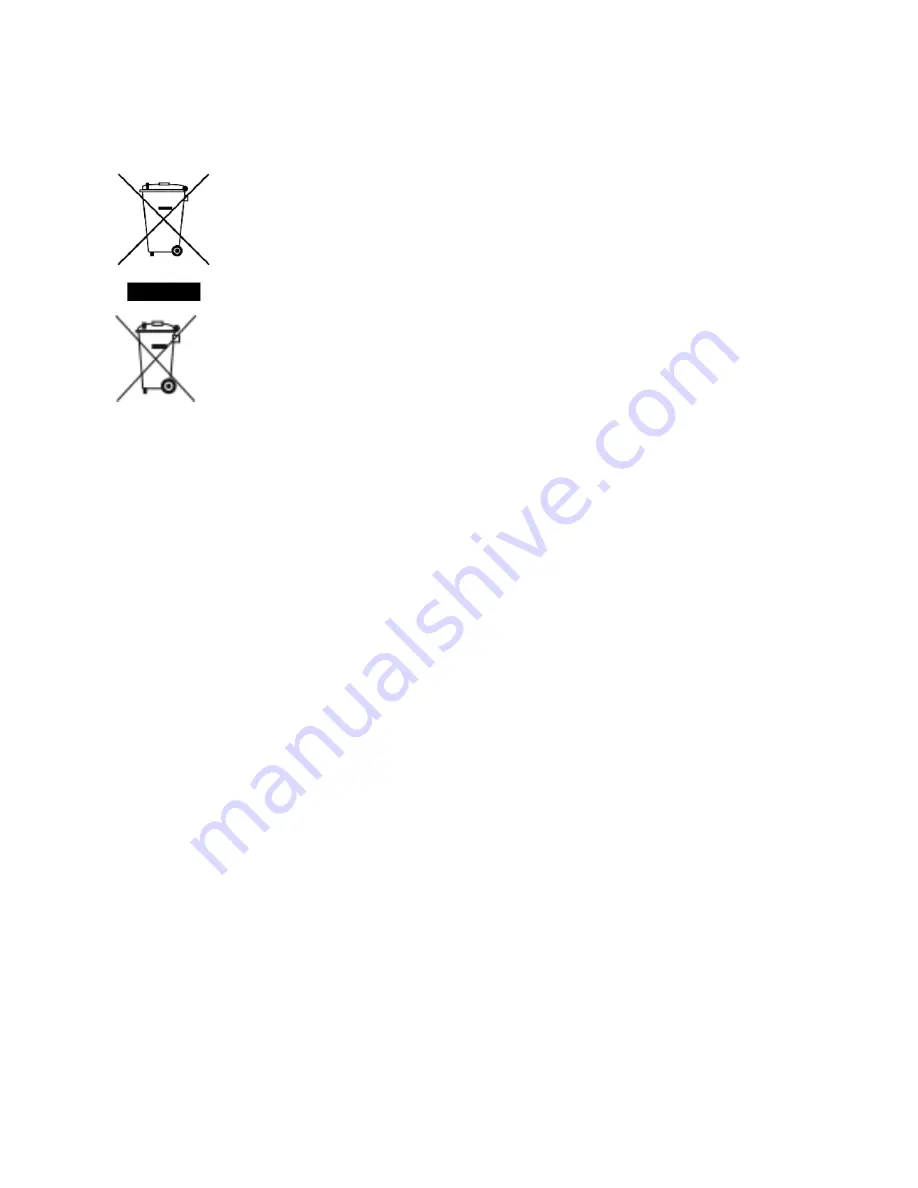
EEuurrooppeeaann U
Unniioonn
These symbols indicate that this product is not to be disposed of with your
household waste, according to the Waste Electrical and Electronic Equipment
(WEEE) Directive (2012/19/EU), the Battery Directive (2006/66/EC) and national
legislation implementing those Directives.
If a chemical symbol is printed beneath the symbol shown above, in accordance with the
Battery Directive, this indicates that a heavy metal (Hg = Mercury, Cd = Cadmium, Pb =
Lead) is present in this battery or accumulator at a concentration above an applicable
threshold specified in the Battery Directive.
Some equipment can be used in both a domestic or household and a professional or
business application. Private households within European Union can return used electrical
and electronic equipment to designated collection facilities free of charge. For more
information about collection and recycling of old products and batteries, contact your
local municipality, your waste disposal service or the point of sale where you purchased
the items. In some member states, when you purchase new equipment, your local retailer
may be required to take back your old equipment free of charge. For more information,
contact your retailer.
Business Users in the European Union, in accordance with European legislation, end of life
electrical and electronic equipment subject to disposal must be managed within agreed
procedures. If you discard electrical and electronic equipment, contact your dealer or
supplier, local reseller or Xerox representative for end of life take-back information prior to
disposal.
Improper handling of this type of waste can have a possible impact on the environment
and human health due to potentially hazardous substances that are generally associated
with EEE. Your cooperation in the correct disposal of this product will contribute to the
effective usage of natural resources.
D
Diissppoossaall O
Ouuttssiiddee ooff tthhee EEuurrooppeeaann U
Unniioonn
These symbols are only valid in the European Union. If you want to discard these items, contact your
local authorities or dealer and ask for the correct method of disposal
O
Otthheerr C
Coouunnttrriieess
Contact your local waste management authority to request a disposal guidance.
40
Xerox
®
Versant
®
4100 Press
User Documentation
Summary of Contents for Versant 4100 Press
Page 1: ...Version 1 0 November 2020 702P08365 Xerox Versant 4100 Press User Documentation...
Page 284: ...284 Xerox Versant 4100 Press User Documentation Working With...
Page 426: ...426 Xerox Versant 4100 Press User Documentation Troubleshooting...
Page 428: ...428 Xerox Versant 4100 Press User Documentation For Administrators...
Page 429: ......
Page 430: ......