26. The connection is on the compressor
housing, see chapter Connections and dimensional
drawings, page 14, position 8.
SB-170-9
29
6.6.2 Lubrication/oil level monitoring
• Check the lubrication of the compressor directly after
the compressor start.
The oil level must be visible in the zone of both sight
glasses.
• Check the oil level repeatedly within the first hours of
operation!
During the start phase, oil foam may arise but its level
should decrease at stable operating conditions. Other-
wise high proportions of liquid in the suction gas are
suspected.
!
!
NOTICE
Risk of wet operation!
Maintain the discharge gas temperature well
above the condensing temperature: at least
20 K.
At least 30 K for R407A, R407F and R22.
!
!
NOTICE
Risk of compressor failure due to liquid slug-
ging!
Before adding larger quantities of oil: check the
oil return!
6.6.3 Set high pressure and low pressure switches
(HP + LP)
Check exactly the cut-in and cut-out pressure values
according to the operating limits by testing them.
6.6.4 Set the condenser pressure
• Set the condenser pressure so that the minimum
pressure difference is reached within 20 s after the
compressor start.
• Avoid quick pressure reduction with finely stepped
pressure control.
Application limits, see BITZER SOFTWARE, manual
SH-170 and brochure SP-171 (CSH) / SP-172 (CSW).
6.6.5 Vibrations and frequencies
Check the system carefully to detect any abnormal vi-
bration, check particularly pipelines and capillary tubes.
In case of strong vibrations, take mechanical meas-
ures: e.g. use pipe clamps or install vibration dampers.
!
!
NOTICE
Risk of burst pipes and leakages on the com-
pressor and system components!
Avoid strong vibrations!
6.6.6 Checking the operating data
• Evaporation temperature
• Suction gas temperature
• Condensing temperature
• Discharge gas temperature
– min. 20 K above condensing temperature
– min. 30 K above condensing temperature for
R407C, R407F and R22
– max. 120°C on the outside of the discharge gas
line
• Oil temperature directly under the oil sight glass
• Cycling rate
• Current values
• Voltage
• Prepare data protocol.
Application limits, see BITZER SOFTWARE, manual
SH-170 and brochure SP-171 (CSH) / SP-172 (CSW).