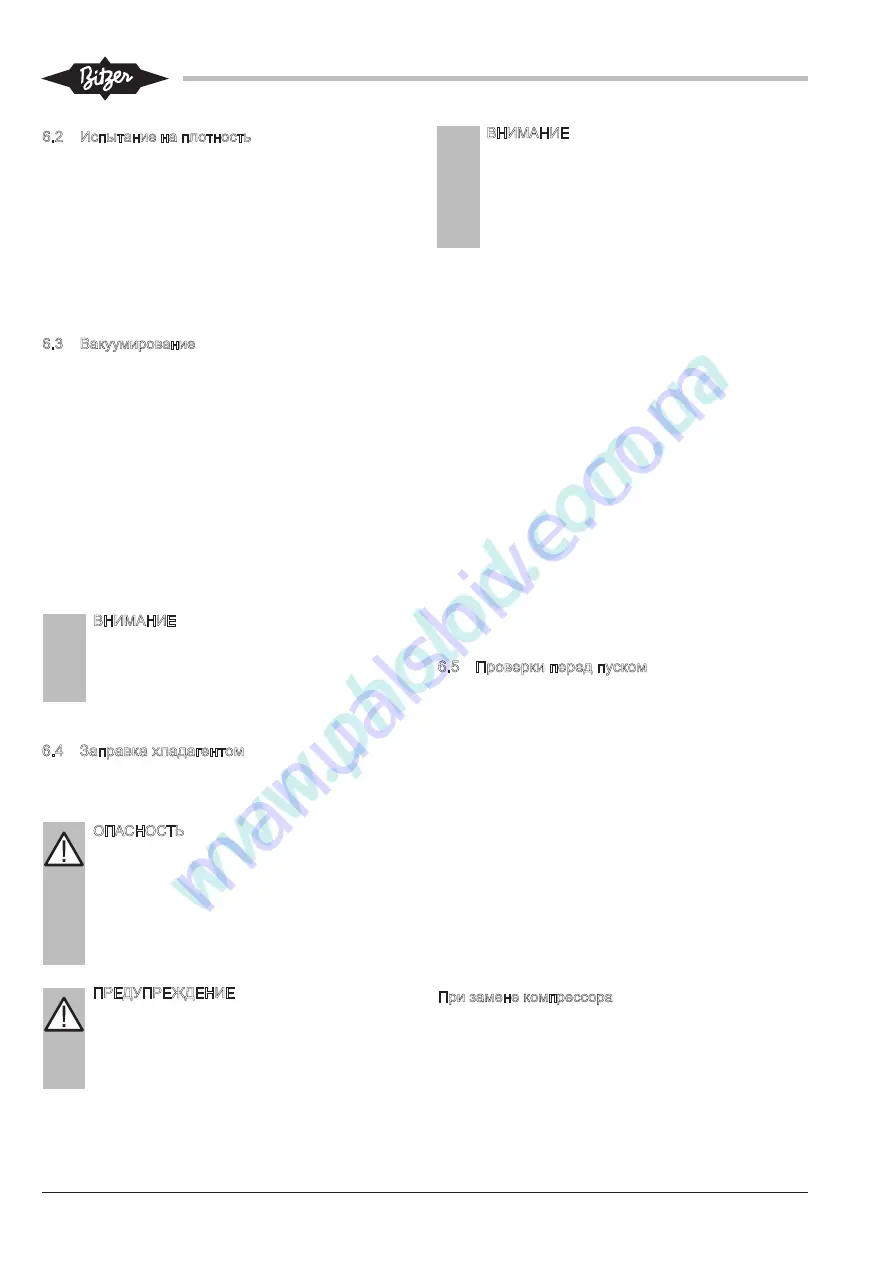
SB-170-9 RUS
94
SB-170-9
90
5.1 Raccordements réseau
Lors du dimensionnement des contacteurs du moteur,
des conduites d'amenée et des fusibles :
• Prendre en considération le courant de service maxi-
mal ou la puissance absorbée maximale du moteur.
• Choisir des contacteurs de la catégorie d'utilisation
AC3.
