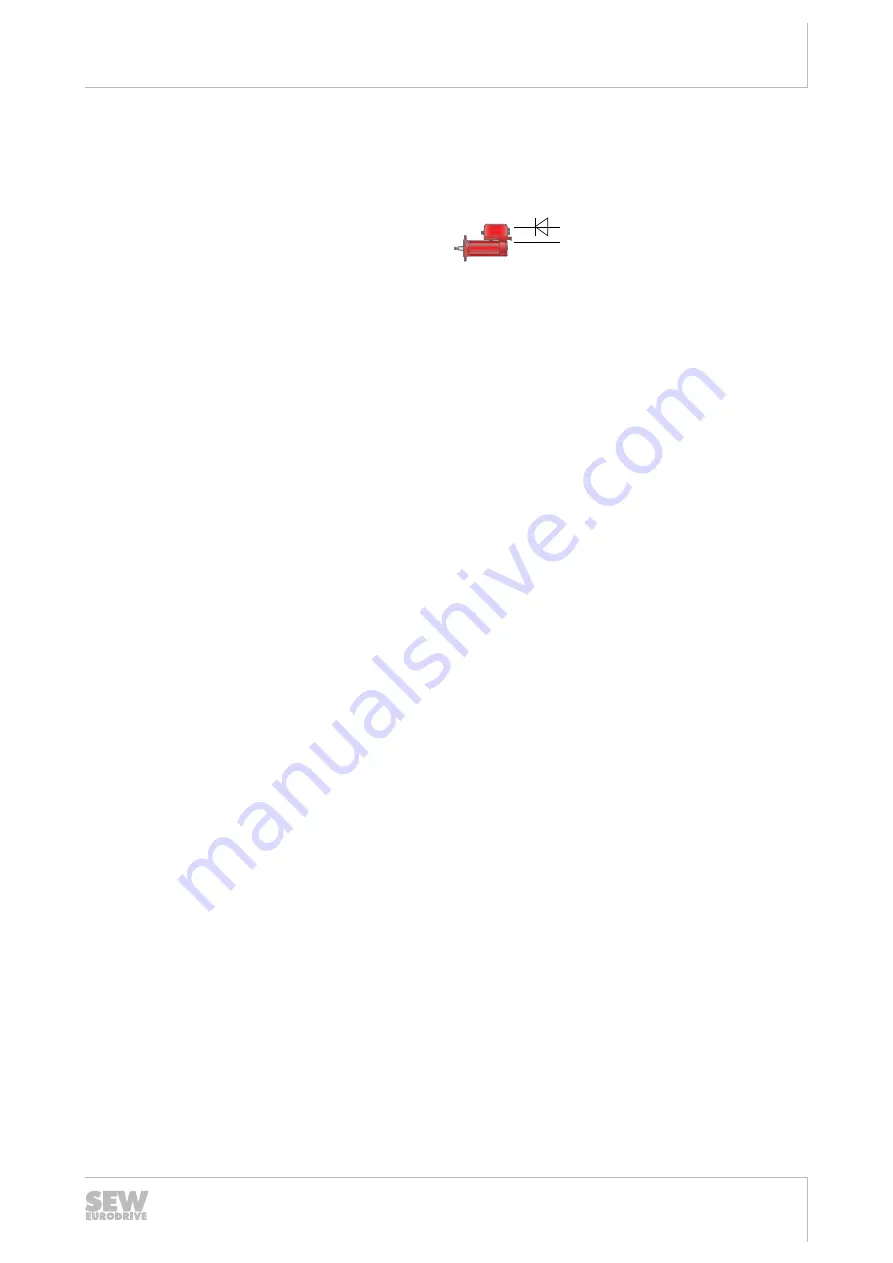
5
Electrical installation
CAN bus
Operating Instructions – CMP ELVCD
27
To avoid the possible regenerative voltage rise at the output of the 48 V power supply
unit and the resulting switch-off, you may install a diode. Dimension the diode accord-
ing to the currents and the voltage of the 48 V supply. Install the diode in the C 48 V
supply as shown in the following figure:
ELVCD
GND
+ZK
20411863691
Industrial switched-mode power supplies have back-feeding protection. Back-feeding
protection specifies how high the voltage may be at the output during regenerative
operation of the ELVCD drive without the power supply being switched off or dam-
aged. Please observe the information on the power supply data sheet.
If the voltage value of the back-feeding protection is higher than the switch-on
threshold of the brake chopper, a diode does not need to be installed.
During braking operation of the ELVCD drive, the energy that is fed back is dissipated
in the integrated braking resistor. This leads to additional heating of the ELVCD in-
verter, which must be taken into consideration in the thermal design of the drive (de-
rating, see chapter "Thermal characteristic curves" (→
99)).
Due to the use of an external brake chopper with a braking resistor, the braking en-
ergy is no longer dissipated in the ELVCD inverter. Appropriate derating is therefore
not required. Please pay attention to correct electrical installation (see chapter "Install-
ation topology (example)" (→
24)). Please pay attention to the following information
when setting the switching thresholds of the external brake chopper:
•
The switch-on threshold of the external brake chopper must be less than the
switch-off threshold of the internal brake chopper.
•
The switch-off threshold of the external brake chopper must be more than the
voltage of the DC 48 V supply circuit.
•
If the switch-on threshold of the external brake chopper is less than the back-feed-
ing protection of the switched-mode power supply, no diode is required.
5.6
CAN bus
5.6.1
Bus termination
In order to avoid disruptions in the bus system due to reflections, each system bus
must be terminated with bus terminating resistors at the first and last physical stations.
Terminating the
first system bus
station
Use the MOVI‑PLC
®
controller as the first system bus station.
•
If the ELVCD drive is actuated via CAN 2, connect a terminating resistor of 120 Ω
at the beginning of system bus CAN 2 between pin X32:2 and pin X32:3.
•
If the ELVCD drive is actuated via CAN 1, connect a terminating resistor of 120 Ω
at the beginning of system bus CAN 1 between pin X33:2 and pin X33:3.
Jumpering refer-
ence potential
No potential shift should occur between the stations of system bus CAN 2.
No potential shift may occur between the stations of system bus CAN 1.
Suitable measures must be taken to ensure that no potential shift occurs between the
system bus stations. For example, jumper the CAN_GND reference potential of the
stations with a separate cable.
22759468/EN – 11/2017