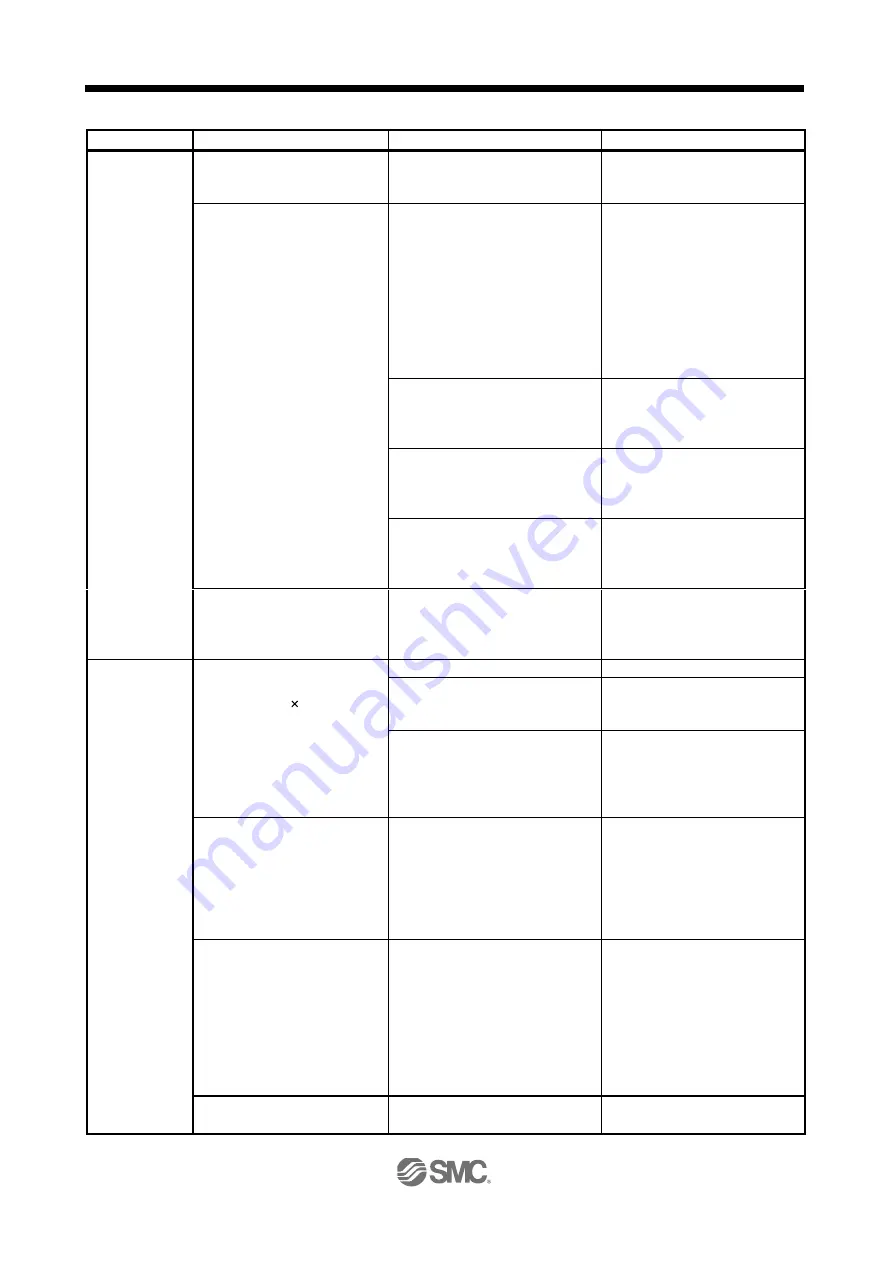
9 - 24
9. TROUBLESHOOTING
Phenomena
Checkpoint
Estimated cause
Action
The position is
misaligned in
operation after
the home position
return.
Check the servo alarm/warning.
1. A servo alarm is occurring.
2. The servo motor coasts due to a
servo alarm.
Check the details of the alarm and
remove its cause.
The output pulse counter and the
driver cumulative command pulses
of the driver do not match.
1. An output pulses miscounting due
to noises.
2. A shield of a command cable is
made incorrectly.
3. A command cable is connected
loosely or broken.
1. Check that the shield of the
command cable is made
correctly.
2. When wiring with the open
collector system, change it to the
differential system.
3. Wire apart from the strong
electric circuit.
4. Install the data line filters.
(Refer to section 12.17.)
The servo-on (SON) is turned off.
Review the wiring and the driver
programs in order that the servo-on
(SON) is not turned to off in
operation.
The command pulses voltage level is
low at the open collector system.
(normal value: 24VDC)
Review the wiring and command
pulse specifications.
Replace the driver if an error cannot
be detected.
The command pulses ripple error
occurs due to a long command cable.
Shorten the wiring length.
Differential system: 10m or shorter
Open collector system: 2m or
shorter
The cumulative feedback pulses x
the travel distance per pulse does
not match with the actual machine
position.
1. A machine slipped.
2. A machine backlash is big.
Adjust the machine parts.
The position is
misaligned in
operation after
the home position
return.
The cumulative feedback pulses
do not match with the cumulative
command pulses
the electronic
gear setting value.
Temporary breaking of a power line
Review the wiring.
1. The servo gain is low.
2. The auto tuning response is low.
3. The setting time is late.
Increase the auto tuning response
and then adjust the gains again.
(Refer to chapter 7.)
1. The forward rotation stroke end (LSP) or
the reverse rotation stroke end (LSN) is
turned off.
(AL.99 occurred.)
2. Clear (CR) or reset (RES) is turned on.
1. Review the wiring and the sequence of
each signal.
2. If a noise may malfunction greatly,
make the input filter setting (parameter
No.PD19) value bigger.
1. If the safe operation is possible,
repeat acceleration/deceleration
4 times or more to complete the
auto tuning.
2. Increase the auto tuning
response (parameter No.PA09).
(except the manual mode)
The auto tuning response is low.
Increase the auto tuning response
and then adjust the gains again.
(Refer to chapter 7.)
Check the settings as follows for
the geared servo motor.
1. The travel distance per
revolution of the servo motor
(Set by the driver)
2. Command input pulses per
revolution (parameter No.PA05)
3. Electronic gear (parameter
No.PA06/PA07)
The calculation of the reduction ratio
is not correct.
Review the setting of the reduction
ratio.
Check the in-position range
(parameter No.PA10).
The in-position range is too large.
Set the in-position range smaller
than the current setting.
Содержание LECSB Series
Страница 1: ...PRODUCT NAME AC Servo Motor Driver MODEL Series LECSB Series Doc no JXC OMT0021 B ...
Страница 17: ...7 App 6 Compliance with the European EC directives App 7 App 7 Conformance with UL C UL standard App 10 ...
Страница 255: ...10 1 10 OUTLINE DRAWINGS 10 OUTLINE DRAWINGS 2 10 1 Driver 2 10 2 Connector 4 ...