• Régler le relais thermique sur le courant de service
maximal du compresseur.
5.2 Versions moteur
!
!
AVIS
Risque de défaillance de compresseur !
N'utiliser le compresseur que dans le sens de
rotation prescrit !
Les séries de compresseurs CS.65, CS.75, CS.85,
CSH76 et CSH86 sont équipées de série de moteurs à
bobinage partiel (Part Winding, « PW ») avec
connexion Δ/ΔΔ. En option, elles peuvent également
être équipées de moteurs à étoile/triangle (Y/Δ). Pour
des informations détaillées, se reporter au manuel
SH-170.
Les modèles CS.95, CSH96 et CSW105 sont générale-
ment équipés de moteurs à étoile/triangle (Y/Δ).
Moteurs à bobinage partiel (PW)
Méthodes de démarrage :
• Démarrage à bobinage partiel pour réduire le cou-
rant de démarrage.
• Démarrage direct.
Retard de temps avant l’allumage du 2ème bobinage
partiel : 0,5 s max. !
Effectuer correctement les raccordements ! Une erreur
d’arrangement des raccords électriques aboutit à des
champs tournants contraires ou à l’angle de phase dé-
calé, et donc à un blocage du moteur !
Raccorder les bornes du moteur au couvercle de la
boîte de raccordement conformément aux instructions.
Tenir compte absolument de l’ordre des bobinages par-
tiels !
• 1er bobinage partiel (contacteur K1) : Raccords 1 /
2 / 3.
• 2ème bobinage partiel (contacteur K2) : Raccords 7 /
8 / 9.
• Partage de bobinage 50%/50%.
• Répartition des contacteurs moteur :
– 1er contacteur (PW 1) : 60% du courant de ser-
vice max.
– 2ème contacteur (PW 2) : 60% du courant de ser-
vice max.
Moteur à étoile-triangle
Le retard de temps entre la mise en route du compres-
seur d’un côté et, de l’autre, la commutation entre
l’opération en étoile et celle en triangle ne doit pas dé-
passer les 2 s.
Effectuer correctement les raccordements !
Toute erreur d’arrangement des raccords électriques
aboutit à un court-circuit !
Information
Les contacteurs réseau et triangles doivent être
calculés à au moins 60% du courant de service
max., le contacteur étoile à 33%.
5.3 Essai de haute tension (test de résistance
d'isolation)
Les compresseurs ont déjà été soumis avant leur sortie
d’usine à un essai de haute tension conformément à la
norme EN12693 ou conformément aux normes UL984
ou UL60335-2-34 pour la version UL.
!
!
AVIS
Risque d'endommagement de l'isolant et de dé-
faillance du moteur !
Il ne faut surtout pas répéter l'essai de haute
tension de la même manière !
Un nouvel essai de haute tension ne doit être réalisé
qu’à une tension alternative max. de 1000 V CA.
SB-170-9
94
6.2 Contrôler l'étanchéité
Contrôler l'étanchéité du circuit frigorifique (groupe as-
semblé) ainsi que de ses parties individuelles selon la
norme EN378-2 ou toute autre norme de sécurité équi-
valente également valable. Pour ce faire, créer de pré-
férence une surpression à l'aide de nitrogène déshy-
draté.
Tenir compte des pressions d'essai et des indications
de sécurité, voir chapitre Contrôler la résistance à la
pression, page 93.
6.3 Mettre sous vide
• Mettre en marche le réchauffeur d'huile.
• Ouvrir les vannes d'arrêt et les vannes magnétiques
présentes.
• Mettre sous vide l'ensemble de l'installation, y com-
pris le compresseur du côté d'aspiration et du côté
haute pression, à l'aide d'une pompe à vide.
Pour une puissance de pompe bloquée, le « vide
stable » atteint doit être inférieur à 1,5 mbar.
• Si nécessaire, répéter le processus à plusieurs re-
prises.
!
!
AVIS
Risque de défaut du moteur et du compres-
seur !
Ne pas démarrer le compresseur à vide !
Ne pas mettre de tension, même pour le
contrôle !
