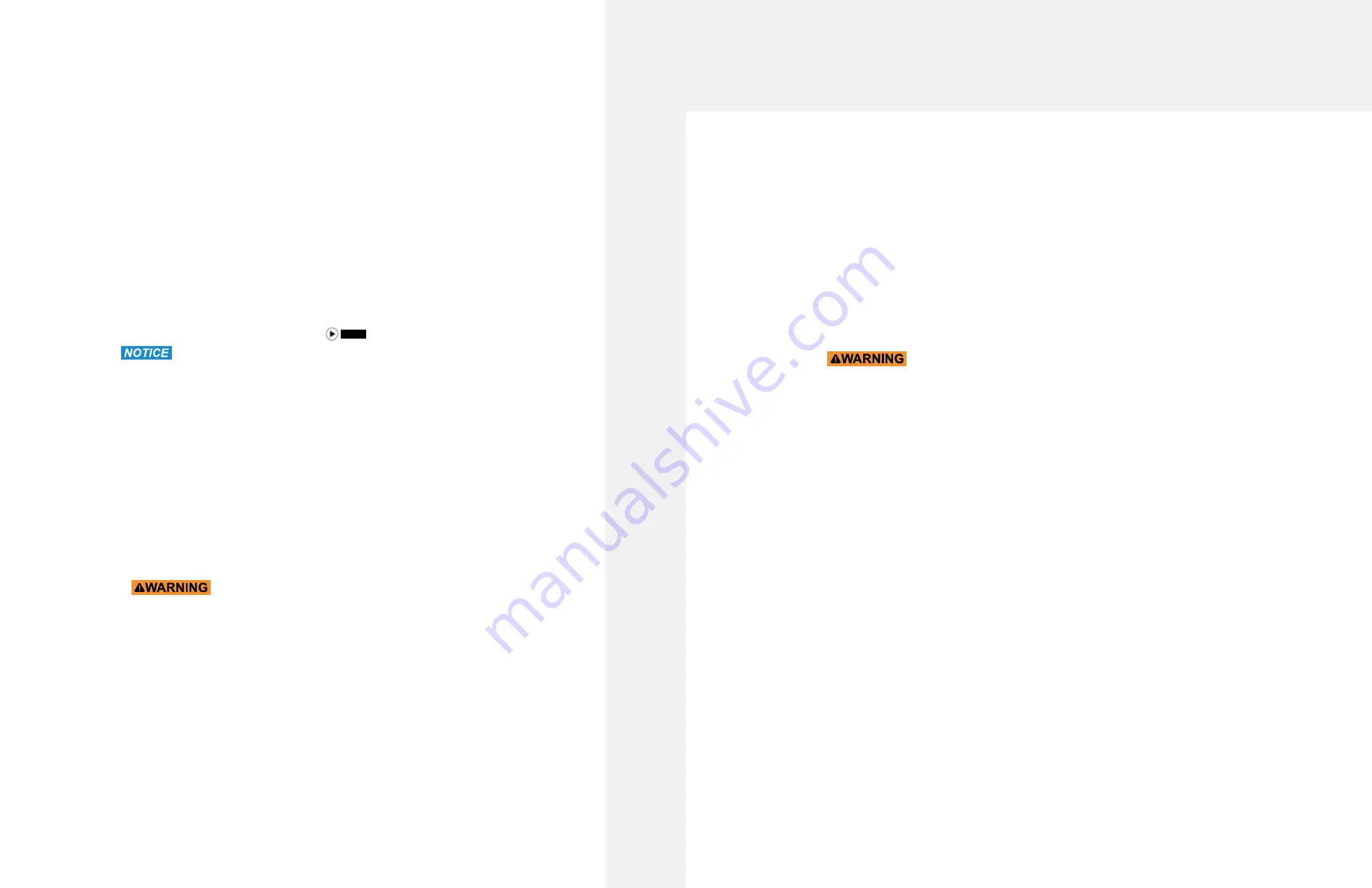
Next Time
Over time the abrasive rate of the machine will change to due to a variety of reasons, including but
not limited to wear, backflow events, or clogs. Often the earliest indication that the abrasive orifice
will need to be changed is that you exhibit partial cutting (rate too low) or your cut-time does
not correlate with the amount of abrasive you have used (rate too high). We also recommend
checking the abrasive rate after any clog or backflow, as either event can change the rate.
Practicing good cutting procedures will help prevent the abrasive orifice from getting clogged and
changing the abrasive rate. These include:
•
Avoid letting the cutting head touch the material by leveling your Cut Bed and setting your
nozzle height.
•
Avoid letting the abrasive hopper run out.
•
Pay attention to the amount of abrasive used in comparison to what WAM predicts the
usage to be
•
Always use your sifting Screens when adding abrasive.
•
Beyond that, normal wear and tear is a part of any machine tool and is to be expected.
