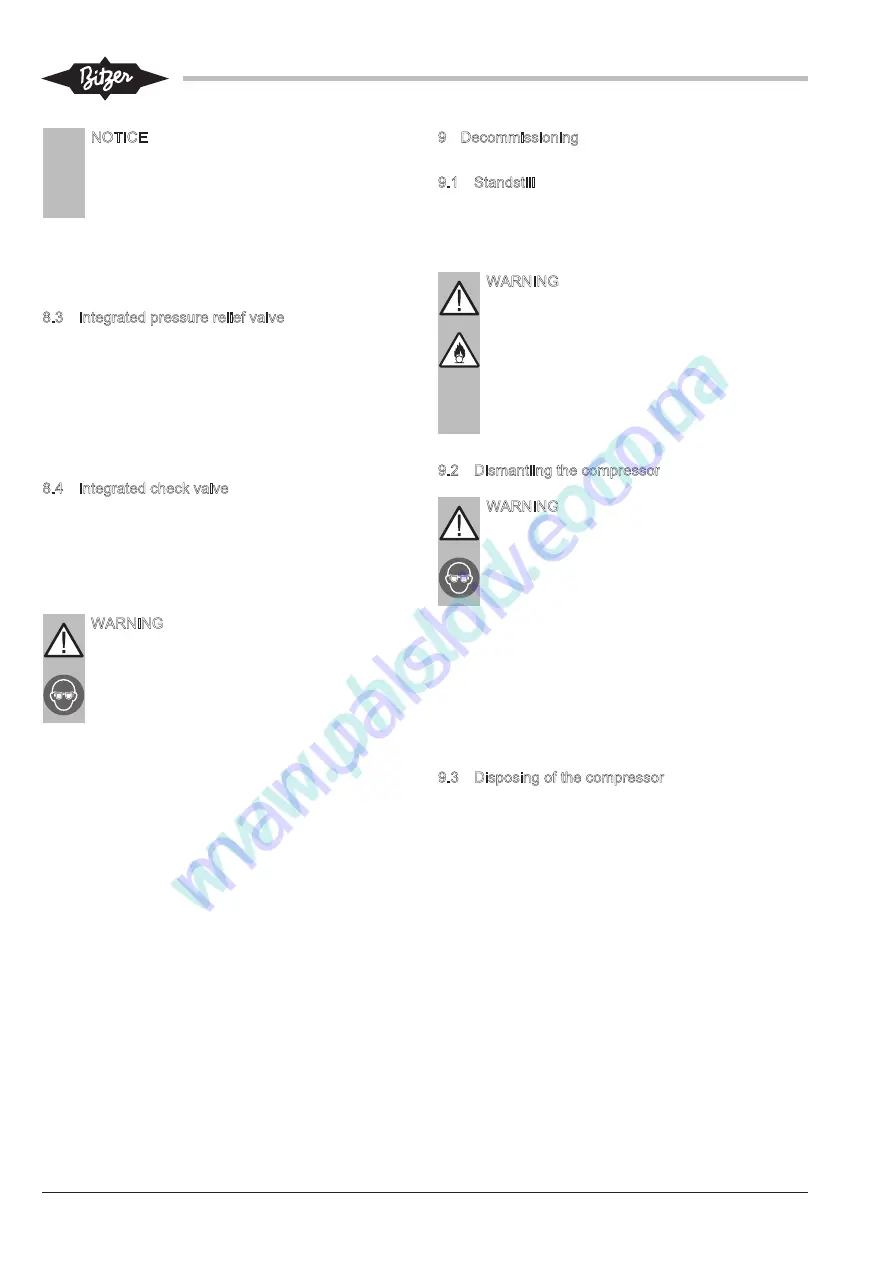
SB-170-9 RUS
32
SB-170-9
90
5.1 Raccordements réseau
Lors du dimensionnement des contacteurs du moteur,
des conduites d'amenée et des fusibles :
• Prendre en considération le courant de service maxi-
mal ou la puissance absorbée maximale du moteur.
• Choisir des contacteurs de la catégorie d'utilisation
AC3.
• Régler le relais thermique sur le courant de service
maximal du compresseur.
5.2 Versions moteur
!
!
AVIS
Risque de défaillance de compresseur !
N'utiliser le compresseur que dans le sens de
rotation prescrit !
Les séries de compresseurs CS.65, CS.75, CS.85,
CSH76 et CSH86 sont équipées de série de moteurs à
bobinage partiel (Part Winding, « PW ») avec
connexion Δ/ΔΔ. En option, elles peuvent également
être équipées de moteurs à étoile/triangle (Y/Δ). Pour
des informations détaillées, se reporter au manuel
SH-170.