6.4 Remplir de fluide frigorigène
N'utiliser que des fluides frigorigènes homologués, se
reporter à voir chapitre Champs d’application, page 71.
DANGER
Danger d'éclatement des composants et tuyaux
dû à une surpression hydraulique pendant le
remplissage en phase liquide.
Risque de blessures graves.
Éviter absolument une suralimentation de l'ins-
tallation avec le fluide frigorigène !
AVERTISSEMENT
L'utilisation de fluides frigorigènes non
conformes est susceptible de faire éclater le
compresseur !
Risque de blessures graves !
N'utiliser que les fluides frigorigènes vendus par
des constructeurs renommés et des partenaires
commerciaux sérieux !
!
!
AVIS
Risque de fonctionnement en noyé pendant l'ali-
mentation en fluide !
Doser de façon extrêmement précise !
Maintenir la température du gaz de refoulement
à au moins 20 K au-dessus de celle de conden-
sation.
➙ Avant de remplir de fluide frigorigène :
➙ Ne pas mettre en marche le compresseur !
➙ Mettre en marche le réchauffeur d'huile.
➙ Contrôler le niveau d'huile dans le compresseur.
• Remplir directement le fluide frigorigène dans le
condenseur ou le réservoir ainsi que le cas échéant,
pour les installations avec évaporateur noyé, dans
l'évaporateur.
• Retirer le mélange du cylindre de remplissage en
tant que phase liquide et sans bulles.
• Après la mise en service, il se peut qu'un remplis-
sage complémentaire soit nécessaire : Lorsque le
compresseur est en marche, remplir le fluide frigori-
gène depuis le côté d'aspiration, dans l'idéal via l'en-
trée de l'évaporateur. Retirer le mélange du cylindre
de remplissage en tant que phase liquide et sans
bulles.
6.5 Contrôler avant le démarrage du compresseur
• Niveau d’huile (entre le centre du voyant inférieur et
la partie supérieure du voyant supérieur).
• Au démarrage du compresseur, la température
d’huile doit être d’au moins 20 °C et supérieure de
20 K à la température ambiante – soit environ (au
moins) 15 K au point de mesure juste en dessous du
voyant d’huile.
• Réglage et fonctionnement des dispositifs de protec-
tion et de sécurité.
• Valeurs de consigne du relais temporisé.
• Pression de coupure des limiteurs de haute et basse
pression.
• Vérifier si les vannes d’arrêt sont ouvertes.
En cas de remplacement du compresseur
Il y a déjà de l'huile dans le circuit. Il peut donc être né-
cessaire de vider une partie de la charge d'huile.
6.2 Испытание на плотность
Произведите испытание на плотность смонтированного
холодильного контура в целом или по частям в
соответствии с EN 378-2 (или другим действующим
стандартом безопасности). Для этого предпочтительно
использовать сухой азот.
Соблюдайте значения пробных давлений и указания
по технике безопасности, смотрите главу Испытание
давлением на прочность, стр. 93.
6.3 Вакуумирование
• Включите подогреватель масла.
• Откройте имеющиеся запорные и электромагнитные
клапаны.
• Произведите вакуумирование всей установки,
включая компрессор, подсоединив вакуум-насос к
стороне высокого и низкого давления.
При выключенном вакуумном насосе „устойчивый
вакуум“ должен удерживаться на уровне менее 1.5
mbar.
• При необходимости повторите эту процедуру
несколько раз.
ВНИМАНИЕ
Опасность повреждения мотора и компрессора!
Не запускайте компрессор под вакуумом!
Не подключать напряжение, в том числе и для
целей проверки!
SB-170-9
27
6.1 Checking pressure strength
Check the refrigerant circuit (assembly) according to
EN378-2 (or other applicable equivalent safety stand-
ards). The compressor had been already tested in the
factory for strength pressure. A tightness test is there-
fore sufficient, see chapter Checking tightness, page
27. If you still wish to perform a strength pressure test
for the entire assembly:
DANGER
Risk of bursting due to excessive pressure!
The pressure applied during the test must never
exceed the maximum permitted values!
Test pressure: 1.1-fold of the maximum allow-
able pressure (see name plate). Make a distinc-
tion between the high-pressure and low-pres-
sure sides!
