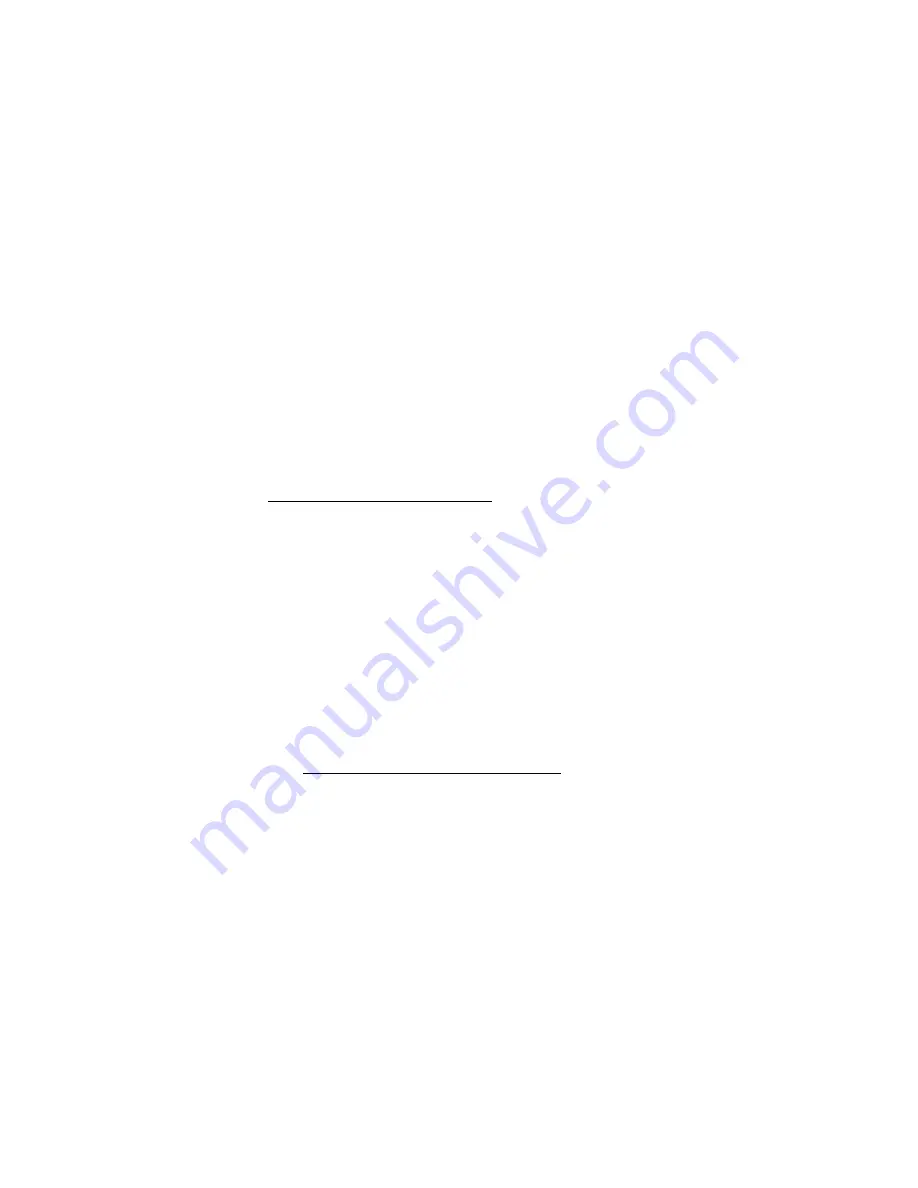
08.96
12 Functional Descriptions
12.33.1 Introduction
12.33.1.1
Fourier analysis
The integrated Fourier analysis function provides you with a particularly effective tool for
optimizing the speed controller. It allows you to assess the speed control settings and the
mechanical properties of the machine.
To reach the Fourier analysis (frequency response method), please select Startup Drive
servo startup Startup function .
The frequency response method supplies exact and reproducible results even with very low
test signal amplitudes. You can adapt the measurement parameters to the individual
application.
The results of the Fourier analysis are displayed in a Bode diagram. A Bode diagram consists
of two graphs, i.e. the amplitude response curve and the phase response curve.
The phase is at 0 in the lower frequency range. It rotates to negative phase angles as the
frequency increases. If the phase angle exceeds I180°I, the graph representation is reversed,
i.e. it jumps from –180° to180° or from 180° to–180°.
12.33.1.2
Measurement range (bandwidth), measurement time
The bandwidth is calculated as follows on the SINUMERIK 840C/611D:
1
Max. bandwidth =
2 x speed controller clock cycle
The bandwidths are as follows depending on the speed controller clock cycle:
•
Clock cycle= 62.5µs
Bandwidth = 8 kHz.
•
Clock cycle= 125µs
Bandwidth = 4 kHz.
•
Clock cycle= 250µs
Bandwidth = 2 kHz.
•
Clock cycle= 500µs
Bandwidth = 1 kHz.
Owing to the short measurement times, traversing distances of a few mm are sufficient for the
required response measurement. The measurement time is calculated as follows:
512 x No. of averaging operations
Measurement time[s] =
+ settling time
Bandwidth [Hz]
The measurement time is 6.5 seconds with 20 averaging operations. With an offset of 5
rev/min, a traversing range of less than 0.55 revolutions is required for the measurement.
© Siemens AG 1992 All Rights Reserved 6FC5197- AA50
12–335
SINUMERIK 840C (IA)
Summary of Contents for SIMODRIVE 611-D
Page 2: ......