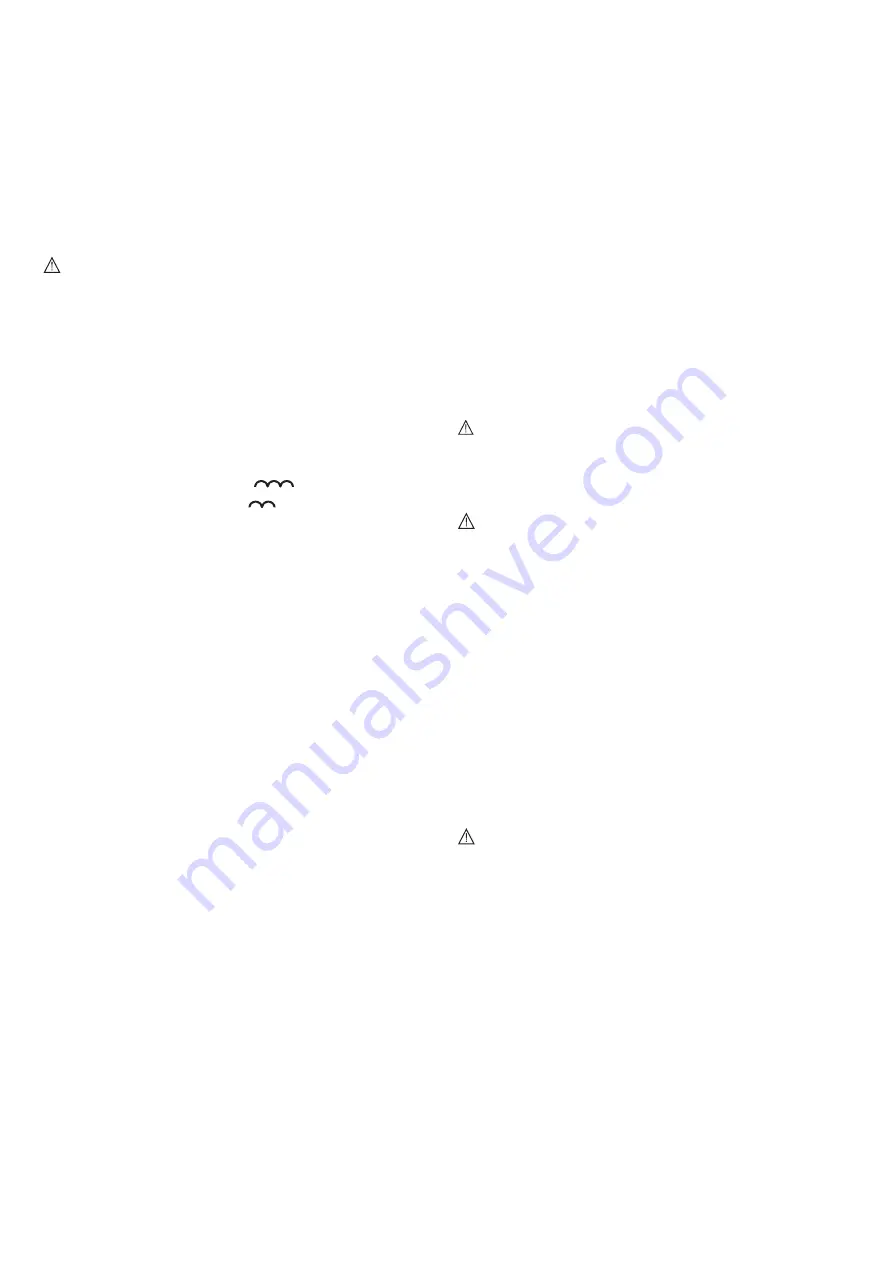
- 7 -
- Open the reel compartment door.
This process allows dented or deformed metal sheets to be re-shaped, without having
- Position the wire reel on the spindle, holding the end of the wire upwards; make sure
to hammer out the sheets from behind. This is particularly useful for sections of
the tab for pulling the spindle is correctly seated in its hole
(1a)
.
bodywork with inaccessible rear sides.
- Release the pressure counter-roller/s and move it/them away from the lower roller/s
The operation is carried out as follows:
- Replace the nozzle of the torch with the nozzle required for riveting. This nozzle has a
(2a)
.
side hole for housing the rivet.
- Make sure the puller roller is suitable for the wire being used
(2b)
.
- Turn the current adjustment switch to position 3.
- Free the end of the wire and remove the distorted end with a clean cut and no burr;
- Adjust the feed speed according to the current and the diameter of the wire used as if a
turn the reel anti-clockwise and thread the end of the wire into the wire-guide infeed,
welding operation was to be carried out.
pushing it 50-100mm into the wire guide of the torch fitting
(2c)
.
- Turn the switch to <TIMER> position.
- Re-position the counter-roller/s, adjusting the pressure to an intermediate value, and
- Set the time at 1-1.5 seconds
make sure that the wire is correctly positioned in the groove of the lower roller
(3)
.
