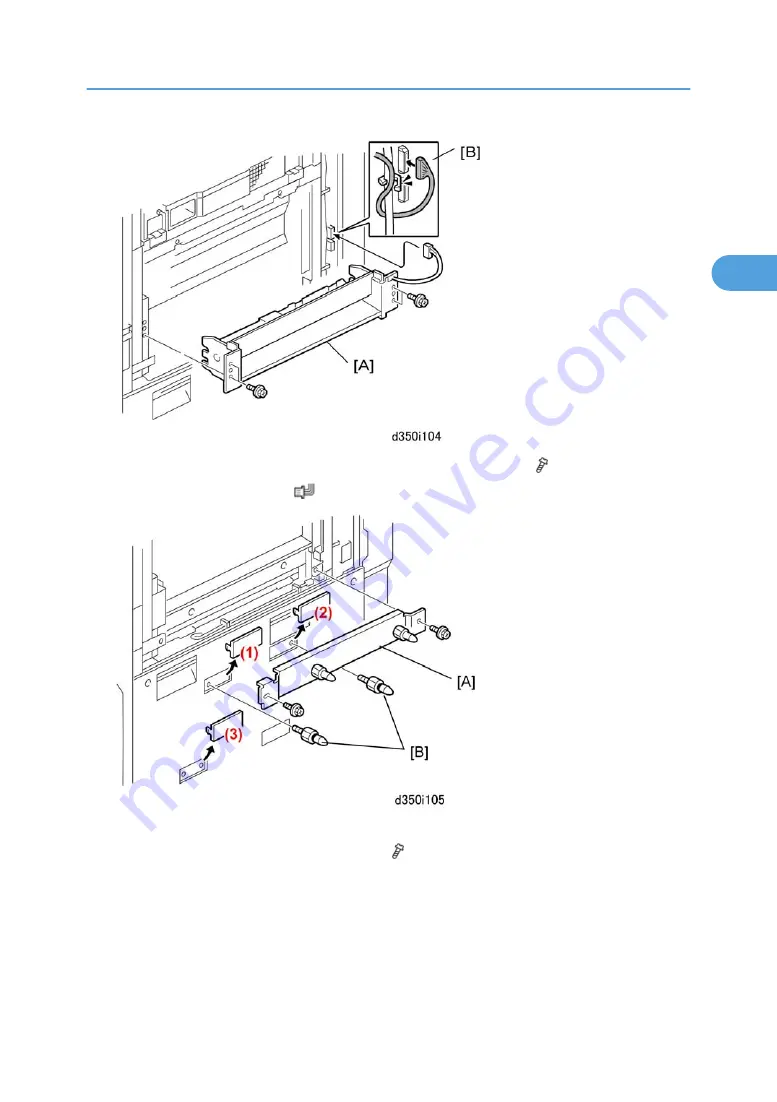
9. Use the screws removed with the bypass tray to attach the relay unit [A] ( x4).
10. Connect the relay harness [B] (
x1).
11. Remove knockouts: (1), (2), (3).
12. Attached the stay [A] with the provided screws ( x2).
13. Attach the joint connection pins [B] (x2).
14. Re-attach the right upper cover.
LCIT RT4000 (D350)
137
2
Summary of Contents for V-C3 D081
Page 1: ...Model V C3 Machine Code D081 D082 Field Service Manual 30 November 2009...
Page 2: ......
Page 46: ...44...
Page 52: ...Overview Main Machine 1 Transport Belt ARDF 18 Grip Roller 1 Product Information 50 1...
Page 54: ...1 Product Information 52 1...
Page 135: ...19 Input 5 for B4 SEF or 6 for 8 5 x 14 SEF LG Size Tray Type 1075 B474 133 2...
Page 283: ...PM Tables See Appendices for the following information PM Tables PM Tables 281 3...
Page 284: ...3 Preventive Maintenance 282 3...
Page 326: ...4 Replacement and Adjustments 324 4...
Page 455: ...Left Lower Cover Removed AC Drive Board Boards 453 4...
Page 460: ...PFB 1 Remove the PFB A x14 x6 4 Replacement and Adjustments 458 4...
Page 461: ...HVPS 1 Remove the HVPS x4 x8 Charge Roller Power Pack Boards 459 4...
Page 463: ...DRB 1 Remove the DRB x14 x5 Boards 461 4...
Page 464: ...DTMB 1 Remove the DTMB x7 x4 4 Replacement and Adjustments 462 4...
Page 504: ...4 Remove the ITB drive motor A x4 x1 4 Replacement and Adjustments 502 4...
Page 508: ...2 Remove A Air filters B Ozone filter 4 Replacement and Adjustments 506 4...
Page 528: ...5 System Maintenance 526 5...
Page 568: ...Service Call Tables See Appendices for Service Call Tables information 6 Troubleshooting 566 6...
Page 572: ...Total 32 20 7 Energy Saving 570 7...
Page 575: ...6 Duplex with combine mode SP 8421 005 pages Paper Save 573 7...
Page 576: ...7 Energy Saving 574 7...
Page 577: ...Model V C3 Machine Code D081 082 Appendices 25 December 2009...
Page 578: ......
Page 647: ...3 Apply a thin layer of Grease KS660B around the surface at B as shown Lubrication Points 69 2...
Page 648: ...2 Appendix PM Tables 70 2...
Page 958: ...25 SDK J Application Info 4 Appendix Service Program Mode Tables 380 4...
Page 1092: ...4 Appendix Service Program Mode Tables 514 4...