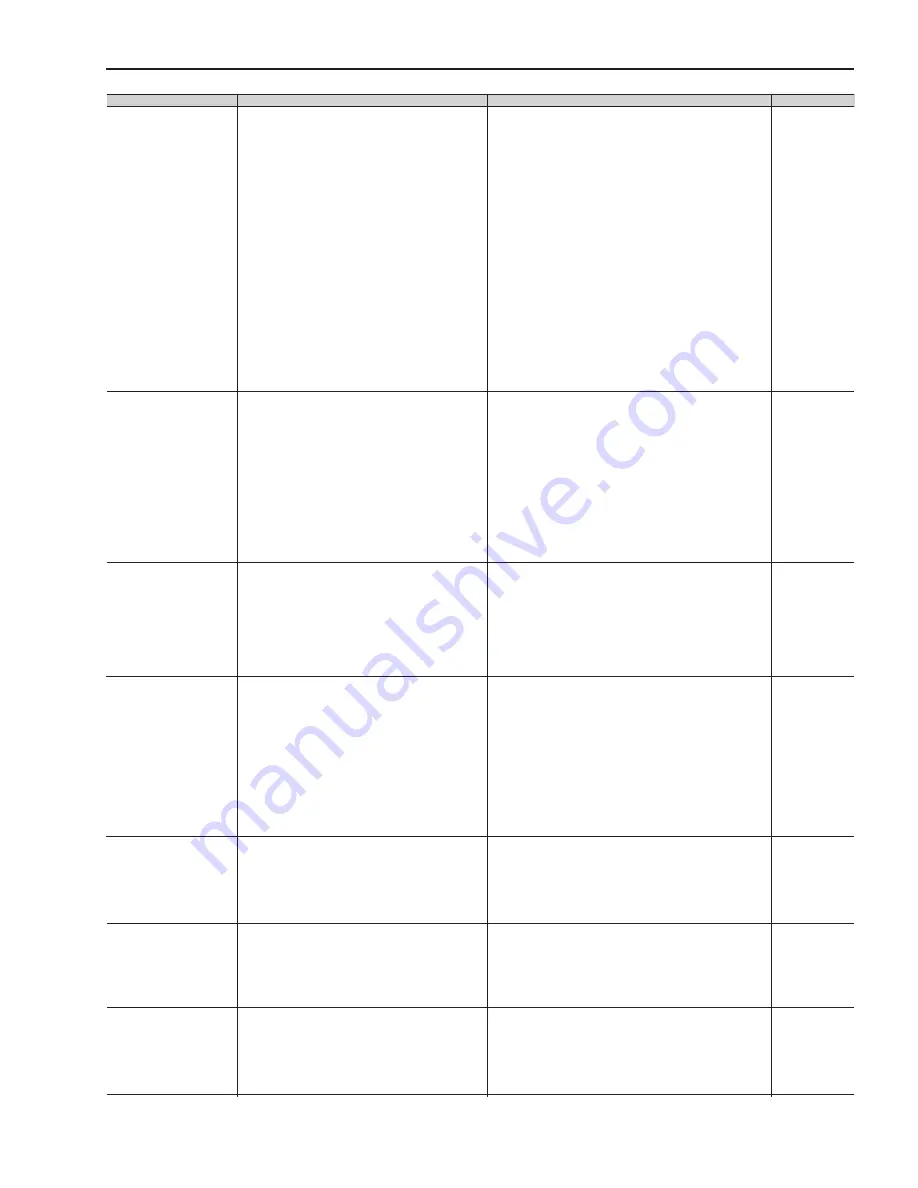
CHAPTER 8 - DIAGNOSTICS AND TROUBLESHOOTING
166
FAULT
E48 or A48
Ch1 Motor Temperature
Short Circuit
E49 or A49
Ch2 Motor Temperature
Short Circuit
E50 or A50
Ch3 Motor Temperature
Short Circuit
E51 or A51
Ch4 Motor Temperature
Short Circuit
E52 or A52
Ch5 Motor Temperature
Short Circuit
E57
Failure in the SCRs of
the Power Module R-U
E58
Failure in the SCRs of
the Power Module S-V
E59
Failure in the SCRs of
the Power Module T-W
E62
Too long time for the
current or torque limit
during the start
E63
Locked rotor
at the start end
E65 or A65
Motor undercurrent at
full voltage operation
E66 or A66
Motor overcurrent at
full voltage operation
E67
Wrong phase sequen-
ce at start
DESCRIPTION OF THE ACTUATION
It detects a short circuit of the temperature
channels, through the short circuit enters the
three wire of each sensor.
When the SCR is not switched on in less
than 50ms.
When the start time due to start with current
limit, current ramp or torque control is longer
than the time set at P102.
When at the end of the acceleration ramp
the current is not lower than 2x the nominal
motor current (P401x2) before closing of the
By-pass relay.
When the current is lower than programmed
during the programmed time. Nominal motor
current is used as reference.
When the current is higher than programmed
during the programmed time. The nominal
motor current is used as reference.
When the signal sequence of the synchro-
nism do not follow the
R
/1L1,
S
/3L2,
T
/5L3 sequence.
POSSIBLE CAUSES
Short circuit in the wires of the temperature sensor
of the motor.
Comment:
Programming of the broken wire actuation as error
or alarm is in the P691.
One of the SCRs of the indicated power module is
damaged.
Bad contact in the firing circuit cables of the
indicated power module, (R-U: X8 and X9, S-V: X10
and X11, T-W: X12 and X13).
Defective CPS6X board.
Time programmed at P102 is shorter than required.
The programmed current limit at P110 is too low.
The programmed current limit at any point of cur-
rent ramp is too low.
The programmed torque limit at any point of the
torque control is too low.
Stalled motor, locked rotor.
The nominal motor current that has been program-
med at P401 is wrong.
The time programmed at P102 is shorter than re-
quired to start the motor by voltage ramp.
The transformer that supplies the motor may be
saturated and requires too much time to recover
from the starting current.
Stalled motor, locked rotor.
For special motors that support this working condi-
tion you can set P617=0.
The percent value programmed as maximum
acceptable undercurrent limit (P610) is lower than
required for the motor and its application.
In applications with hydraulic pumps which may be
operated without load.
The percent value programmed as maximum
acceptable overcurrent limit (P612) is lower than
required for the motor and its application.
Motor with instantaneous overload.
Stalled motor, locked rotor.
Parameter P620 has been programmed without
need.
Wrong phase sequence.
This can be changed in another point of the power
supply line.
RESET
Power-on
Manual Reset
Auto-reset
DIx
Power-on
Manual Reset
DIx
Power-on
Manual Reset
DIx
Power-on
Manual Reset
DIx
Power-on
Manual Reset
Auto-reset
DIx
Power-on
Manual Reset
Auto-reset
DIx
Power-on
Manual Reset
DIx
Table 8.1 (Cont.)
- Detailed fault description
Summary of Contents for SSW06
Page 2: ......