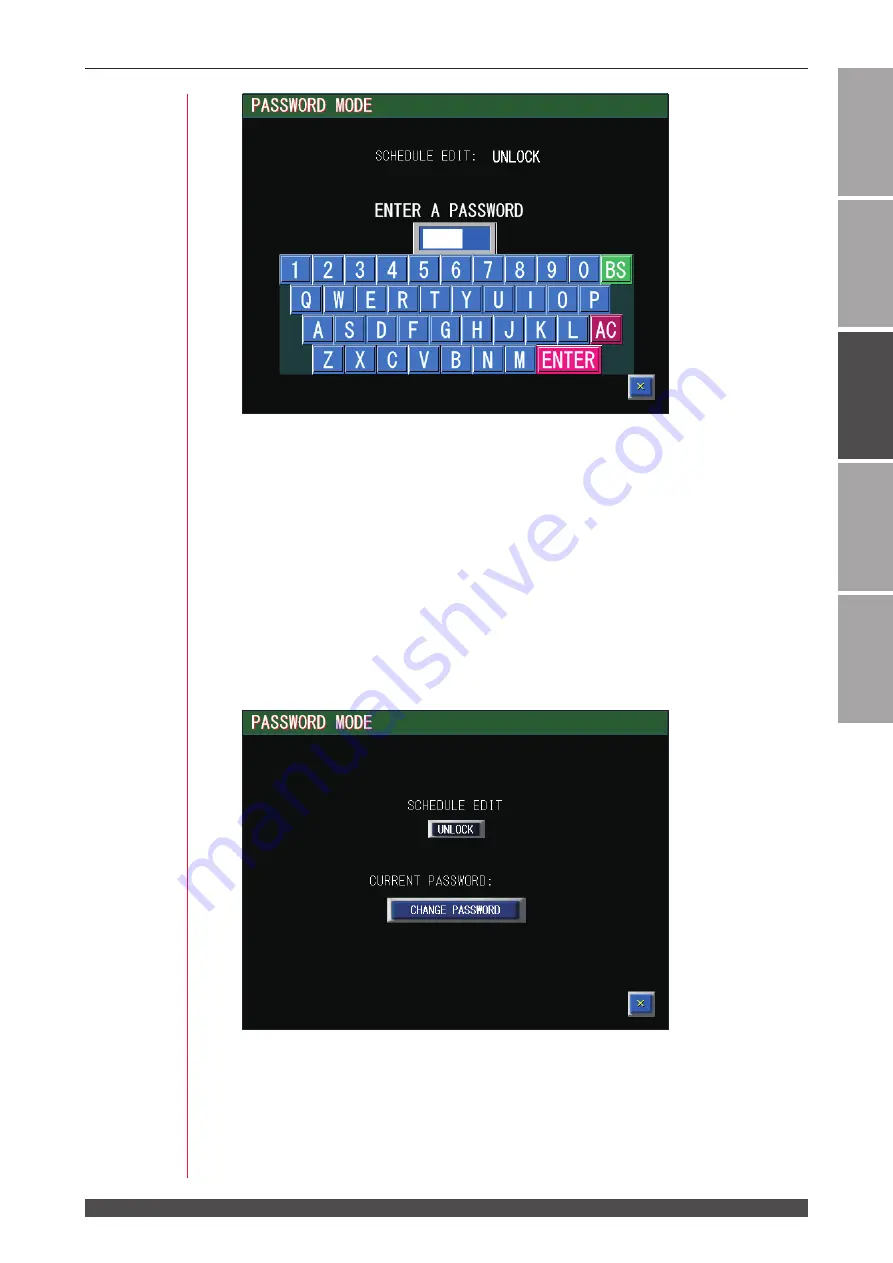
3 . Changing the Equipment Settings
95
MF-C2000A Series
Chapter 2 V
arious Settings
Introduction Part
Inst
allat
ion and
Preparation Part
Operating Part
Maintenance Part
Appendixes
(3) Enter the set password into the password input box.
Press the password by pressing keyboard keys on the screen. The AC key de-
letes all the entered characters. The BS key deletes a character in front of the
cursor one by one. The ENTER key is used to check the entered password for
correctness.
⇒
At delivery, a password is not set. Press the ENTER key without inputting charac-
ters. Then, set a password.
⇒
The password to be entered must consist of 4 alphanumerical characters.
(4) Press the ENTER key on the keyboard.
When the entered password is correct, the new password setting screen is dis-
played.
When the entered password is wrong, the WRONG PASSWORD screen is dis-
played.
Then, enter the set password once again.
Summary of Contents for MF-C2000A Series
Page 1: ...AA04OM1209213 07 FIBER LASER WELDER MF C2000A Series OPERATION MANUAL ...
Page 21: ...Introduction Part ...
Page 22: ......
Page 34: ......
Page 42: ......
Page 43: ...Installation and Preparation Part ...
Page 44: ......
Page 73: ...Operating Part ...
Page 74: ......
Page 78: ......
Page 142: ......
Page 212: ......
Page 213: ...Maintenance Part ...
Page 214: ......
Page 232: ......
Page 244: ......
Page 245: ...Appendixes ...
Page 246: ......