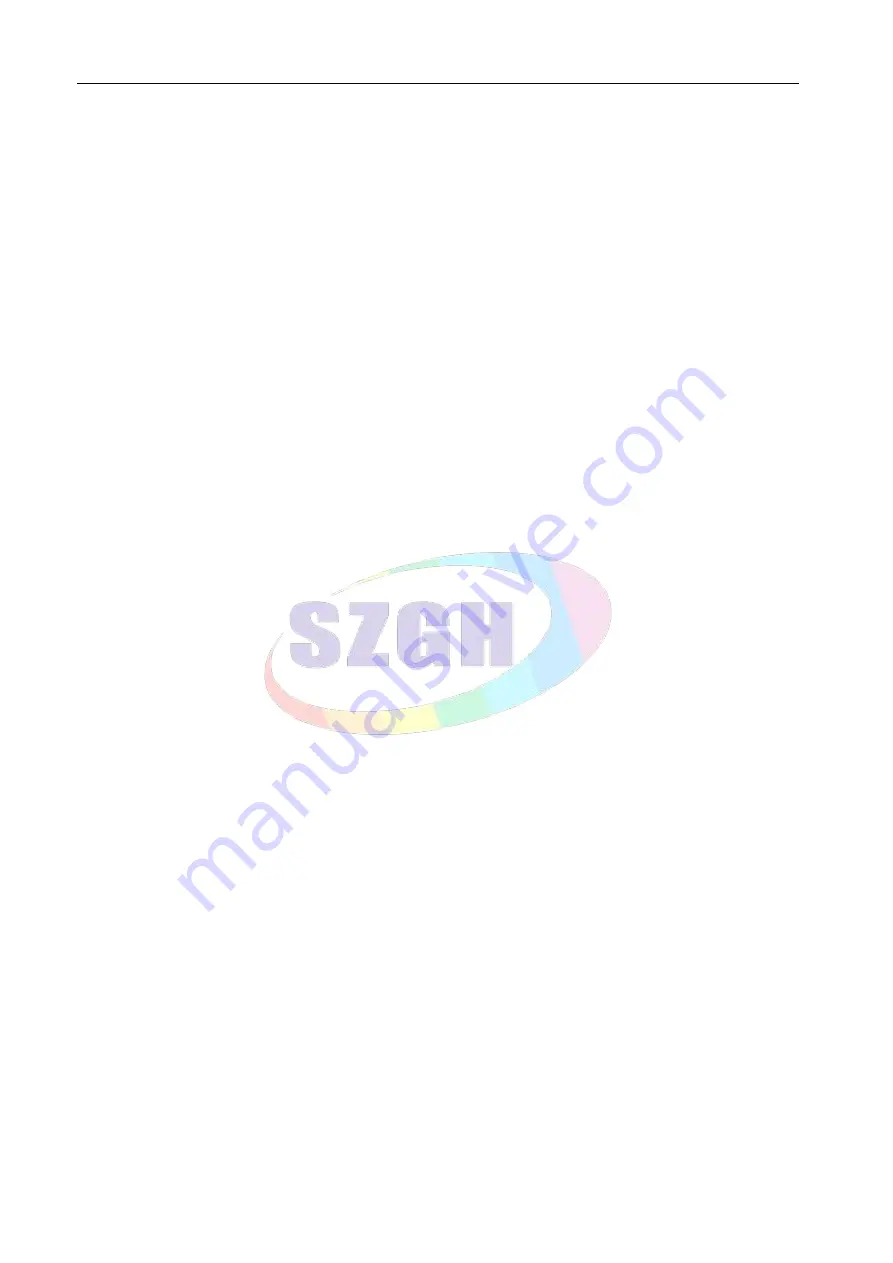
-Shenzhen Guanhong Automation Co.,Ltd.-
SZGH-CNC1000MDb Series
- 132 -
6.5.4 Manual Reference Position Return
The CNC machine tool has a position used to determine the machine position. This position is
called the reference position, where the tool is replaced or the coordinate are set. Ordinarily, after
the power is turned on or alarm/release emergency stop, the tool is moved to the reference position.
Manual reference position return is to move the tool to the reference position using switches
and push buttons located on the operator’s panel.
In axis parameter, P38 is set for the grade of homing; there are 4 grades for homing. 0: Just
hint; 1:No use; 8: Compulsion; 9: Super Compulsion;
Suggestion: In order to ensure processing accuracy, it needs homing after reboot.
There are two ways that return to reference position manually, one is that floating zero point,
the other is that switch for homing, details as follows:
(1) Floating Zero Point Set
When user don’t fix switches for Homing , user can use floating zero point as home, also
reference position, also original point of machine coordinate system.
Parameters set: In Axis parameter,
P33: Bit parameter, D3:X ; D4:Y ; D5:Z ; D6:A ; D7:B ; 1 means float zero point;
P34: Distance between reference position & current position in X direction;
P35: Distance between reference position & current position in Y direction;
P36: Distance between reference position & current position in Z direction;
P37: Distance between reference position & current position in A direction;
P318 in Axis parameter:Distance between reference position & current position in B direction;
Steps of setting floating zero point(home):
1. Enabled function of float zero point of all axes(XZCAB): P23= 11111001;
2. Moving each axes to designated position in order to set floating point easily.
3.Set distance between reference & designated position: P34/P35/P36/P37/P318
(2) Switch For Homing Set
User can fixed switches for homing,some parameters & wiring needs to done.
A. Parameters set:
in Axis Parameter
,
P33: Bit parameter, D3:X ; D4:Y ; D5:Z ; D6:A ; D7:B ; 0 means switch for homing;
P38: Grade of Homing,0: Just hint; 1:No use; 8: Compulsion; 9: Super Compulsion;
P39: Mode of Homing, 0 & 2: Detect Z0 signal; 1 & the others, no detect ;
P40: Bit Parameter, Direction & Sequence of Homing;
P41: Bit parameter, Type of switch for homing ;
P42: Range of detecting Z0 signal in X-axis ;
P43: Range of detecting Z0 signal in Y-axis ;
P44: Range of detecting Z0 signal in Z-axis ;
P45: Range of detecting Z0 signal in A-axis ;
P46: Offset after homing in X-axis
P47: Offset after homing in Y-axis
P48: Offset after homing in Z-axis
P49: Offset after homing in A-axis
In Speed Parameter,
P34: X-axis homing speed
Содержание SZGH-CNC1000MDb Series
Страница 220: ...Shenzhen Guanhong Automation Co Ltd SZGH CNC1000MDb Series 207 Appendix I Wiring Diagram of CN3 Plug...
Страница 221: ...Shenzhen Guanhong Automation Co Ltd SZGH CNC1000MDb Series 208 Appendix II Wiring Diagram of CN10 Plug...
Страница 222: ...Shenzhen Guanhong Automation Co Ltd SZGH CNC1000MDb Series 209 Appendix III Wiring Diagram of CN4 Plug...