6.2 Checking tightness
Check the refrigerant circuit (assembly) for tightness,
as a whole or in parts, according to EN378-2 (or other
applicable equivalent safety standards). For this, create
an excess pressure, preferably using dried nitrogen.
Observe test pressures and safety reference, see
chapter Checking pressure strength, page 27.
6.3 Evacuation
• Switch on the oil heater.
• Open all shut-off valves and solenoid valves.
• Use a vacuum pump to evacuate the entire system,
including the compressor, on the suction side and
the high-pressure side.
With the vacuum pump shut off, a "standing vacuum"
lower than 1.5 mbar must be achieved.
• Repeat the operation several times if necessary.
!
!
NOTICE
Risk of damage to the motor and compressor!
Do not start the compressor while it is in a va-
cuum!
Do not apply any voltage, not even for testing!
6.4 Charging refrigerant
Use only permitted refrigerants, see see chapter Ap-
plication ranges, page 5.
DANGER
Risk of bursting of components and pipelines
due to hydraulic excess pressure while feeding
liquid.
Serious injuries are possible.
Avoid overcharging the system with refrigerant
under all circumstances!
WARNING
Risk of bursting due to counterfeit refrigerants!
Serious injuries are possible!
Purchase refrigerants only from reputable man-
ufacturers and reliable distributors!
!
!
NOTICE
Risk of wet operation during liquid feeding!
Measure out extremely precise quantities!
Maintain the discharge gas temperature at least
20 K above the condensing temperature.
➙ Before charging with refrigerant:
➙ Do not switch on the compressor!
➙ Switch on the oil heater.
➙ Check the oil level in the compressor.
• Fill liquid refrigerant directly into the condenser or re-
ceiver; on systems with flooded evaporator, maybe
directly into the evaporator.
• Blends must be taken out of the charging cylinder as
a solid liquid.
• After commissioning, it may be necessary to add re-
frigerant: While the compressor is running, charge
with refrigerant on the suction side, preferably at the
evaporator inlet. Blends must be taken out of the
charging cylinder as a solid liquid.
ВНИМАНИЕ
Опасность влажного хода при заправке жидким
хладагентом!
Заправку производите малыми дозами!
Температура газа на нагнетании должна быть
как минимум на 20 K выше температуры
конденсации.
→
Перед заправкой хладагентом:
→
Не включайте компрессор!
→
Включите подогреватель масла.
→
Проверьте уровень масла в компрессоре.
• Заправляйте жидкий хладагент непосредственно
в конденсатор или ресивер. Для систем с
затопленным испарителем, возможна также
заправка в испаритель.
• Смеси изымайте из заправочного цилиндра в виде
сплошной (без пузырьков) жидкости.
• После ввода в эксплуатацию может потребоваться
дополнительная заправка хладагентом: Во время
работы компрессора заправляйте хладагент со
стороны всасывания, лучше всего заправлять на
входе в испаритель. При этом смеси из заправочного
цилиндра должны быть взяты в виде сплошной (без
пузырьков) жидкости.
SB-170-9
27
6.1 Checking pressure strength
Check the refrigerant circuit (assembly) according to
EN378-2 (or other applicable equivalent safety stand-
ards). The compressor had been already tested in the
factory for strength pressure. A tightness test is there-
fore sufficient, see chapter Checking tightness, page
27. If you still wish to perform a strength pressure test
for the entire assembly:
DANGER
Risk of bursting due to excessive pressure!
The pressure applied during the test must never
exceed the maximum permitted values!
Test pressure: 1.1-fold of the maximum allow-
able pressure (see name plate). Make a distinc-
tion between the high-pressure and low-pres-
sure sides!
6.2 Checking tightness
Check the refrigerant circuit (assembly) for tightness,
as a whole or in parts, according to EN378-2 (or other
applicable equivalent safety standards). For this, create
an excess pressure, preferably using dried nitrogen.
Observe test pressures and safety reference, see
chapter Checking pressure strength, page 27.
6.3 Evacuation
• Switch on the oil heater.
• Open all shut-off valves and solenoid valves.
