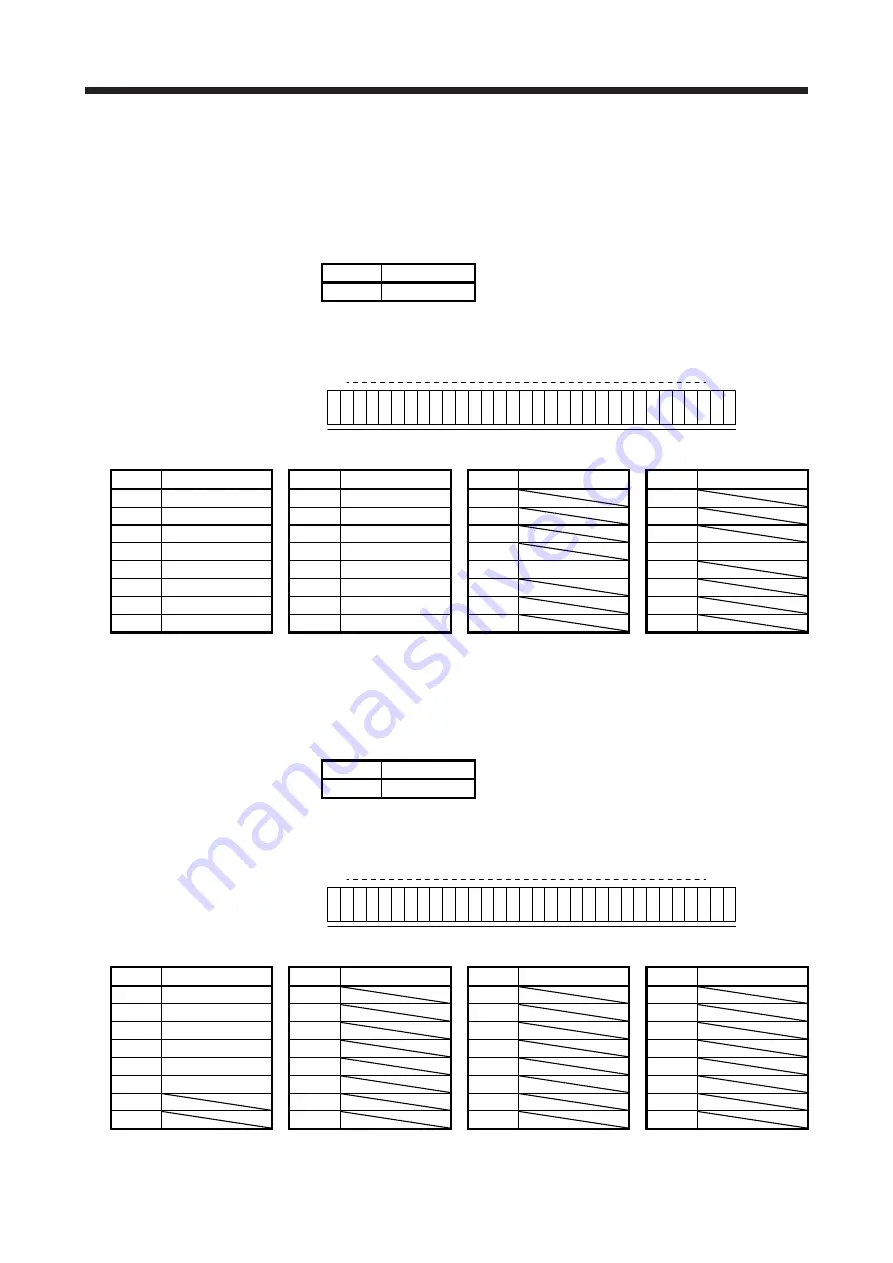
12. COMMUNICATION FUNCTION (MITSUBISHI ELECTRIC GENERAL-PURPOSE AC SERVO PROTOCOL)
12 - 22
12.5.4 External I/O signal status (DIO diagnosis)
(1) Reading input device status
The following shows how to read the status of the input devices.
(a) Transmission
Transmit command [1] [2] and data No. [0] [0].
Command Data
No.
[1] [2]
[0] [0]
(b) Return
The slave station returns the status of the input devices.
b31
b1b0
1: On
0: Off
Command of each bit is transmitted to the master station as hexadecimal data.
Bit Symbol
Bit Symbol
Bit Symbol
Bit Symbol
0 SON
8 SP1
16
24
1 LSP
9 SP2
17
25
2
LSN
10
SP3
18
26
3
TL
11
ST1/RS2 19
27
CDP
4
TL1
12
ST2/RS1 20
STAB2
28
5
PC
13
CM1
21
29
6
RES
14
CM2
22
30
7
CR
15
LOP
23
31
(2) Reading external input pin status
The following shows how to read the on/off status of the external input pins.
(a) Transmission
Transmit command [1] [2] and data No. [4] [0].
Command Data
No.
[1] [2]
[4] [0]
(b) Return
The on/off status of the input pins are returned.
b31
b1b0
1: On
0: Off
Command of each bit is transmitted to the master station as hexadecimal data.
Bit
CN1 connector pin
Bit
CN1 connector pin
Bit
CN1 connector pin
Bit
CN1 connector pin
0 43
8
16
24
1 44
9
17
25
2
42
10
18
26
3
15
11
19
27
4
19
12
20
28
5
41
13
21
29
6
14
22
30
7
15
23
31
Содержание MR-JE-_A
Страница 9: ...A 8 MEMO ...
Страница 15: ...6 MEMO ...
Страница 29: ...1 FUNCTIONS AND CONFIGURATION 1 14 MEMO ...
Страница 139: ...4 STARTUP 4 38 MEMO ...
Страница 187: ...5 PARAMETERS 5 48 MEMO ...
Страница 221: ...6 NORMAL GAIN ADJUSTMENT 6 34 MEMO ...
Страница 259: ...8 TROUBLESHOOTING 8 8 MEMO ...
Страница 264: ...9 DIMENSIONS 9 5 2 SCR connector system 3M Receptacle 36210 0100PL Shell kit 36310 3200 008 Unit mm 34 8 39 5 22 4 11 0 ...
Страница 265: ...9 DIMENSIONS 9 6 MEMO ...
Страница 273: ...10 CHARACTERISTICS 10 8 MEMO ...
Страница 339: ...12 COMMUNICATION FUNCTION MITSUBISHI ELECTRIC GENERAL PURPOSE AC SERVO PROTOCOL 12 34 MEMO ...