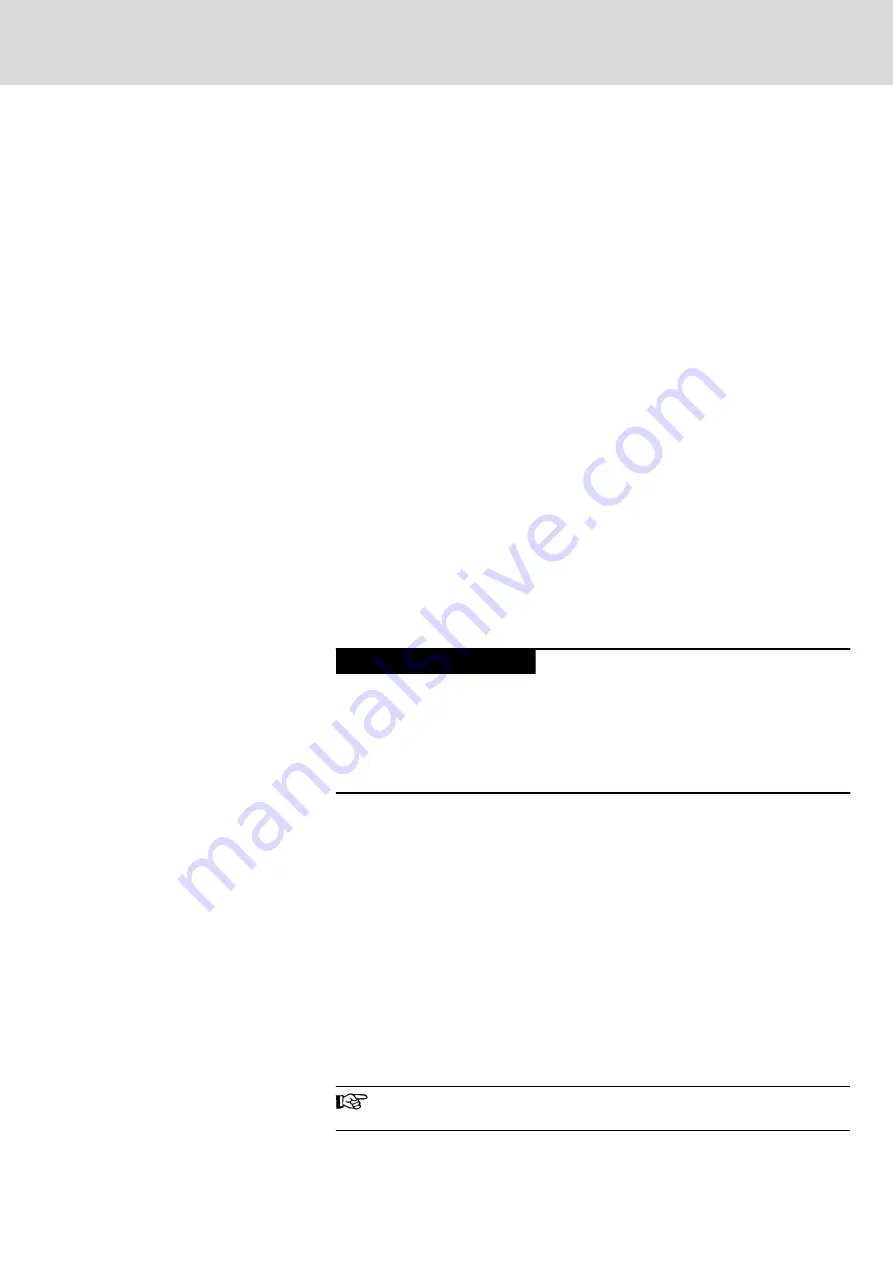
Normal operation
In normal operation, using the holding brake for clamping (holding) an axis in
standstill, the "static holding torque" (M4) – static friction (friction coefficient
μ
H
) specified in the data sheets takes effect.
Failure (E-Stop)
In the case of failure (E-Stop), where the holding brake is used to decelerate
a moving axis, the "dynamic braking torque" – sliding friction (friction
coefficient μ
G
) applies.