• Use a vacuum pump to evacuate the entire system,
including the compressor, on the suction side and
the high-pressure side.
With the vacuum pump shut off, a "standing vacuum"
lower than 1.5 mbar must be achieved.
• Repeat the operation several times if necessary.
!
!
NOTICE
Risk of damage to the motor and compressor!
Do not start the compressor while it is in a va-
cuum!
Do not apply any voltage, not even for testing!
6.4 Charging refrigerant
Use only permitted refrigerants, see see chapter Ap-
plication ranges, page 5.
DANGER
Risk of bursting of components and pipelines
due to hydraulic excess pressure while feeding
liquid.
Serious injuries are possible.
Avoid overcharging the system with refrigerant
under all circumstances!
WARNING
Risk of bursting due to counterfeit refrigerants!
Serious injuries are possible!
Purchase refrigerants only from reputable man-
ufacturers and reliable distributors!
!
!
NOTICE
Risk of wet operation during liquid feeding!
Measure out extremely precise quantities!
Maintain the discharge gas temperature at least
20 K above the condensing temperature.
➙ Before charging with refrigerant:
➙ Do not switch on the compressor!
➙ Switch on the oil heater.
➙ Check the oil level in the compressor.
• Fill liquid refrigerant directly into the condenser or re-
ceiver; on systems with flooded evaporator, maybe
directly into the evaporator.
• Blends must be taken out of the charging cylinder as
a solid liquid.
• After commissioning, it may be necessary to add re-
frigerant: While the compressor is running, charge
with refrigerant on the suction side, preferably at the
evaporator inlet. Blends must be taken out of the
charging cylinder as a solid liquid.
SB-170-9
27
6.1 Checking pressure strength
Check the refrigerant circuit (assembly) according to
EN378-2 (or other applicable equivalent safety stand-
ards). The compressor had been already tested in the
factory for strength pressure. A tightness test is there-
fore sufficient, see chapter Checking tightness, page
27. If you still wish to perform a strength pressure test
for the entire assembly:
DANGER
Risk of bursting due to excessive pressure!
The pressure applied during the test must never
exceed the maximum permitted values!
Test pressure: 1.1-fold of the maximum allow-
able pressure (see name plate). Make a distinc-
tion between the high-pressure and low-pres-
sure sides!
6.2 Checking tightness
Check the refrigerant circuit (assembly) for tightness,
as a whole or in parts, according to EN378-2 (or other
applicable equivalent safety standards). For this, create
an excess pressure, preferably using dried nitrogen.
Observe test pressures and safety reference, see
chapter Checking pressure strength, page 27.
6.3 Evacuation
• Switch on the oil heater.
• Open all shut-off valves and solenoid valves.
• Use a vacuum pump to evacuate the entire system,
including the compressor, on the suction side and
the high-pressure side.
With the vacuum pump shut off, a "standing vacuum"
lower than 1.5 mbar must be achieved.
• Repeat the operation several times if necessary.
!
!
NOTICE
Risk of damage to the motor and compressor!
Do not start the compressor while it is in a va-
cuum!
Do not apply any voltage, not even for testing!
6.4 Charging refrigerant
Use only permitted refrigerants, see see chapter Ap-
plication ranges, page 5.
DANGER
Risk of bursting of components and pipelines
due to hydraulic excess pressure while feeding
liquid.
Serious injuries are possible.
Avoid overcharging the system with refrigerant
under all circumstances!
WARNING
Risk of bursting due to counterfeit refrigerants!
Serious injuries are possible!
Purchase refrigerants only from reputable man-
ufacturers and reliable distributors!
!
!
NOTICE
Risk of wet operation during liquid feeding!
Measure out extremely precise quantities!
Maintain the discharge gas temperature at least
20 K above the condensing temperature.
➙ Before charging with refrigerant:
➙ Do not switch on the compressor!
➙ Switch on the oil heater.
➙ Check the oil level in the compressor.
• Fill liquid refrigerant directly into the condenser or re-
ceiver; on systems with flooded evaporator, maybe
directly into the evaporator.
• Blends must be taken out of the charging cylinder as
a solid liquid.