A spot of welding will therefore be carried out at the point where the head of the rivet is
- Use the adjustment screw located at the centre of the spindle to apply a slight braking
located and so joining the latter to the metal sheet. The dented metal sheet can now be
pressure on the spindle itself
(1b)
.
re-shaped using the appropriate appliance
- Remove the nozzle and contact tip
(4a)
.
6.6 METAL SHEET HARDENING (FIG.M)
- Insert the welding machine plug in the power supply outlet, switch on the welding
This operation is only possible for compact welding machines with one or more earth
machine, press the torch button and wait for the end of the wire to pass through the
connectors.
whole of the wire guide hose and protrude by 10-15 cm from the front part of the
In order to carry out this process, the kit should be requested.
torch, release the button.
After welding and hammering, the metal sheet looses its original characteristics; body
___________________________________________________________________
work-shops normally use oxyacetylene welding torches to return the metal sheet to its
original state. This torch is used to heat the metal sheet up to about 800° Celsius and is
WARNING! During these operations the wire is live and subject to mechanical
then rapidly cooled using a cloth soaked with water.
stress; therefore if adequate precautions are not taken the wire could cause
The oxyacetylene equipment can now be replaced using the following hardening
hazardous electric shock, injury and striking of electric arcs:
process:
___________________________________________________________________
- Remove the torch nozzle and fit the special electrode holder and the coal electrode by
tightening the appropriate knob.
- Do not direct the mouthpiece of the torch towards parts of the body.
- Turn the adjustment switch to position 1 (higher positions may overheat the electrode
- Keep the torch away from the gas bottle.
and the machine).
- Re-fit the contact tip and the nozzle onto the torch
(4b)
.
- Release the pressure from the towing rollers by releasing the spring in order to
- Check that wire feed is regular; set the roller and spindle braking pressure to the
prevent the wire from being dragged along the torch.
minimum possible values making sure that the wire does not slide in the groove and
If only a small area is to be hardened, carry out the operation as if it were spot welding by
when feed is halted the loops of wire are not loosened by excessive reel inertia.
placing the end of the electrode in contact with the metal sheet until this heats up. When
- Cut the end of the wire so that 10-15 mm protrude from the nozzle.
the sheet is sufficiently heated, cool it down using a cloth soaked with water. If a large
- Close the reel compartment door.
area is to be hardened, the electrode should be rotated.
___________________________________________________________________
6. WELDING: DESCRIPTION OF THE PROCEDURE
WARNING:
6.1 PRELIMINARY OPERATIONS
- Insert the earth connector into the (-) socket (for welding machines with a single earth
- The indicator light comes on when there is overheating and cuts off the power supply;
connector).
it will reset automatically within a few minutes, after cooling down.
- Insert the earth connector in the desired (-) quick connector depending on the
___________________________________________________________________
material to be welded (for welding machines with 2 or more earth connectors);
- quick connector (-) with max reactance (
) or position 2-3 for aluminium
7. MAINTENANCE
material and resulting (Al) alloys, copper alloys (CuAl/CuSi).
___________________________________________________________________
- quick connector (-) with min reactance (
) or position 1-2 for stainless steel
(SS), carbon steel and low-alloy (Fe) steel.
- Connect the return cable to the piece being welded.
WARNING! BEFORE CARRYING OUT MAINTENANCE OPERATIONS MAKE
- Turn on and adjust the protective gas using the pressure reducing valve (5-7 l/min)
SURE THE WELDING MACHINE IS SWITCHED OFF AND DISCONNECTED FROM
NOTE:
At the end of the job, remember to turn off the protective gas.
THE MAIN POWER SUPPLY.
- Switch the welder on and set the welding current by means of the rotary switch.
___________________________________________________________________
FIG. G
7.1 ROUTINE MAINTENANCE:
6.2 WELDING (FIG. H)
ROUTINE MAINTENANCE OPERATIONS CAN BE CARRIED OUT BY THE
Once the machine has been prepared for welding by carrying out the operations
OPERATOR.
described above, simply place the earth clamp in contact with the workpiece and press
the torch button, keeping the torch at a safe distance from the workpiece.
7.1.1 Torch
Before carrying out difficult sections of welding, tests should be carried out on scrap
-
Do not put the torch or its cable on hot pieces; this would cause the insulating
pieces. These tests should be carried out using the adjustment knob in order to obtain
materials to melt, making the torch unusable after a very short time;
the best welding possible. If the arc melts in drops and tends to go out, the speed of the
-
Make regular checks on the gas pipe and connector seals;
wire should be increased or the welding current decreased. If, however, the wire hits the
-
Every time the wire reel is changed, blow out the wire-guide hose using dry
piece violently and causes material to be projected, the wire speed should be reduced.
compressed air (max. 5 bar) to make sure it is not damaged;
It should be remembered that in order to obtain the best results, each type of wire is
-
Before using the welding machine, always check the torch terminal parts for wear
suited to a specific current and wire feed speed. Therefore, for difficult sections of
and make sure they are assembled correctly: nozzle, contact pipe, gas diffuser.
welding and welding which requires a great deal of time, wires with different diameters
should be tried so that the most suitable may be chosen.
