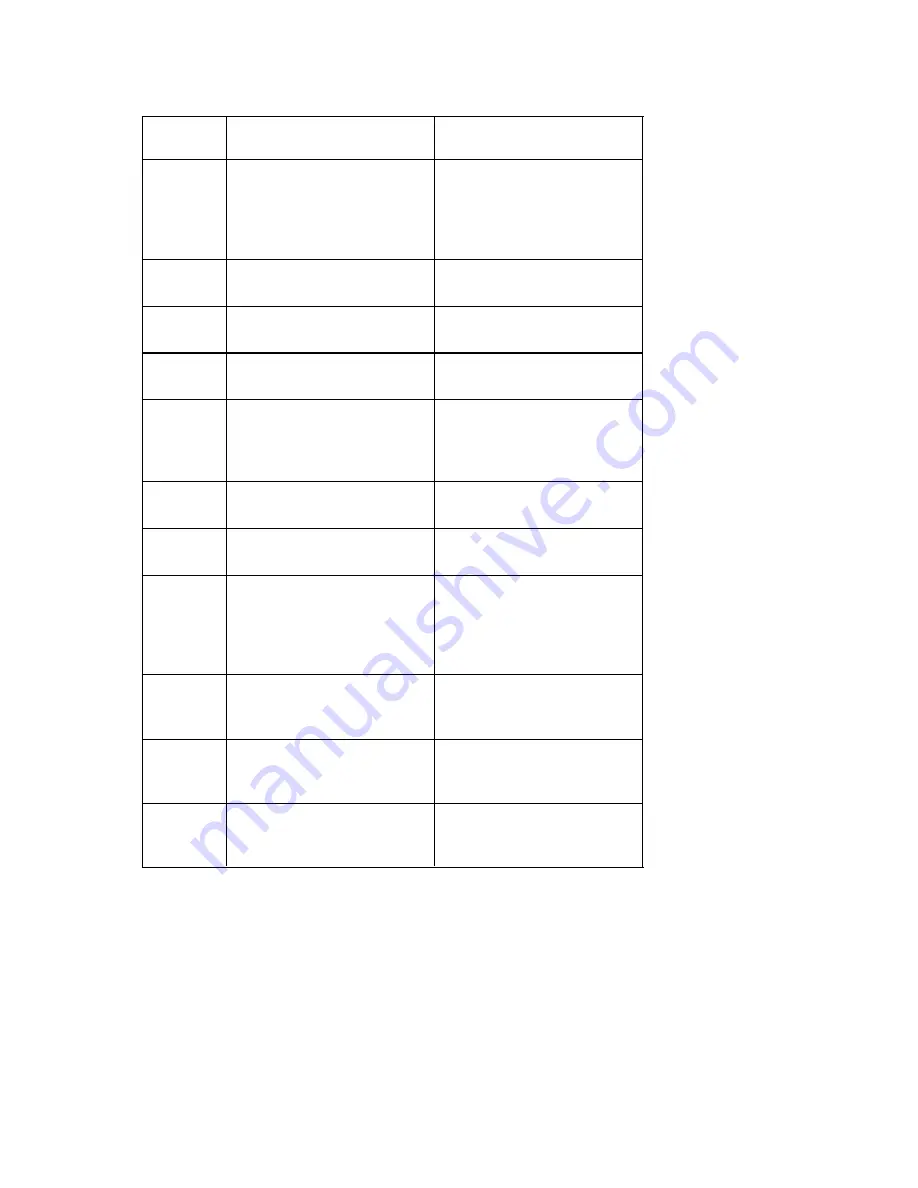
12.93
12 Functional Descriptions
12.18.13 Start-up
12.18.13.2 Full start-up procedure
Step
Action
Important information
1
Define position control
sampling time
Following drive and
associated leading drives
must generally have the
same position control
sampling times.
2
Set drift compensation
(applies only to analog drives)
Deactivate feedforward
control and link beforehand
3
Carry out general optimization
of axes and spindles
Servo gain factor must be
correct (following error check)
4
Set feedforward control
Check effect of feedforward
control on the following error
5
Match dynamic response of
individual drives
With setpoint links, the
leading and following drives
must have the same dynamic
response (rise time).
6
Set the required machine
data
Initial configuration must be
enabled
7
Optimize the compensatory
controller
Switch on link and FD overlay
8
Calculate the time constants
of the parallel model
Check synchronism error in
service display; deactivate
compensatory controller;
feedforward control must be
fully set
9
Define the GI monitoring
tolerances according to
manufacturer's data
Check in service display (indi-
vidual spindle/individual axis)
Synchronism error
10
Check the GI programming
functions
Configuration;
Activate/deactivate link;
on-the-fly synchronization
11
Set the interlocks
Interlocks, e.g. set
reconfiguration etc. (NC MD
bits)
© Siemens AG 1992 All Rights Reserved 6FC5197- AA50
12–157
SINUMERIK 840C (IA)
Summary of Contents for SIMODRIVE 611-D
Page 2: ......