• After commissioning, it may be necessary to add re-
frigerant: While the compressor is running, charge
with refrigerant on the suction side, preferably at the
evaporator inlet. Blends must be taken out of the
charging cylinder as a solid liquid.
6.4 Заправка хладагентом
Заправляйте только разрешенные хладагенты, смотрите
главу Области применения, стр. 71.
ОПАСНОСТЬ
Опасность разрыва компонентов и
трубопроводов из-за избыточного
гидравлического давления при заправке жидким
хладагентом.
Возможны серьёзные повреждения.
Избыточная заправка хладагентом абсолютно
недопустима!
ПРЕДУПРЕЖДЕНИЕ
Опасность разрыва компрессора при
использовании поддельных хладагентов!
Возможны тяжёлые повреждения!
Заказывайте хладагенты только у известных
производителей и проверенных дистрибьюторов!
SB-170-9
27
6.1 Checking pressure strength
Check the refrigerant circuit (assembly) according to
EN378-2 (or other applicable equivalent safety stand-
ards). The compressor had been already tested in the
factory for strength pressure. A tightness test is there-
fore sufficient, see chapter Checking tightness, page
27. If you still wish to perform a strength pressure test
for the entire assembly:
DANGER
Risk of bursting due to excessive pressure!
The pressure applied during the test must never
exceed the maximum permitted values!
Test pressure: 1.1-fold of the maximum allow-
able pressure (see name plate). Make a distinc-
tion between the high-pressure and low-pres-
sure sides!
6.2 Checking tightness
Check the refrigerant circuit (assembly) for tightness,
as a whole or in parts, according to EN378-2 (or other
applicable equivalent safety standards). For this, create
an excess pressure, preferably using dried nitrogen.
Observe test pressures and safety reference, see
chapter Checking pressure strength, page 27.
6.3 Evacuation
• Switch on the oil heater.
• Open all shut-off valves and solenoid valves.
• Use a vacuum pump to evacuate the entire system,
including the compressor, on the suction side and
the high-pressure side.
With the vacuum pump shut off, a "standing vacuum"
lower than 1.5 mbar must be achieved.
• Repeat the operation several times if necessary.
!
!
NOTICE
Risk of damage to the motor and compressor!
Do not start the compressor while it is in a va-
cuum!
Do not apply any voltage, not even for testing!
6.4 Charging refrigerant
Use only permitted refrigerants, see see chapter Ap-
plication ranges, page 5.
DANGER
Risk of bursting of components and pipelines
due to hydraulic excess pressure while feeding
liquid.
Serious injuries are possible.
Avoid overcharging the system with refrigerant
under all circumstances!
WARNING
Risk of bursting due to counterfeit refrigerants!
Serious injuries are possible!
Purchase refrigerants only from reputable man-
ufacturers and reliable distributors!
!
!
NOTICE
Risk of wet operation during liquid feeding!
Measure out extremely precise quantities!
Maintain the discharge gas temperature at least
20 K above the condensing temperature.
➙ Before charging with refrigerant:
➙ Do not switch on the compressor!
➙ Switch on the oil heater.
➙ Check the oil level in the compressor.
• Fill liquid refrigerant directly into the condenser or re-
ceiver; on systems with flooded evaporator, maybe
directly into the evaporator.
• Blends must be taken out of the charging cylinder as
a solid liquid.
• After commissioning, it may be necessary to add re-
frigerant: While the compressor is running, charge
with refrigerant on the suction side, preferably at the
evaporator inlet. Blends must be taken out of the
charging cylinder as a solid liquid.
SB-170-9
27
6.1 Checking pressure strength
Check the refrigerant circuit (assembly) according to
EN378-2 (or other applicable equivalent safety stand-
ards). The compressor had been already tested in the
factory for strength pressure. A tightness test is there-
fore sufficient, see chapter Checking tightness, page
27. If you still wish to perform a strength pressure test
for the entire assembly:
DANGER
Risk of bursting due to excessive pressure!
The pressure applied during the test must never
exceed the maximum permitted values!
