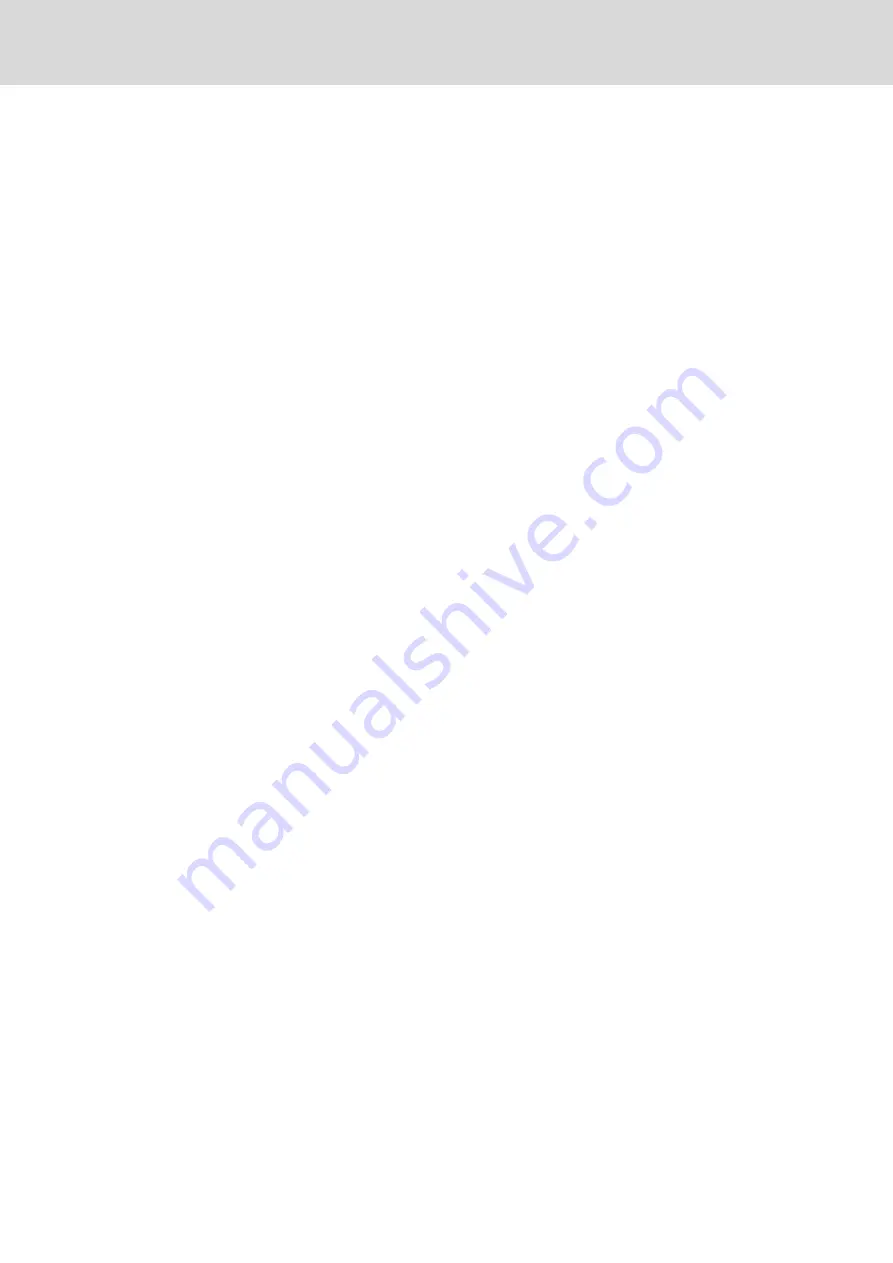
If 105 °C are exceeded, the motor temperature warning is generated; after 30
seconds, power is switched off.
The motor has been correctly sized, if the difference between amplifier
temperature read from the parameter and ambient temperature remains at
less than 60 K in operation.
See also "S-0-0384, Amplifier temperature".
7.2.5
Switching frequency
The nominal values refer to a switching frequency of 4 kHz.
Operation with 8 kHz is possible and has the following effect:
●
Continuous torque and peak torque are considerably reduced
●
Higher basic losses cause higher motor temperature rise already in no-
load operation
See also "P-0-0001, Switching frequency of the power output stage".
7.3
Notes on mechanical project planning
7.3.1
Mounting clearance
The mounting clearance has to comply with both mechanical and thermal
requirements. The mechanical requirements are complied with by taking the
dimensions of the components and their attachments (e.g., cables) into
account. Observe the minimum mounting clearances (dimensions) specified
in the dimensional drawings.
To comply with the thermal requirements, it has to be possible to dissipate
the power dissipation generated in the mounting clearance (e.g. control
cabinet) while the (local) ambient temperature does not exceed the allowed
ambient temperature T
a_work
.
KCU ventilation
Take the air intake and air outlet into account for ventilation.
Observe the data d
top
, d
bot
and d
hor
in the data sheet of KCU.
KSM, KMS mounting clearance
Make sure there is sufficient heat dissipation (e.g., ventilation, surface) in the
mounting clearance, particularly in the case of "closed" mounting situations.
Make sure that the cooling air can freely circulate around the housing surface
to avoid pockets of heat. Keep the housing surface which has a cooling effect
free from insulating dirt.
7.3.2
Output shaft
Plain shaft
The recommended standard design provides a friction-locked shaft-hub
connection without backlash and excellent running smoothness. Use
clamping sets, clamping sleeves or clamping elements to couple the machine
elements to be driven.
Output shaft with key
The optional key according to DIN 6885, sheet 1, edition 08‑1968, permits
keyed transmission of torques with constant direction, with low requirements
on the shaft-hub connection.
248/407
Notes on project planning
IndraDrive Mi Drive Systems with KCU02, KSM02,
KMS02/03, KMV03, KNK03, KLC03
Bosch Rexroth AG R911335703_Edition 04
Содержание Rexroth IndraDrive Mi KCU02
Страница 272: ...258 407 IndraDrive Mi Drive Systems with KCU02 KSM02 KMS02 03 KMV03 KNK03 KLC03 Bosch Rexroth AG R911335703_Edition 04 ...
Страница 290: ...276 407 IndraDrive Mi Drive Systems with KCU02 KSM02 KMS02 03 KMV03 KNK03 KLC03 Bosch Rexroth AG R911335703_Edition 04 ...
Страница 312: ...298 407 IndraDrive Mi Drive Systems with KCU02 KSM02 KMS02 03 KMV03 KNK03 KLC03 Bosch Rexroth AG R911335703_Edition 04 ...
Страница 378: ...364 407 IndraDrive Mi Drive Systems with KCU02 KSM02 KMS02 03 KMV03 KNK03 KLC03 Bosch Rexroth AG R911335703_Edition 04 ...
Страница 382: ...368 407 IndraDrive Mi Drive Systems with KCU02 KSM02 KMS02 03 KMV03 KNK03 KLC03 Bosch Rexroth AG R911335703_Edition 04 ...
Страница 408: ...394 407 IndraDrive Mi Drive Systems with KCU02 KSM02 KMS02 03 KMV03 KNK03 KLC03 Bosch Rexroth AG R911335703_Edition 04 ...
Страница 420: ...Notes 406 407 IndraDrive Mi Drive Systems with KCU02 KSM02 KMS02 03 KMV03 KNK03 KLC03 ...
Страница 421: ...Notes IndraDrive Mi Drive Systems with KCU02 KSM02 KMS02 03 KMV03 KNK03 KLC03 407 407 ...