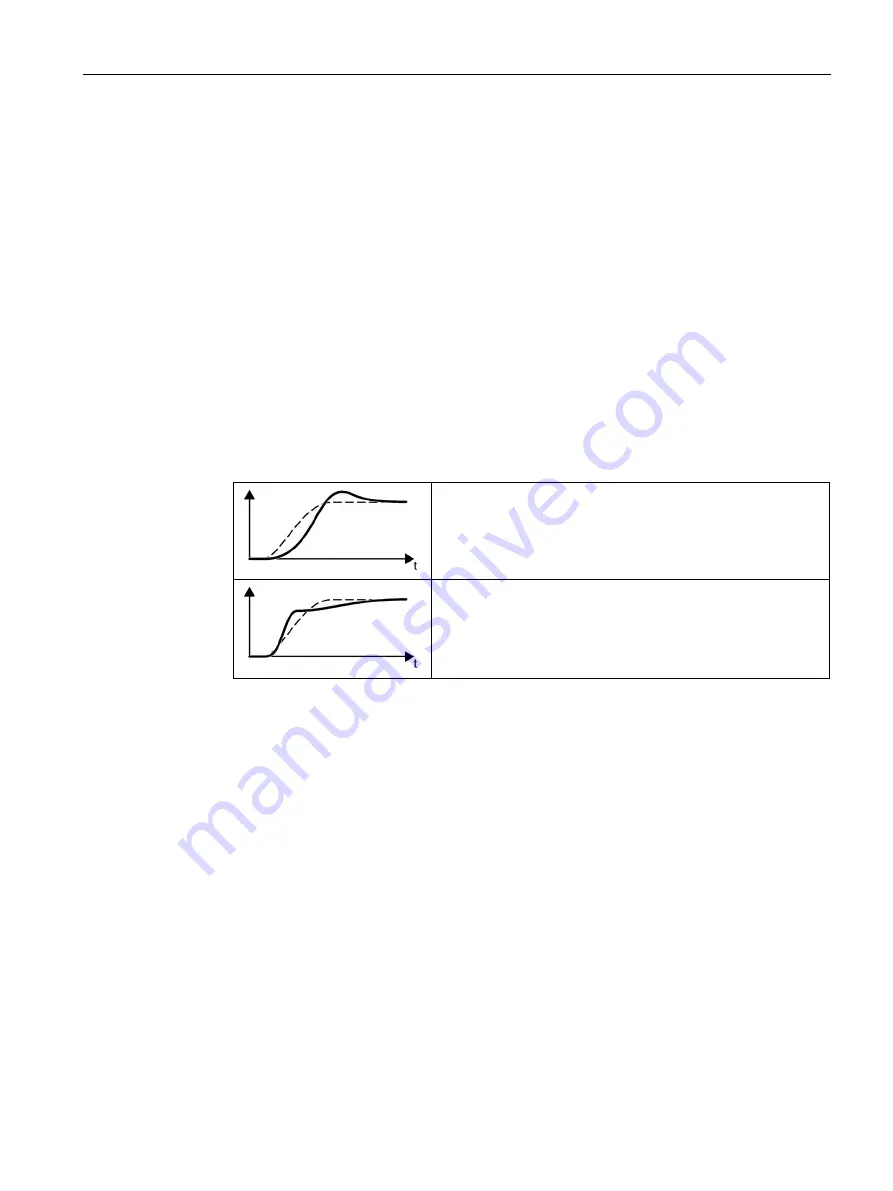
Advanced commissioning
7.11 Motor control
SIMATIC ET 200pro FC-2 converter
Operating Instructions, 04/2018, FW V4.7 SP10, A5E34257324B AF
159
●
The inverter requires 10 % … 50 % of the rated torque to accelerate.
When necessary, adapt the ramp-up and ramp-down times of the ramp-function
generator (p1120 and p1121).
●
You have prepared the trace function in STARTER to be able to record the speed
setpoint and actual value.
Procedure
1.
Switch on the motor.
2.
Enter a speed setpoint of approximately 40 % of the rated speed.
3.
Wait until the actual speed has stabilized.
4.
Increase the setpoint up to a maximum of 60 % of the rated speed.
5.
Monitor the associated characteristic of the setpoint and actual speed.
6.
Optimize the controller by adapting the ratio of the moments of inertia of the load and
motor (p0342):
Initially, the speed actual value follows the speed setpoint with
some delay, and then overshoots the speed setpoint.
•
Increase p0342
Initially, the speed actual value increases faster than the speed
setpoint. The setpoint passes the actual value before reaching
its final value. Finally, the actual value approaches the setpoint
without any overshoot.
•
Reduce p0342
7.
Switch off the motor.
8.
Set p0340 = 4. The inverter again calculates the speed controller parameters.
9.
Switch on the motor.
10.Over the complete speed range check as to whether the speed control operates
satisfactorily with the optimized settings.
You have optimized the speed controller.
❒
When necessary, set the ramp-up and ramp-down times of the ramp-function generator
(p1120 and p1121) back to the value before optimization.
7.11.2.4
Friction characteristic
Function
In many applications, e.g. applications with geared motors or belt conveyors, the frictional
torque of the load is not negligible.