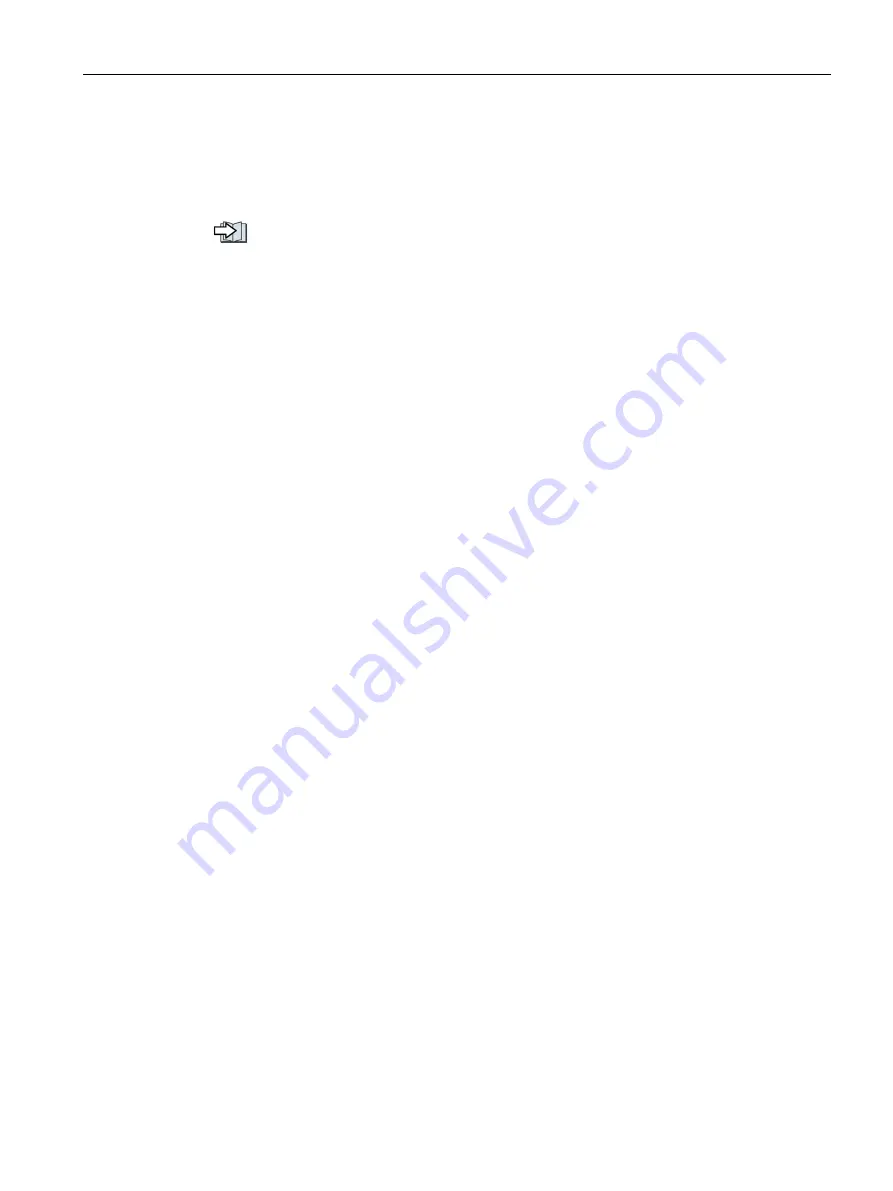
Advanced commissioning
7.11 Motor control
SIMATIC ET 200pro FC-2 converter
Operating Instructions, 04/2018, FW V4.7 SP10, A5E34257324B AF
157
frequency also results in a higher motor slip, which is proportional to the accelerating torque.
I
q
and I
d
controllers keep the motor flux constant using the output voltage, and adjust the
matching current component I
q
in the motor.
All of the function diagrams 6020 ff. for vector control are provided in the List Manual.
Manuals for your inverter (Page 272)
7.11.2.2
Select motor control
Vector control is already preset
To achieve a good controller response, you must adapt the elements marked in gray in the
figure in the overview diagram above. If you selected vector control as control mode in the
basic commissioning, you will have already set the following:
●
The maximum speed for your application.
●
The motor and current model: If the motor data in the inverter correspond to the motor
data on the rating plate, then the motor and current model in the inverter are correct and
the vector control can operate satisfactorily.
●
The inverter calculates the torque limits matching the current limit that you have set for
the basic commissioning.
Regardless of it, you can also set additional positive and negative torque limits or limit the
power of the motor.
●
The inverter has a preset speed controller with self-optimization (rotating measurement).
If you want to continue to optimize this setting, follow the instructions further down in this
chapter.
Select encoderless vector control
Set p1300 = 20.
7.11.2.3
Optimizing the speed controller
Optimum control response - post optimization not required
Preconditions for assessing the controller response:
●
The moment of inertia of the load is constant and does not depend on the speed
●
The inverter does not reach the set torque limits during acceleration
●
You operate the motor in the range 40 % … 60 % of its rated speed