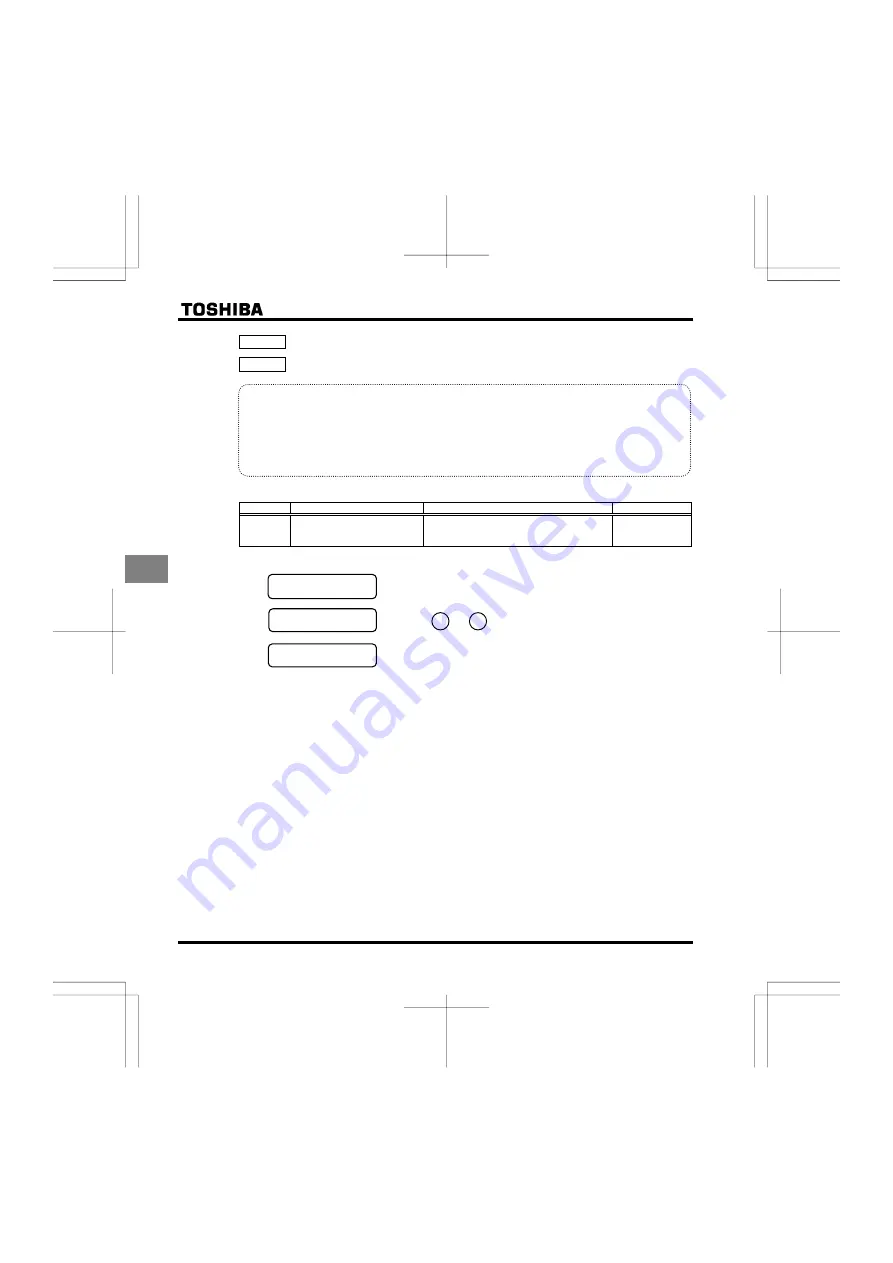
E6581381
E-8
5
EOQF
: Command mode selection
HOQF
: Frequency setting mode selection 1
•
Function
Remote mode selection, these parameters are used to specify which input device (operation panel,
terminal board, serial communication) takes priority in entering an operation stop command or a frequency
setting command, VIA, VIB, operation panel, serial communication device, external contact up/down).
At Local mode selection, the start/stop operation and frequency setting by operation panel is prior with no
relation of
EOQF
/
HOQF
setting.
<Command mode selection>
Title
Function
Adjustment range
Default setting
EOQF
Command mode selection
0: Terminal board
1: Operation panel
2: Serial communication
0
Programmed value
:
Terminal board
operation
ON and OFF of an external signal Runs and stops operation.
:
Operation panel
operation
Press the and keys on the operation panel to start and stop.
Serial communication
operation
Run and stop through serial communication.
* There are two types of function: the function that conforms to commands selected by
EOQF
, and the function
that conforms only to commands from the terminal board.
⇒
See the table of input terminal function selection in Chapter 11.
* When priority is given to commands from a linked computer or terminal board, they have priority over the
setting of
EOQF
.
STOP
RUN
Summary of Contents for TOSVERT VF-FS1 Series
Page 2: ......
Page 15: ...E6581381 A 3 1 1 3 Names and functions 1 3 1 Outside view Operation panel ...
Page 18: ...E6581381 A 6 1 VFFS1 2004 2037PM VFFS1 4004 4055PL Note EMC plate is supplied as standard ...
Page 36: ......
Page 40: ...E6581381 B 4 2 2 2 2 Standard connection diagram 2 ...
Page 54: ......
Page 56: ...E6581381 D 2 4 4 1 Flow of status monitor mode Flow of monitor as following ...
Page 66: ......
Page 180: ......
Page 196: ......
Page 208: ......
Page 233: ...E6581381 L 5 12 Outline drawing Fig A Fig B Fig C Fig D ...
Page 242: ......
Page 248: ......
Page 251: ......