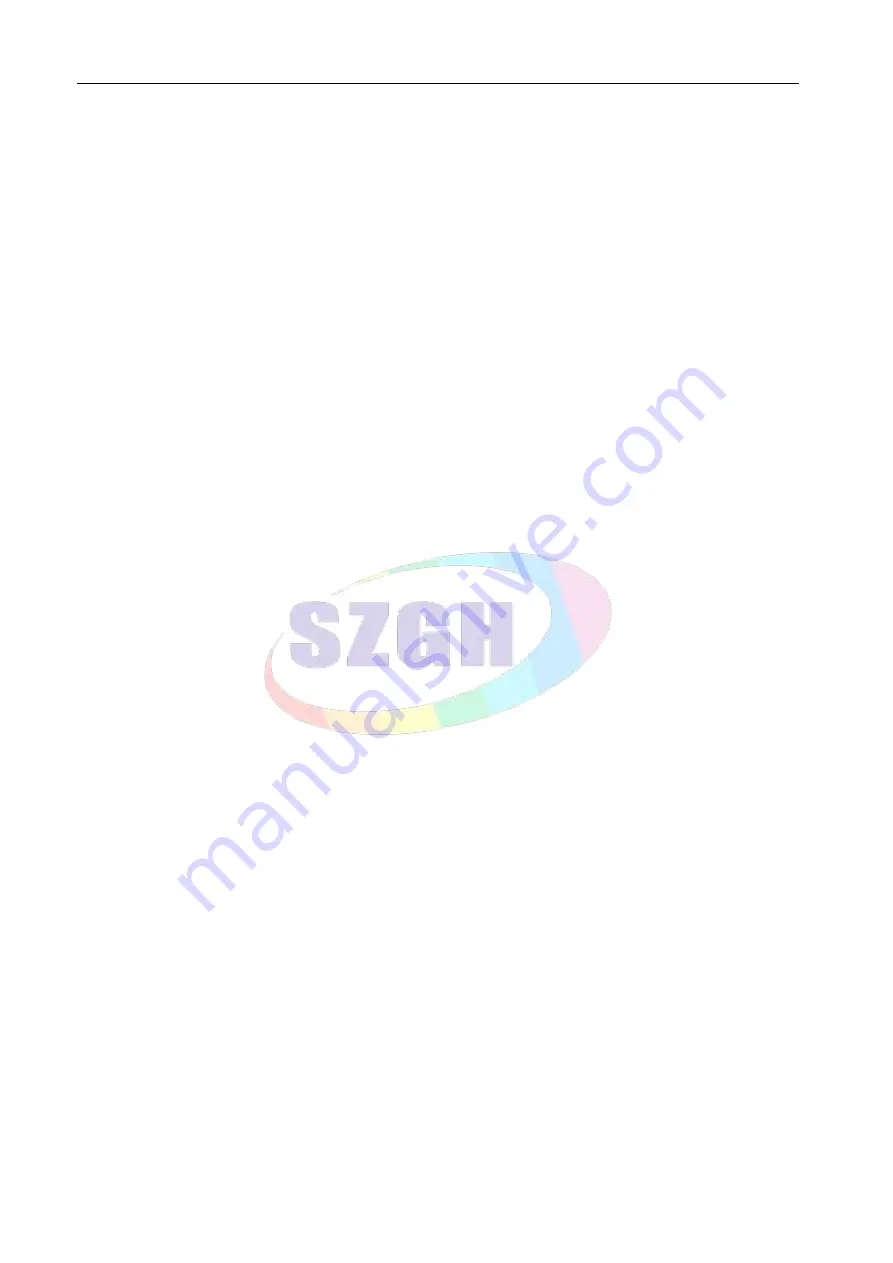
-Shenzhen Guanhong Automation Co.,Ltd.-
SZGH-CNC1000MDb Series
- 172 -
318,B_Machine Coordinate of float zero point
It is set the machine coordinate value of B-axis based on float zero point. The value is distance
between current position of machine tool & float zero point.
323,Nearest way for rotary axis(+4:X, +8:Y, +16:Z, +32:A, +64:B)
It sets whether these rotary axes are moving with nearest way, +4: X-axis don’t run with
nearest way, +8:Y-axis, +16:Z-axis, +32:A-axis, +64:B-axis.
404,SP_Direction when position control mode
It is the direction of spindle motor,o means reverse,1 mean normal.
405,Using Electronic Gear Ratio for Spindle [0:Yes, 1:No]
It is for whether the spindle use electron gear.
406,Numerator of SP_Electronic Gear Ratio in Low Gear (1-999999)
407,Denominator of SP_Electronic Gear Ratio in Low Gear (1-999999)
408,Numerator of SP_Electronic Gear Ratio in High Gear (1-999999)
409,Denominator of SP_Electronic Gear Ratio in High Gear (1-999999)
These are numerator & denominator of SP-axis’s electron low gear with different gear.
410,Coordinate Axis when spindle do tapping[91 X,92 Y/C,93 Z,94 A,95 B]
It is the axis that be use for spindle when interpolation tap.
411,Control Mode of Tapping [0:Following, 1: Interpolation]
[2 follow encode;3 interpolation to SP]
It is control mode of interpolation tap.
412,Teeth of SP_Motor (<P413)
It is tooth number of spindle.it <=P413.
413,Teeth of SP_Encoder (>P412)
It is tooth number of SP-encoder,it >=P412.
Attention:the tooth number of spindle must be not more than the tooth number of SP-encoder,when
less,it need to install our company’s adapter plate.
414,Follow-Up of AAxis[7:X, 8:Y, 9:Z]
It is set the function of follow up of A-axis.
Set to 7: A-axis follow up with X-axis; Set to 8: A-axis follow up with Y-axis ; Set to 9: A-axis
follow up with Z-axis. A-axis follow up on condition of both Manual & Auto.
Set to 17: C-axis follow up with X-axis; Set to 18: C-axis follow up with Y-axis ; Set to 19:
C-axis follow up with Z-axis. C-axis follow up on condition of both Manual & Auto.
Set to 27: B-axis follow up with X-axis; Set to 28: B-axis follow up with Y-axis ; Set to 29:
B-axis follow up with Z-axis. A-axis follow up on condition of both Manual & Auto.
Special Cautions:
1.Only when CNC controller is configured with related feeding axis, and there are related parameters sets
for related feeding axis, such as C axis & A-axis.
2.About bit parameters, if some bits are don’t specified functions for feeding axis, please keep same to
ex-factory set, which should be important for inner system, otherwise it will affect normal operations of CNC
system.
Содержание SZGH-CNC1000MDb Series
Страница 220: ...Shenzhen Guanhong Automation Co Ltd SZGH CNC1000MDb Series 207 Appendix I Wiring Diagram of CN3 Plug...
Страница 221: ...Shenzhen Guanhong Automation Co Ltd SZGH CNC1000MDb Series 208 Appendix II Wiring Diagram of CN10 Plug...
Страница 222: ...Shenzhen Guanhong Automation Co Ltd SZGH CNC1000MDb Series 209 Appendix III Wiring Diagram of CN4 Plug...