The dynamic braking torque is lower than the indicated static holding torque
M4. It is approx. 0.75 … 0.8 x M4. Therefore, observe the following
description of dynamic sizing.
Dynamic sizing
The load torque has to be lower than the minimum dynamic torque which the
brake can provide. Otherwise, the dynamic brake torque is not sufficient to
stop the axis.
If a mass is to be decelerated in a defined time or over a defined distance,
the mass inertia of the whole system additionally has to be taken into
account.
Other important aspects for sizing
The holding brake is not a safety brake (cf. DIN EN 954 / 03.97 and
Information Sheet for vertical axes published by the institution for statutory
accident
insurance
and
prevention
["Süddeutsche
Metall-
Berufsgenossenschaft"]). Due to uncontrollable adverse factors, such as film
rust on the brake friction surface, the holding brake torque can be reduced.
Additionally, overvoltage and too high temperatures can weaken the
permanent magnets and the brake.
Sizing - Recommendation
Considering these factors, the following recommendation can be made for
sizing holding brakes at axes:
The holding torque required for the application should not exceed a maximum
of 60% of the static holding torque (M4) of the holding brake used.
Holding torque reduction and premature wear
occur when braking moving axes!
NOTICE
Do not use the holding brake to stop a moving axis during normal operation.
This is allowed for E-Stop situations only. In this situation, the specified rated
torque of the holding brake (M4) is reduced to the dynamic braking torque.
Complete deterioration of the holding brake can be expected after approx.
20,000 revolutions of the brake when applied.
Observe the commissioning instructions for holding brakes. See also
Functional Description of firmware (index entry "Motor holding brake →
Operating behavior").
7.3.5
Mechanically attaching driving elements
General information
For all driving elements attched to the output shaft (e.g., gearboxes,
couplings, pinions), the following instructions absolutely have to be observed.
Redundant bearings
Generally, redundant bearings are to be avoided by all means when
attaching driving elements. The tolerances inevitably present in such cases
will lead to additional forces acting on the bearing of the motor shaft and,
should the occasion arise, to a distinctly reduced service life of the bearing.
If redundant attachment cannot be avoided, it is absolutely
necessary that you consult Rexroth.
IndraDrive Mi Drive Systems with KCU02, KSM02,
KMS02/03, KMV03, KNK03, KLC03
255/407
Notes on project planning
R911335703_Edition 04 Bosch Rexroth AG
Содержание Rexroth IndraDrive Mi KCU02
Страница 272: ...258 407 IndraDrive Mi Drive Systems with KCU02 KSM02 KMS02 03 KMV03 KNK03 KLC03 Bosch Rexroth AG R911335703_Edition 04 ...
Страница 290: ...276 407 IndraDrive Mi Drive Systems with KCU02 KSM02 KMS02 03 KMV03 KNK03 KLC03 Bosch Rexroth AG R911335703_Edition 04 ...
Страница 312: ...298 407 IndraDrive Mi Drive Systems with KCU02 KSM02 KMS02 03 KMV03 KNK03 KLC03 Bosch Rexroth AG R911335703_Edition 04 ...
Страница 378: ...364 407 IndraDrive Mi Drive Systems with KCU02 KSM02 KMS02 03 KMV03 KNK03 KLC03 Bosch Rexroth AG R911335703_Edition 04 ...
Страница 382: ...368 407 IndraDrive Mi Drive Systems with KCU02 KSM02 KMS02 03 KMV03 KNK03 KLC03 Bosch Rexroth AG R911335703_Edition 04 ...
Страница 408: ...394 407 IndraDrive Mi Drive Systems with KCU02 KSM02 KMS02 03 KMV03 KNK03 KLC03 Bosch Rexroth AG R911335703_Edition 04 ...
Страница 420: ...Notes 406 407 IndraDrive Mi Drive Systems with KCU02 KSM02 KMS02 03 KMV03 KNK03 KLC03 ...
Страница 421: ...Notes IndraDrive Mi Drive Systems with KCU02 KSM02 KMS02 03 KMV03 KNK03 KLC03 407 407 ...