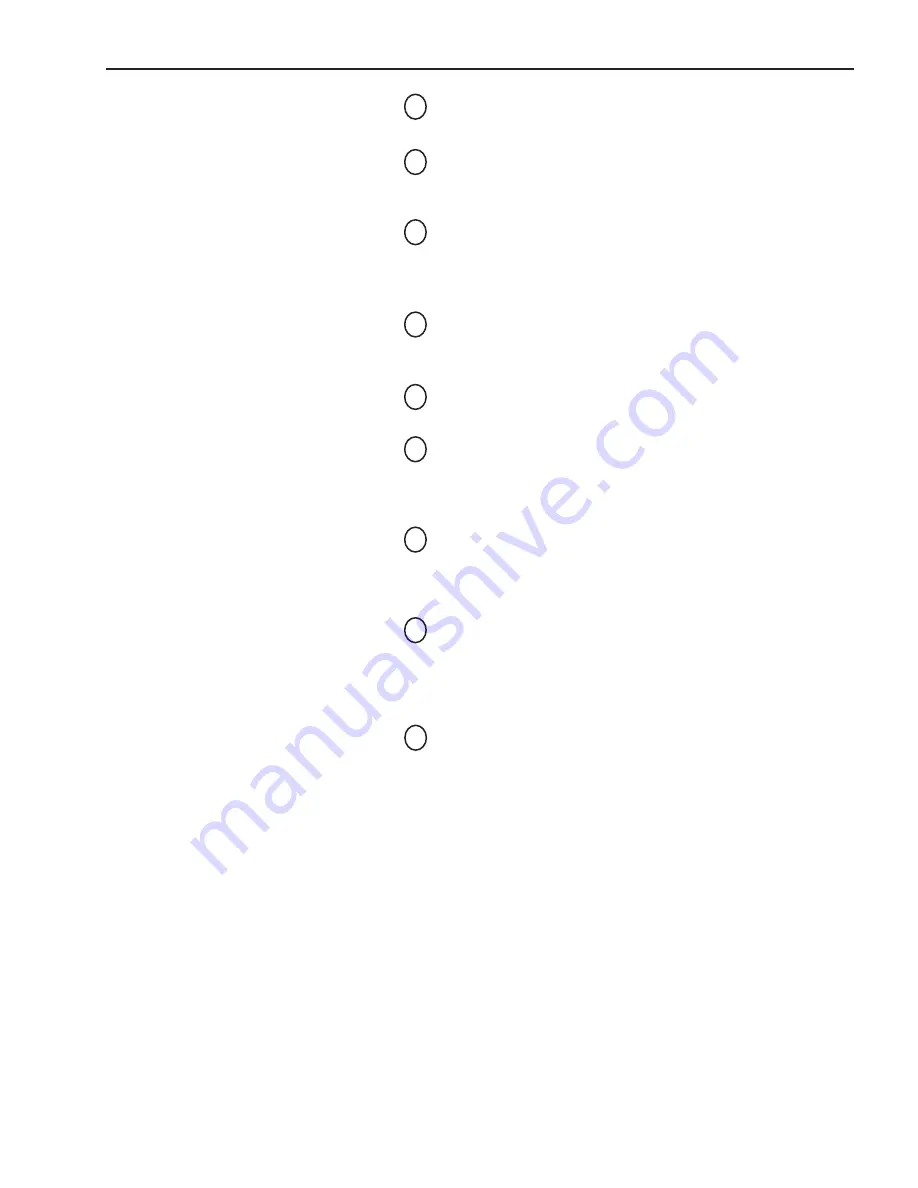
CHAPTER 3 - INSTALLATION AND CONNECTION
60
X1E (33 and 34) is only available on the models fitted with
cooling fans;
For integral motor protection the installation of one or more PTC
thermistors (PTC at DI6) or thermostats (external fault at DI4
to DI6) is recommended;
Remember that when a command via two-wire digital input is
used (the switch is normally open with retention), every time
the power supply returns, after any fault, the motor starts im-
mediately if the switch remains closed;
In case of maintenance services, remove the power supply
fuses or disconnect the power supply, thus ensuring complete
equipment disconnection from power.
An emergency stop can be obtained by disconnecting the
electronics power supply.
The contactors must be of the same model and must support
the motor starting current. For safety reasons, auxiliary con-
tacts must be used to keep both contactors from closing at the
same time.
Use a digital input set to “General Enable” to disable the motor
without braking. Use a digital input set to “No Braking”, for sa-
fety reasons, with the possibility of fitting a motor stop sensor
to disable the braking.
The use of an external By-pass contactor is optional for models
950A to 1400A that do not have an internal By-pass contactor.
This contactor is also recommended, in models with an internal
By-pass, for use in applications where the motor can frequently
present a locked rotor during the full operation cycle.
To maintain the current indications and protections, when using
the external By-pass contactor, it is necessary to place the
current transformers on the Soft-Starter output. The current
transformers must be placed in the correct positions and direc-
tions as indicated. For more details see chapter 9.6.
5
6
4
7
8
9
10
11
12
Summary of Contents for SSW06
Page 2: ......