7.1.2 Wire feeder
- Make frequent checks on the state of wear of the wire feeder rollers, regularly remove
6.3 ALUMINIUM WELDING
the metal dust deposited in the feeder area (rollers and wire-guide infeed and
For aluminium welding, pure ARGON or an ARGON-HELIUM mixture should be used
outfeed).
for shielding. The wire used should have the same characteristics as the material to be
welded. Always use an alloy wire (e.g. aluminium/silicium); never use pure aluminium
7.2 EXTRAORDINARY MAINTENANCE
wire.
Aluminium MIG welding does not present any particular problems. The only difficulty is
in the pulling of the wire for the whole length of the torch, since aluminium is known to
have poor mechanical characteristics. The smaller the diameter of the wire the more this
problem is accentuated.
___________________________________________________________________
This problem can be avoided by making the following changes:
1- Replace the guide hose of the torch with a Teflon guide hose. To withdraw this,
WARNING! BEFORE REMOVING THE WELDING MACHINE PANELS AND
simply loosen the screws at the end of the torch.
WORKING INSIDE THE MACHINE MAKE SURE THE WELDING MACHINE IS
2- Use contact tips for aluminium.
SWITCHED OFF AND DISCONNECTED FROM THE MAIN POWER SUPPLY
3- Replace the wire pulling rollers with those made for aluminium
OUTLET.
4- Replace the steel guide hose for wire feed with a Teflon guide hose.
___________________________________________________________________
The above pieces for aluminium welding are available as optionals.
If checks are made inside the welding machine while it is live, this may cause
serious electric shock due to direct contact with live parts and/or injury due to
6.4 SPOT WELDING (FIG.I)
direct contact with moving parts.
Two overlapping metal sheets can be spot-welded together using a wire system and
- Inspect the welding machine regularly, with a frequency depending on use and the
weld material.
dustiness of the environment, and remove the dust deposited on the transformer,
This model has been specifically designed for the purposes of spot-welding and is
reactance and rectifier using a jet of dry compressed air (max. 10 bar).
equipped with adjustable timer which allows ideal spot-welding time to be set and
- Do not direct the jet of compressed air on the electronic boards; these can be cleaned
therefore the creation of spot-welds which have the same characteristics.
with a very soft brush or suitable solvents.
In order to use the machine for spot-welding, it should be set-up as follows:
- At the same time make sure the electrical connections are tight and check the wiring
- Replace the nozzle of the torch with the nozzle required for spot-welding, which is
for damage to the insulation.
supplied as an accessory. This nozzle is cylindrical-shaped and has holes for gas
- At the end of these operations re-assemble the panels of the welding machine and
escape at the end
screw the fastening screws right down.
- Turn the current adjustment switch to <maximum> position.
- Never, ever carry out welding operations while the welding machine is open.
- Set the wire feed speed at almost maximum speed.
- After having carried out maintenance or repairs, restore the connections and wiring
- Turn the switch to <TIMER> position
as they were before, making sure they do not come into contact with moving parts or
- Set the spot welding time according to the thickness of the metal sheets.
parts that can reach high temperatures. Tie all the wires as they were before, being
To carry out the spot welding, rest the nozzle of the torch on the surface of the first metal
careful to keep the high voltage connections of the primary transformer separate
sheet, then press the torch button in order to start welding: the wire will melt the first
from the low voltage ones of the secondary transformer.
sheet, pass through this sheet and into the second, making a molten wedge between
Use all the original washers and screws when closing the casing.
the two metal sheets.
The button should be pressed until the timer interrupts the welding.
This system allows spot-welding to be carried out which would not normally be possible
with conventional spot-welders, since metal sheets can be joined which do not allow
access to the rear side such as box-type sheets.
This system also makes the operator’s work much easier thanks to the extremely light-
weight torch.
The application limits of this system depend on the width of the first metal sheet; the
second sheet may be extremely thick.
6.5 RIVET WELDING (FIG.L)
This operation is only possible for compact welding machines with an/one earth
connector.
EXTRAORDINARY MAINTENANCE MUST ONLY BE CARRIED OUT BY
TECHNICIANS WHO ARE EXPERT OR QUALIFIED IN THE ELECTRIC-
MECHANICAL FIELD, AND IN FULL RESPECT OF THE IEC/EN 60974-4
TECHNICAL DIRECTIVE.
Summary of Contents for MASTERMIG 220/2
Page 83: ...83 FIG D FIG E 230V 220V 240V 400V 380V 415V...
Page 84: ...84 0 8 0 8 0 8 0 6 0 6 4 3 a b 2 1 a b a b c 200mm kg5 300mm kg15 FIG F...
Page 85: ...85 FIG F1 200mm 300mm 1 a a b b 4 2 a b c 3 0 8 0 8 0 6 0 6...
Page 86: ...86 FIG F2 200mm 300mm 1 a a b b 4 2 a b c 3 0 8 0 8 0 6 0 6 MAX 5kg MAX 15kg...