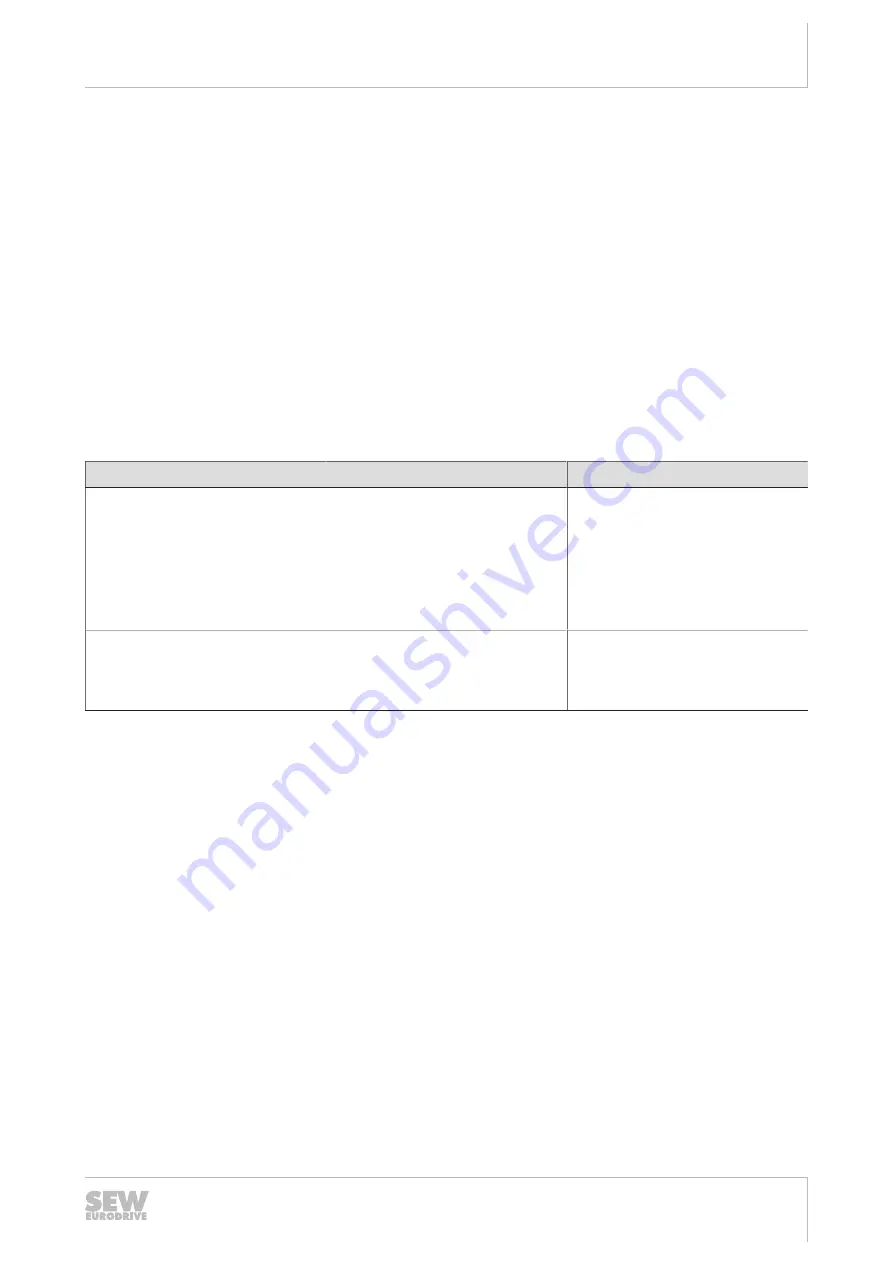
11
Inspection and maintenance
Inspection and maintenance intervals
Operating Instructions – Compact Extra-Low Voltage Drives
79
The following factors may lead to shorter inspection and maintenance intervals:
• Number of real emergency switching off braking operations
• Particularly high number of cycles with high motor acceleration
• Especially high cyclic duration factor at high speed
• Changing direction of rotation (reversing operation)
• Vertical mounting positions and pivoted mounting positions
• High mass moments of inertia due to the motion of the drive, e.g. in mobile drives
or drives subject to high impact and vibration load
• Application-related retrodriving torques or torsional vibrations
• External environmental influences, such as moisture, high degree of UV exposure,
low ambient temperatures.
11.3.1
Motor
The following table shows the inspection intervals for the motor:
Time interval
Activity
Design
Every 3000 operating hours, at
least every 6 months
Check for possible bearing dam-
age in the event of running noise.
In the event of bearing damage,
have the bearing replaced by
SEW‑EURODRIVE
Service or
specialists trained by
SEW‑EURODRIVE
.
• Specialists at customer site
• Specialists trained by
SEW‑EURODRIVE
•
SEW‑EURODRIVE
Service
Recommendation: Every
10 000 operating hours
Have the motor inspected by
SEW‑EURODRIVE
Service or
specialists trained by
SEW‑EURODRIVE
.
• Specialists trained by
SEW‑EURODRIVE
•
SEW‑EURODRIVE
Service
11.3.2
Brake
• The brake does not require any maintenance.
• You cannot measure the working air gap directly, since the brake is integrated in
the motor.
• If the permissible total braking work W
insp
that was determined during configuration
has been reached, you must have the drive replaced. Contact
SEW‑EURODRIVE
.
26718014/EN – 11/2020