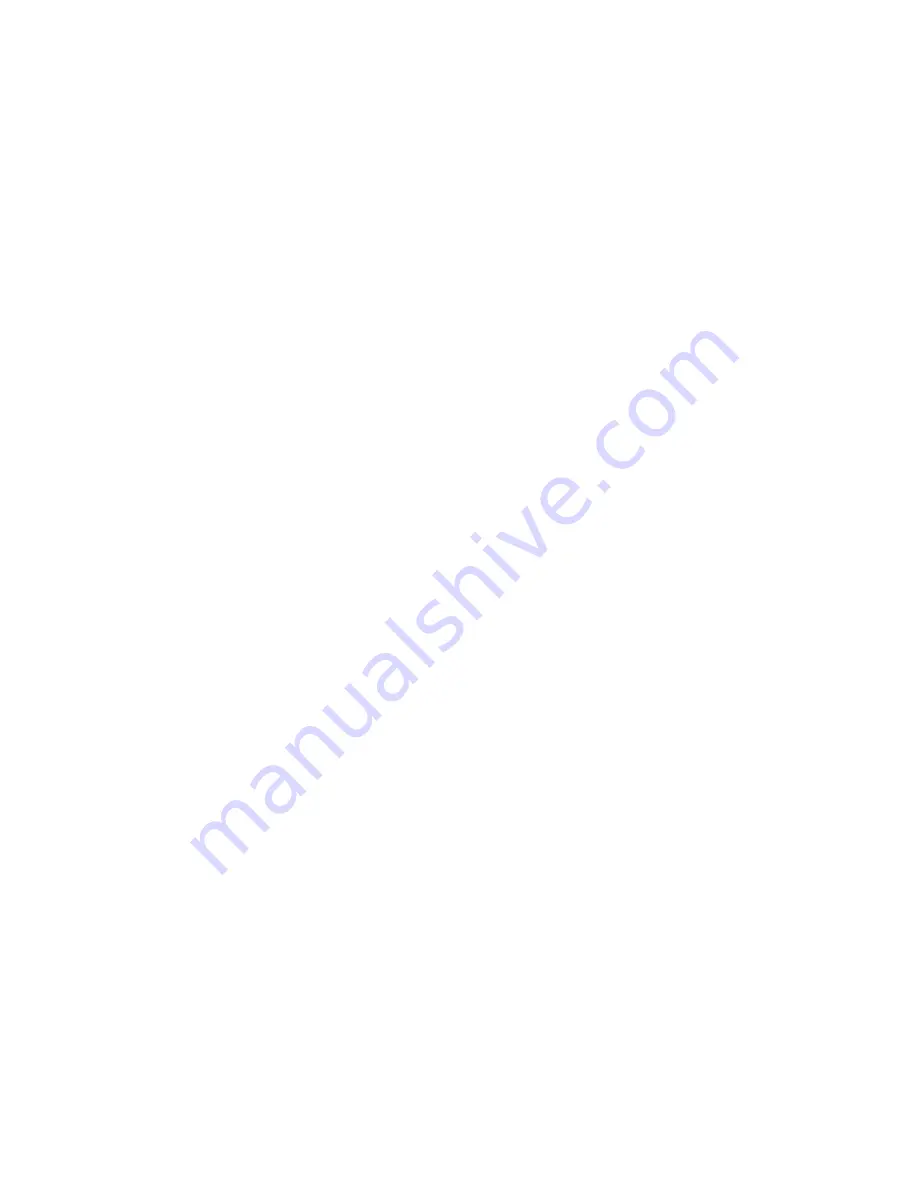
04.96
12 Functional Descriptions
12.25.4 Memory configuration on control power-up
DRAM:
704 KB
for part program memory
64 KB
for IKA data (corresponds to 4000 IKA points)
256 KB
for UMS
approx. 40 KB
for block buffers for one channel (corresponds to 23 block buffers per
channel)
0 KB
for buffering of measured values (new "Extended measurement"
function)
approx.100 KB
for extended overstore in 2 channels
0 KB
for drive SW (MSD)
0 KB
for drive SW (FDD)
0 KB
for additional real axes
1364 KB
=
Total memory requirements
SRAM:
19 KB
for R parameters (corresponds to 700 channel-spec. and 600 central R
parameters)
32 KB
for TO data (corresponds to 819 tools with 10 parameters)
51 KB
=
Total memory requirements
The values entered in the Siemens NCMEMCFG file guarantee that the control starts during
the initial start-up phase and can be operated.
If a 386 NC-CPU module is replaced by a 486 SX NC-CPU module, it is advisable to use the
same memory configuration in the new module.
The initial start-up procedure is as follows:
The rotary switch on the CSB module is set to start-up position and the control switched on.
The control reaches cyclic operation within the start-up mode. The data contained in file
NCMEMCFG are transferred to the NC-MD during power-up.
The currently valid memory configuration can now be examined in an MDD display. This
display is selected by means of softkeys Data area/Start-up/Machine data/NC-MD/ETC
key/Memory configuration. The user data can be displayed in the appropriate memory areas
by means of softkeys DRAM data or SRAM data. "Online" data can be read, but not written.
If an attempt is made to change online data, the message "No input authorization" is output.
© Siemens AG 1992 All Rights Reserved 6FC5197- AA50
12–261
SINUMERIK 840C (IA)
Summary of Contents for SIMODRIVE 611-D
Page 2: ......