Test pressure: 1.1-fold of the maximum allow-
able pressure (see name plate). Make a distinc-
tion between the high-pressure and low-pres-
sure sides!
6.2 Checking tightness
Check the refrigerant circuit (assembly) for tightness,
as a whole or in parts, according to EN378-2 (or other
applicable equivalent safety standards). For this, create
an excess pressure, preferably using dried nitrogen.
Observe test pressures and safety reference, see
chapter Checking pressure strength, page 27.
6.3 Evacuation
• Switch on the oil heater.
• Open all shut-off valves and solenoid valves.
• Use a vacuum pump to evacuate the entire system,
including the compressor, on the suction side and
the high-pressure side.
With the vacuum pump shut off, a "standing vacuum"
lower than 1.5 mbar must be achieved.
• Repeat the operation several times if necessary.
!
!
NOTICE
Risk of damage to the motor and compressor!
Do not start the compressor while it is in a va-
cuum!
Do not apply any voltage, not even for testing!
6.4 Charging refrigerant
Use only permitted refrigerants, see see chapter Ap-
plication ranges, page 5.
DANGER
Risk of bursting of components and pipelines
due to hydraulic excess pressure while feeding
liquid.
Serious injuries are possible.
Avoid overcharging the system with refrigerant
under all circumstances!
WARNING
Risk of bursting due to counterfeit refrigerants!
Serious injuries are possible!
Purchase refrigerants only from reputable man-
ufacturers and reliable distributors!
!
!
NOTICE
Risk of wet operation during liquid feeding!
Measure out extremely precise quantities!
Maintain the discharge gas temperature at least
20 K above the condensing temperature.
➙ Before charging with refrigerant:
➙ Do not switch on the compressor!
➙ Switch on the oil heater.
➙ Check the oil level in the compressor.
• Fill liquid refrigerant directly into the condenser or re-
ceiver; on systems with flooded evaporator, maybe
directly into the evaporator.
• Blends must be taken out of the charging cylinder as
a solid liquid.
• After commissioning, it may be necessary to add re-
frigerant: While the compressor is running, charge
with refrigerant on the suction side, preferably at the
evaporator inlet. Blends must be taken out of the
charging cylinder as a solid liquid.
SB-170-9
27
6.1 Checking pressure strength
Check the refrigerant circuit (assembly) according to
EN378-2 (or other applicable equivalent safety stand-
ards). The compressor had been already tested in the
factory for strength pressure. A tightness test is there-
fore sufficient, see chapter Checking tightness, page
27. If you still wish to perform a strength pressure test
for the entire assembly:
DANGER
Risk of bursting due to excessive pressure!
The pressure applied during the test must never
exceed the maximum permitted values!
Test pressure: 1.1-fold of the maximum allow-
able pressure (see name plate). Make a distinc-
tion between the high-pressure and low-pres-
sure sides!
6.2 Checking tightness
Check the refrigerant circuit (assembly) for tightness,
as a whole or in parts, according to EN378-2 (or other
applicable equivalent safety standards). For this, create
an excess pressure, preferably using dried nitrogen.
Observe test pressures and safety reference, see
chapter Checking pressure strength, page 27.
6.3 Evacuation
• Switch on the oil heater.
• Open all shut-off valves and solenoid valves.
• Use a vacuum pump to evacuate the entire system,
including the compressor, on the suction side and
the high-pressure side.
With the vacuum pump shut off, a "standing vacuum"
lower than 1.5 mbar must be achieved.
• Repeat the operation several times if necessary.
!
!
NOTICE
Risk of damage to the motor and compressor!
Do not start the compressor while it is in a va-
cuum!
Do not apply any voltage, not even for testing!
6.4 Charging refrigerant
Use only permitted refrigerants, see see chapter Ap-
plication ranges, page 5.
DANGER
Risk of bursting of components and pipelines
due to hydraulic excess pressure while feeding
liquid.
Serious injuries are possible.
Avoid overcharging the system with refrigerant
under all circumstances!
WARNING
Risk of bursting due to counterfeit refrigerants!
Serious injuries are possible!
Purchase refrigerants only from reputable man-
ufacturers and reliable distributors!
