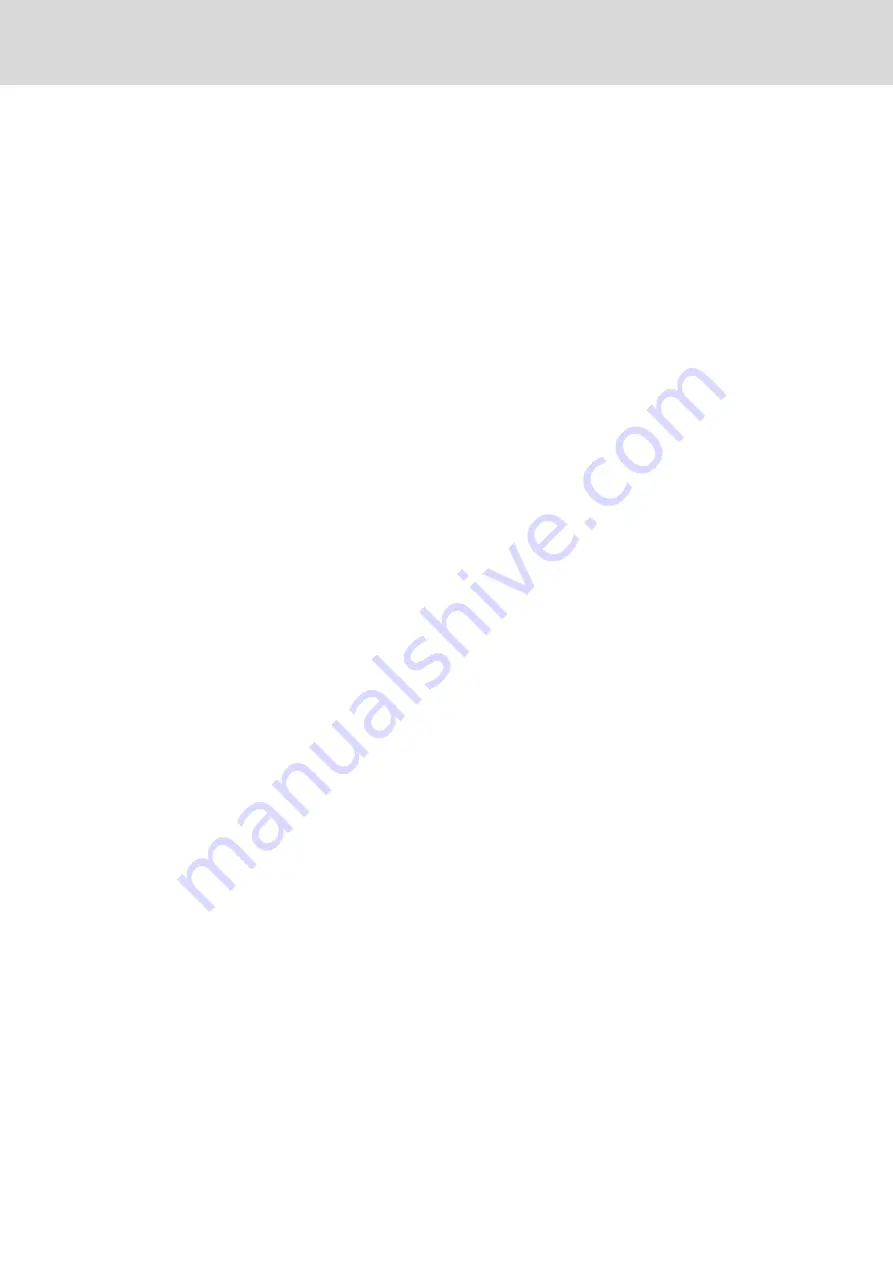
●
Keep free and clear of the machine’s range of motion and moving
machine parts. Prevent personnel from accidentally entering the
machine’s range of motion by using, for example:
–
Safety fences
–
Safety guards
–
Protective coverings
–
Light barriers
●
Make sure the safety fences and protective coverings are strong enough
to resist maximum possible kinetic energy.
