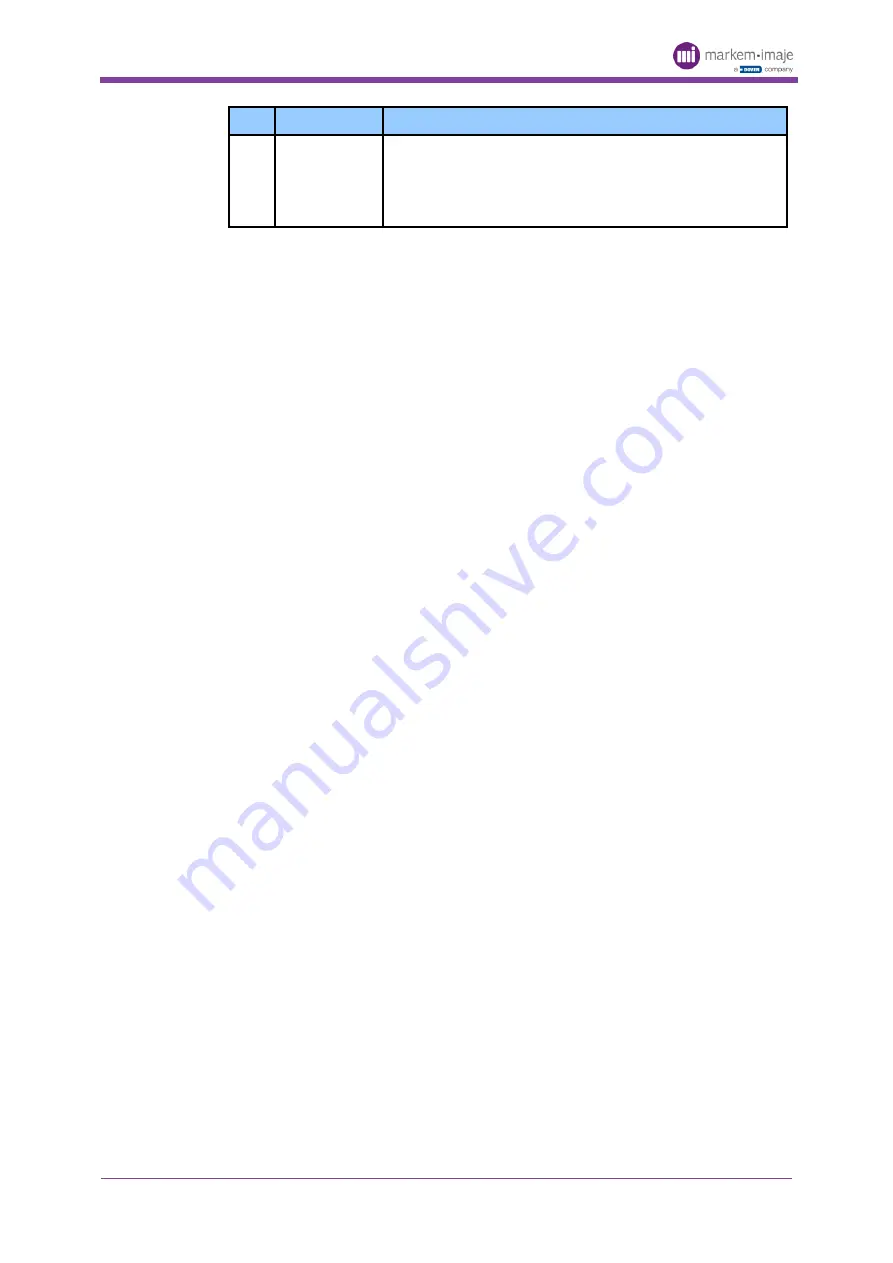
Machine Description
Operating Instructions
© Copyright by Markem-Imaje CSAT GmbH
Page 190 / 370
Subject to Technical Modifications
ITS6_135_Manual_EN.doc
Pos. Item
Meaning
4
Usefule life
pre-curing
Setpoint at which, when reached, the operator should be
notified in several ways (cf. Section 4.12) that the pre-
curing has nearly reached the end of its useful life.
The “command prompt” key opens an input box with which
the setpoint can be entered manually.