Les modèles CS.95, CSH96 et CSW105 sont générale-
ment équipés de moteurs à étoile/triangle (Y/Δ).
Moteurs à bobinage partiel (PW)
Méthodes de démarrage :
• Démarrage à bobinage partiel pour réduire le cou-
rant de démarrage.
• Démarrage direct.
Retard de temps avant l’allumage du 2ème bobinage
partiel : 0,5 s max. !
Effectuer correctement les raccordements ! Une erreur
d’arrangement des raccords électriques aboutit à des
champs tournants contraires ou à l’angle de phase dé-
calé, et donc à un blocage du moteur !
Raccorder les bornes du moteur au couvercle de la
boîte de raccordement conformément aux instructions.
Tenir compte absolument de l’ordre des bobinages par-
tiels !
• 1er bobinage partiel (contacteur K1) : Raccords 1 /
2 / 3.
• 2ème bobinage partiel (contacteur K2) : Raccords 7 /
8 / 9.
• Partage de bobinage 50%/50%.
• Répartition des contacteurs moteur :
– 1er contacteur (PW 1) : 60% du courant de ser-
vice max.
– 2ème contacteur (PW 2) : 60% du courant de ser-
vice max.
Moteur à étoile-triangle
Le retard de temps entre la mise en route du compres-
seur d’un côté et, de l’autre, la commutation entre
l’opération en étoile et celle en triangle ne doit pas dé-
passer les 2 s.
Effectuer correctement les raccordements !
Toute erreur d’arrangement des raccords électriques
aboutit à un court-circuit !
Information
Les contacteurs réseau et triangles doivent être
calculés à au moins 60% du courant de service
max., le contacteur étoile à 33%.
5.3 Essai de haute tension (test de résistance
d'isolation)
Les compresseurs ont déjà été soumis avant leur sortie
d’usine à un essai de haute tension conformément à la
norme EN12693 ou conformément aux normes UL984
ou UL60335-2-34 pour la version UL.
!
!
AVIS
Risque d'endommagement de l'isolant et de dé-
faillance du moteur !
Il ne faut surtout pas répéter l'essai de haute
tension de la même manière !
Un nouvel essai de haute tension ne doit être réalisé
qu’à une tension alternative max. de 1000 V CA.
SB-170-9
32
!
!
NOTICE
Risk of damage to the compressor.
Tighten screws and nuts only to the prescribed
tightening torque and, if possible, crosswise in
at least 2 steps.
• Charge with new oil.
• Test tightness before commissioning.
8.3 Integrated pressure relief valve
The valve is maintenance-free. Its response pressure
difference is 28 bar.
However, after repeated venting, it may leak perman-
ently because of abnormal operating conditions. The
consequences are reduced performance and a higher
discharge gas temperature.
8.4 Integrated check valve
After being shut off, the compressor runs reverse for a
short time (approx. 5 s, until pressure compensation in
the oil separator takes place). When the check valve is
damaged or clogged, this time extends. The valve must
then be changed.
WARNING
The compressor is under pressure!
Serious injuries are possible.
Depressurize the compressor!
Wear safety goggles!
Mounting position: in discharge gas outlet flange below
the discharge shut-off valve or pipe connection. Re-
placement see maintenance instructions SW-170.
9 Decommissioning
9.1 Standstill
Leave the oil heater switched on until disassembly.
This prevents increased refrigerant concentration in the
oil.
WARNING
Risk of refrigerant evaporation from the oil.
Increased risk of flammability, depending on the
refrigerant!
Shut-down compressors or used oil may still
contain rather high amounts of dissolved refri-
gerant.
Close the shut-off valves on the compressor
and extract the refrigerant!
9.2 Dismantling the compressor
WARNING
The compressor is under pressure!
Serious injuries are possible.
Depressurize the compressor!
Wear safety goggles!
Close the shut-off valves on the compressor. Extract
the refrigerant. Do not deflate the refrigerant, but dis-
pose of it properly!
Loosen screwed joints or flanges on the compressor
valves. Remove the compressor from the system; use
hoisting equipment if necessary.
9.3 Disposing of the compressor
Drain the oil from the compressor. Dispose of waste oil
properly! Have the compressor repaired or dispose of it
properly!
When returning compressors that have been operated
with flammable refrigerant, mark the compressor with
the symbol "Caution flammable gas", as the oil may still
contain refrigerant.