●
Mount emergency stopping switches in the immediate reach of the
operator. Before commissioning, verify that the emergency stopping
equipment works. Do not operate the machine if the emergency
stopping switch is not working.
●
Prevent unintended start-up. Isolate the drive power connection by
means of OFF switches/OFF buttons or use a safe starting lockout.
●
Make sure that the drives are brought to safe standstill before accessing
or entering the danger zone.
●
Additionally secure vertical axes against falling or dropping after
switching off the motor power by, for example,
–
mechanically securing the vertical axes,
–
adding an external braking/arrester/clamping mechanism or
–
ensuring sufficient counterbalancing of the vertical axes.
●
The standard equipment motor holding brake or an external holding
brake controlled by the drive controller is not sufficient to guarantee
personal safety!
●
Disconnect electrical power to the components of the electric drive and
control system using the master switch and secure them from
reconnection ("lock out") for:
–
Maintenance and repair work
–
Cleaning of equipment
–
Long periods of discontinued equipment use
●
Prevent the operation of high-frequency, remote control and radio
equipment near components of the electric drive and control system and
their supply leads. If the use of these devices cannot be avoided, check
the machine or installation, at initial commissioning of the electric drive
and control system, for possible malfunctions when operating such high-
frequency, remote control and radio equipment in its possible positions
of normal use. It might possibly be necessary to perform a special
electromagnetic compatibility (EMC) test.
3.3.4
Protection against electromagnetic and magnetic fields during opera‐
tion and mounting
Electromagnetic and magnetic fields!
Health hazard for persons with active implantable medical devices (AIMD)
such as pacemakers or passive metallic implants.
●
Hazards for the above-mentioned groups of persons by electromagnetic
and magnetic fields in the immediate vicinity of drive controllers and the
associated current-carrying conductors.
IndraDrive Mi Drive Systems with KCU02, KSM02,
KMS02/03, KMV03, KNK03, KLC03
41/407
Safety instructions for electric drives and controls
R911335703_Edition 04 Bosch Rexroth AG
Содержание Rexroth IndraDrive Mi KCU02
Страница 272: ...258 407 IndraDrive Mi Drive Systems with KCU02 KSM02 KMS02 03 KMV03 KNK03 KLC03 Bosch Rexroth AG R911335703_Edition 04 ...
Страница 290: ...276 407 IndraDrive Mi Drive Systems with KCU02 KSM02 KMS02 03 KMV03 KNK03 KLC03 Bosch Rexroth AG R911335703_Edition 04 ...
Страница 312: ...298 407 IndraDrive Mi Drive Systems with KCU02 KSM02 KMS02 03 KMV03 KNK03 KLC03 Bosch Rexroth AG R911335703_Edition 04 ...
Страница 378: ...364 407 IndraDrive Mi Drive Systems with KCU02 KSM02 KMS02 03 KMV03 KNK03 KLC03 Bosch Rexroth AG R911335703_Edition 04 ...
Страница 382: ...368 407 IndraDrive Mi Drive Systems with KCU02 KSM02 KMS02 03 KMV03 KNK03 KLC03 Bosch Rexroth AG R911335703_Edition 04 ...
Страница 408: ...394 407 IndraDrive Mi Drive Systems with KCU02 KSM02 KMS02 03 KMV03 KNK03 KLC03 Bosch Rexroth AG R911335703_Edition 04 ...
Страница 420: ...Notes 406 407 IndraDrive Mi Drive Systems with KCU02 KSM02 KMS02 03 KMV03 KNK03 KLC03 ...
Страница 421: ...Notes IndraDrive Mi Drive Systems with KCU02 KSM02 KMS02 03 KMV03 KNK03 KLC03 407 407 ...