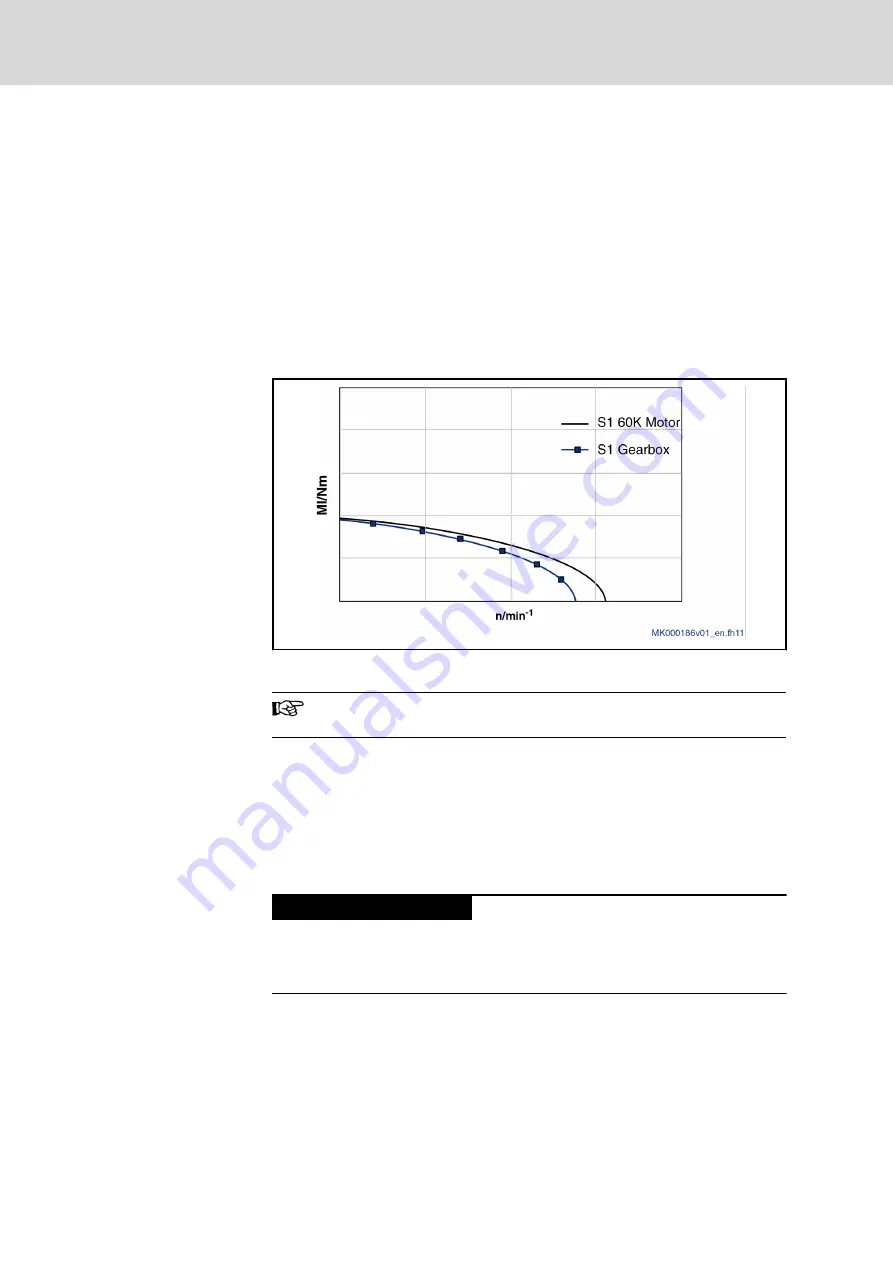
Gearbox attachment
The machine design and the attachment elements used have to be carefully
adapted to the motor type so that the load limits of shaft and bearing are not
exceeded.
When gearboxes are attached to motors, this changes the thermal
connection of the motor to the machine or installation design.
According to the gearbox type, the heat generation at the gearbox is
different. In any case, gearbox attachment reduces the heat dissipation of the
motor via the flange. This has to be taken into account when doing the
project planning for the installation.
To avoid thermal overload of motors when using gearboxes, it is necessary to
reduce the specified performance data.
Fig. 7-30:
Qualitative change in the S1 characteristic in the case of gearbox at‐
tachment
The torques specified in the motor characteristics have to be
reduced by approx. 10–20% when gearboxes are attached.
Observe all other notes and requirements contained in the documentations
on the gearboxes used.
Coupling attachment
The machine design and the attachment elements used have to be carefully
adapted to the motor type so that the load limits of shaft and bearing are not
exceeded.
Risk of damage!
NOTICE
When connecting extremely stiff couplings, the radial force which constantly
changes the angular position may cause an impermissibly high load on the
shaft and bearing.
Bevel gear pinions or skew bevel driving pinions
Owing to thermal effects, the flange-side end of the output shaft may offset
by up to 0.6 mm in relation to the motor housing. If helical driving pinions or
bevel gear pinions directly attached to the output shaft are used, this change
in position will lead to
256/407
Notes on project planning
IndraDrive Mi Drive Systems with KCU02, KSM02,
KMS02/03, KMV03, KNK03, KLC03
Bosch Rexroth AG R911335703_Edition 04
Содержание Rexroth IndraDrive Mi KCU02
Страница 272: ...258 407 IndraDrive Mi Drive Systems with KCU02 KSM02 KMS02 03 KMV03 KNK03 KLC03 Bosch Rexroth AG R911335703_Edition 04 ...
Страница 290: ...276 407 IndraDrive Mi Drive Systems with KCU02 KSM02 KMS02 03 KMV03 KNK03 KLC03 Bosch Rexroth AG R911335703_Edition 04 ...
Страница 312: ...298 407 IndraDrive Mi Drive Systems with KCU02 KSM02 KMS02 03 KMV03 KNK03 KLC03 Bosch Rexroth AG R911335703_Edition 04 ...
Страница 378: ...364 407 IndraDrive Mi Drive Systems with KCU02 KSM02 KMS02 03 KMV03 KNK03 KLC03 Bosch Rexroth AG R911335703_Edition 04 ...
Страница 382: ...368 407 IndraDrive Mi Drive Systems with KCU02 KSM02 KMS02 03 KMV03 KNK03 KLC03 Bosch Rexroth AG R911335703_Edition 04 ...
Страница 408: ...394 407 IndraDrive Mi Drive Systems with KCU02 KSM02 KMS02 03 KMV03 KNK03 KLC03 Bosch Rexroth AG R911335703_Edition 04 ...
Страница 420: ...Notes 406 407 IndraDrive Mi Drive Systems with KCU02 KSM02 KMS02 03 KMV03 KNK03 KLC03 ...
Страница 421: ...Notes IndraDrive Mi Drive Systems with KCU02 KSM02 KMS02 03 KMV03 KNK03 KLC03 407 407 ...