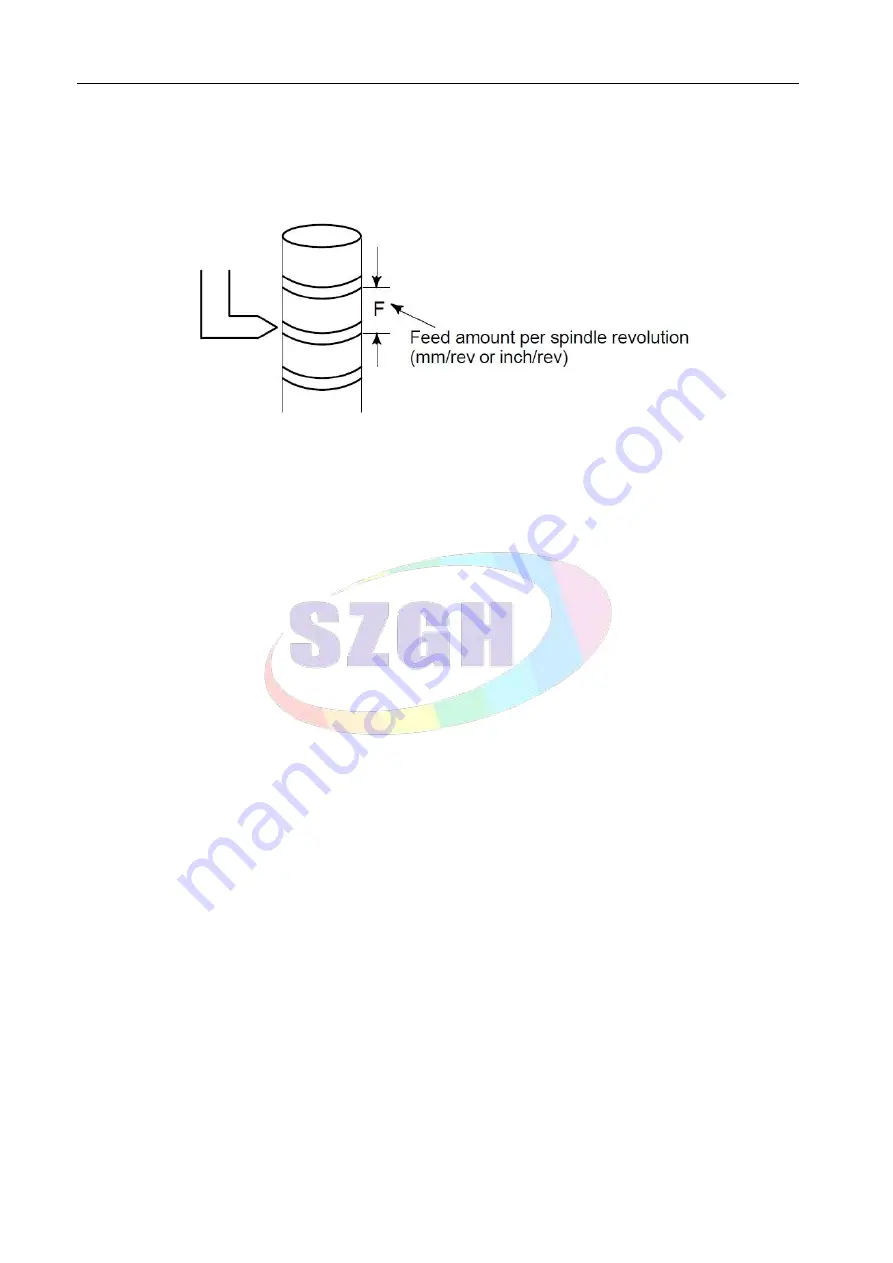
-Shenzhen Guanhong Automation Co.,Ltd.-
SZGH-CNC1000MDb Series
- 46 -
a modal code. Once a G95 is specified, it is valid until G94 (feed per minute) is specified.
An override from 0% to 150% can be applied to feed per minute with the switch on the
machine operator’s panel. For detailed information, see the appropriate manual of the machine tool
builder.
Fig3.15.3 Feed per revolution
Note: When the speed of spindle is low, feedrate fluctuation may occur. The slower the spindle rotates, the
more frequently feedrate fluctuation occurs.
3.20 Processing Mode (G60/G64)
According to process requirements, user can specify the connection way between program block
by G60/G64.
Format:
G60
; Accurate Positioning Processing
G64
; Continuous Path Processing
Both G60 and G64 are modal instructions.
Содержание SZGH-CNC1000MDb Series
Страница 220: ...Shenzhen Guanhong Automation Co Ltd SZGH CNC1000MDb Series 207 Appendix I Wiring Diagram of CN3 Plug...
Страница 221: ...Shenzhen Guanhong Automation Co Ltd SZGH CNC1000MDb Series 208 Appendix II Wiring Diagram of CN10 Plug...
Страница 222: ...Shenzhen Guanhong Automation Co Ltd SZGH CNC1000MDb Series 209 Appendix III Wiring Diagram of CN4 Plug...