Inspecting the High-Pressure O-Rings
The High-Pressure Hoses need to be checked for wear every 20 – 50 hours. If you do
not properly identify wear in the High-Pressure O-Rings, they can become damaged and lead to a
severe leak.
To check the High-Pressure O-Rings:
•
Follow the “Safety Instructions” on the “Hose Disconnect Procedure” label next to both sides of
the High-Pressure Hose connections. This includes:
•
Ensure the High-Pressure Hose is purged by selecting Setup & Maintenance > Maintenance
> Nozzle Purge on the Control Panel. Allow the Nozzle Purge cycle to finish.
•
Turn off WAZER.
•
Disconnect Pump Box and WAZER Power Cables.
•
Disconnect Pump Box Signal Line.
•
Turn off the water supply.
•
Unplug Water Inlet Hose.
•
Disconnect both sides of the High-Pressure Hose to completely disconnect
it by pulling back on the knurled collet of the Connector and pulling the hose out of the
Connection.
•
Look into the ends of the High-Pressure Hose Connector and check to see if the O-Ring is
frayed, worn, misaligned, or otherwise damaged and needs to be replaced. If one or both of
the High-Pressure O-Rings look damaged in any way, simply replace them with one of the spare
O-Rings we provide in the Spare Parts accessory bag. If you are out of spare O-Rings please
contact WAZER Customer Support for replacements.
To replace the High-Pressure O-Ring:
•
Use a pick or needle nose pliers to remove the damaged High-Pressure O-Ring from the High-
Pressure Hose Connector.
•
Push a fresh High-Pressure O-Ring into the Connector and use a pick or needle nose pliers to
push it into place. You should see it nest inside the Connector if installed correctly.
•
Reconnect the High-Pressure Hose to WAZER and Pump Box. If your O-Rings were damaged,
ensure that the High-Pressure Hose does not bend or turn aggressively.
Pump Box Oil Change
The Pump Box oil needs to be changed after the first 50 hours of use, and then every 300 hours
after that. These oil changes aren’t done because of the degradation of the oil, but because of the
impurities that will find their way into the oil over time. These impurities will result in premature
wear if allowed to stay in the oil for extensive periods of time (>300hours).
1. If you have recently been cutting with
WAZER, allow the Pump Box to cool for
approximately 30 minutes before service.
2. If WAZER has not recently been running,
turn WAZER on for 30 seconds (i.e. start
a Cut and cancel it, or run part of a Tank
Cleaning cycle). This will stir up the oil and
impurities so they can be removed when
you drain the oil.
3. Follow the “Safety
Instructions” on the “Cover Opening
Procedure” label near the back of the
cover.
This includes:
•
Turn off the water supply.
•
Turn off WAZER
•
Disconnect the Pump Box Power Cable.
•
Disconnect the Pump Box Signal Cable.
4. You can now move the Pump Box to a
convenient place to work (i.e. Workbench,
table or open floorspace). Remember that
this unit is heavy and requires two people
to lift or move. Also, the gray sheet metal
Pump Box Cover is NOT structural and
should not be used as a lift point.
5. Loosen (you DO NOT need to remove) the
four fasteners that hold the Pump Box
Cover on. You should be able to loosen
these with a 4mm allen key tool. Two are
located along the back edge and two on
the bottom front edge.
6. Remove the Pump Box Cover by pulling the
bottom front edge forward and lifting top
edge up.
7. The Oil Drain Plug is located at the bottom
of the crankcase. You will need to find a
container to collect the drained oil from
this location. Prop the Pump Box up so you
can slide the container under this plug.
8. Remove the Oil Drain Plug with a 17 mm
wrench. Wait for all the oil to drain.
9. Replace the oil drain plug and tighten until
snug. Wipe the area down of ALL excess
oil so that you can assess any leaks or drip
later.
10. Remove the yellow Pump Vent Cap.
11. Refill the oil with approximately 15 oz of a
SAE15W40 oil. The correct oil level is visible
in the crankcase window that is located
on the opposite side of the pulley. The
correct level is in the middle of the window,
between the high and low levels.
12. Replace the yellow Pump Vent Cap.
13. Wipe the Pump Box clean of any oil.
14. Replace the cover and tighten the Pump
Box Cover Knobs so the cover is securely
fastened. Ensure that these are well-
secured to prevent unwanted vibration
noises and the cover rattling loose during
operation.
15. Reconnect and set up the Pump Box:
a. You’ll need to reconnect the High-
Pressure Hose and Water Inlet Hose.
b. Because you made modifications to
water connections, perform a leak test
before making any electrical connections.
c. Connect the Signal Cable between
WAZER and Pump Box.
d. Reconnect the Pump Box Power Cable.
Maintenance & Machine Procedures
Medium Term Service
Interval: 300 hours (5000lbs/2200kg) of abraisve
VIDEO
Maint
enan
ce |
SE
C
TION 7
106
107