!
!
NOTICE
Risk of wet operation during liquid feeding!
Measure out extremely precise quantities!
Maintain the discharge gas temperature at least
20 K above the condensing temperature.
➙ Before charging with refrigerant:
➙ Do not switch on the compressor!
➙ Switch on the oil heater.
➙ Check the oil level in the compressor.
• Fill liquid refrigerant directly into the condenser or re-
ceiver; on systems with flooded evaporator, maybe
directly into the evaporator.
• Blends must be taken out of the charging cylinder as
a solid liquid.
• After commissioning, it may be necessary to add re-
frigerant: While the compressor is running, charge
with refrigerant on the suction side, preferably at the
evaporator inlet. Blends must be taken out of the
charging cylinder as a solid liquid.
SB-170-9
27
6.1 Checking pressure strength
Check the refrigerant circuit (assembly) according to
EN378-2 (or other applicable equivalent safety stand-
ards). The compressor had been already tested in the
factory for strength pressure. A tightness test is there-
fore sufficient, see chapter Checking tightness, page
27. If you still wish to perform a strength pressure test
for the entire assembly:
DANGER
Risk of bursting due to excessive pressure!
The pressure applied during the test must never
exceed the maximum permitted values!
Test pressure: 1.1-fold of the maximum allow-
able pressure (see name plate). Make a distinc-
tion between the high-pressure and low-pres-
sure sides!
6.2 Checking tightness
Check the refrigerant circuit (assembly) for tightness,
as a whole or in parts, according to EN378-2 (or other
applicable equivalent safety standards). For this, create
an excess pressure, preferably using dried nitrogen.
Observe test pressures and safety reference, see
chapter Checking pressure strength, page 27.
6.3 Evacuation
• Switch on the oil heater.
• Open all shut-off valves and solenoid valves.
• Use a vacuum pump to evacuate the entire system,
including the compressor, on the suction side and
the high-pressure side.
With the vacuum pump shut off, a "standing vacuum"
lower than 1.5 mbar must be achieved.
• Repeat the operation several times if necessary.
!
!
NOTICE
Risk of damage to the motor and compressor!
Do not start the compressor while it is in a va-
cuum!
Do not apply any voltage, not even for testing!
6.4 Charging refrigerant
Use only permitted refrigerants, see see chapter Ap-
plication ranges, page 5.
DANGER
Risk of bursting of components and pipelines
due to hydraulic excess pressure while feeding
liquid.
Serious injuries are possible.
Avoid overcharging the system with refrigerant
under all circumstances!
WARNING
Risk of bursting due to counterfeit refrigerants!
Serious injuries are possible!
Purchase refrigerants only from reputable man-
ufacturers and reliable distributors!
!
!
NOTICE
Risk of wet operation during liquid feeding!
Measure out extremely precise quantities!
Maintain the discharge gas temperature at least
20 K above the condensing temperature.
➙ Before charging with refrigerant:
➙ Do not switch on the compressor!
➙ Switch on the oil heater.
➙ Check the oil level in the compressor.
• Fill liquid refrigerant directly into the condenser or re-
ceiver; on systems with flooded evaporator, maybe
directly into the evaporator.
• Blends must be taken out of the charging cylinder as
a solid liquid.
• After commissioning, it may be necessary to add re-
frigerant: While the compressor is running, charge
with refrigerant on the suction side, preferably at the
evaporator inlet. Blends must be taken out of the
charging cylinder as a solid liquid.
6.5 Проверки перед пуском
• Уровень масла (между серединой нижнего
смотрового стекла и верхней областью верхнего
смотрового стекла).
• При запуске компрессора температура масла
должна составлять не менее 20°C и превышать
температуру окружающей среды на 20 К –
примерно на 15 К (минимум) в точке измерения,
непосредственно под смотровым стеклом.
• Настройки и функционирование устройств защиты
и безопасности.
• Настройки реле временных задержек.
• Значения давлений отключения реле высокого и
низкого давления.
• Проверьте, открыты ли запорные клапаны.
При замене компрессора
В контуре уже имеется масло. Поэтому может
потребоваться слив части масла.