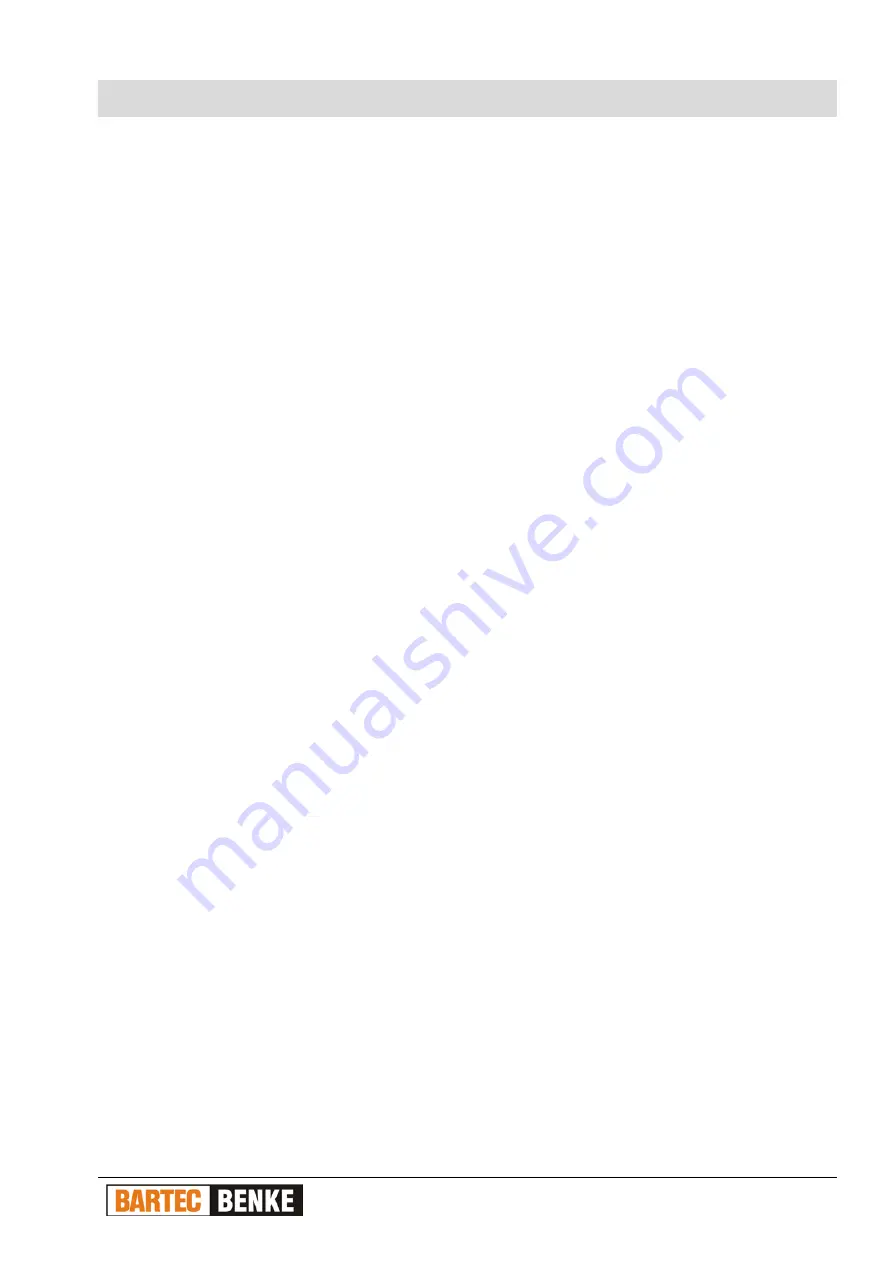
Distillation Process Analyzer DPA-4.5
Contents
General information ....................................................................... 8
1.1
Information on the operating manual ............................. 8
1.2
Explanation of symbols .................................................. 9
1.3
Intended use ................................................................ 11
1.4
Operator obligations .................................................... 12
1.5
Limitation of liability ...................................................... 13
1.6
Copyright ...................................................................... 13
1.7
Replacement parts ....................................................... 14
1.8
Customer service ......................................................... 14
2
Safety .................................................................................... 15
2.1
Dangers and risks ........................................................ 15
2.2
Hazardous substances ................................................ 18
2.3
Explosion protection .................................................... 20
2.3.1
Marking ........................................................... 20
2.3.2
Ignition protection types and certificates ......... 23
2.3.3
Special conditions ........................................... 24
2.4
Safety devices.............................................................. 25
2.4.1
Overview of safety devices on the analyzer ... 26
2.4.2
Control box (Ex p) ........................................... 27
2.4.3
Measuring unit box (Ex d) ............................... 29
2.4.4
Junction boxes (Ex e) ..................................... 31
2.4.5
Potential equalization ...................................... 31
2.4.6
Main switch and emergency off device ........... 32
2.4.7
Signs and safety warnings .............................. 32
2.5
Signs ............................................................................ 33
2.5.1
Overview of signs ............................................ 34
2.5.2
Warnings ......................................................... 36
2.5.3
Command signs .............................................. 37
2.6
Safety measures at the installation location ................ 38
2.7
Safety information on explosion protection .................. 39
2.8
Personnel ..................................................................... 41
2.9
Personal protective equipment .................................... 43
2.10
Securing against being switched on again .................. 45
2.11
Behavior in dangerous situations and in the event of
an accident ................................................................... 46
3
Technical data ...................................................................... 47
3.1
Measuring process ...................................................... 47
3.2
Explosion protection .................................................... 48
3.3
Product flows ............................................................... 48
3.4
Sample properties ........................................................ 49
3.5
Auxiliary media............................................................. 50
3.6
Electrical data .............................................................. 51
December 2013
3