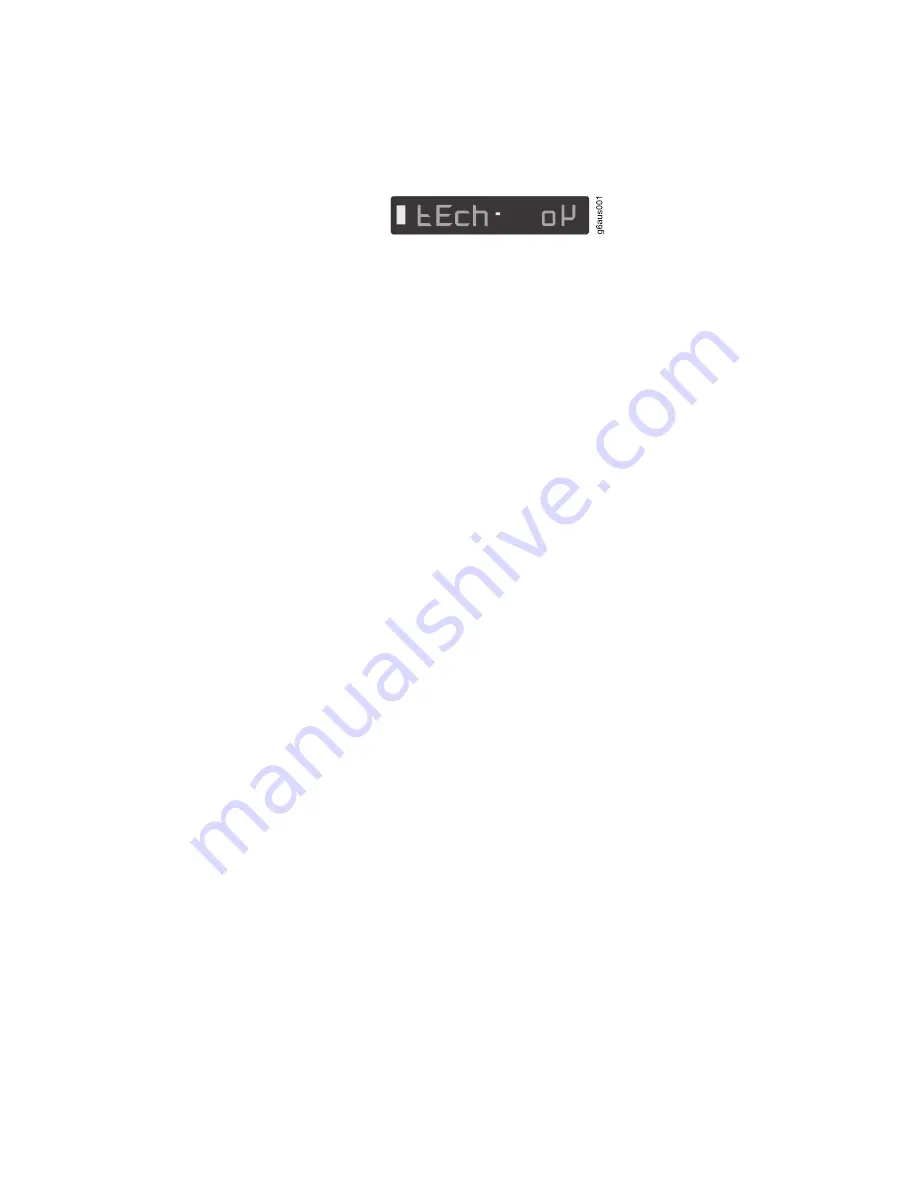
a.
Use the
Forms Feed Reverse
button (
3
) until the sensor is over an area of
the form without any printing and the brightness reading is at it's highest
point.
b.
Press and hold the orange
UP
button until the displayed numbers start to
blink, then release the
UP
button.
c.
This output
means you have successfully
adjusted the sensor. Any other displayed characters means you need to
repeat the adjustment process.
6.
Select
RUN
by moving the
Set
-
Run
switch (
7
) to the right. The display will
stop blinking and the UFC sensor is ready to use.
7.
Press the
Toner Mark
button. The forms will move under the upper mark
sensor so that the printed mark is registered.
8.
Exit diagnostic mode at the operator panel.
What to do next
Related tasks
“Adjusting the Universal Forms Control (UFC) sensor in look up mode”
Follow these steps to set the UFC sensor to read registration or side verify marks
from below the forms (same side printing only). This function is only available in
Administrator or Service mode.
“Selecting the Universal Forms Control (UFC) sensors” on page 198
Use these instructions to select which UFC sensor you want to adjust. Choosing
the lower mark sensor reads the front of the forms; choosing the upper mark
sensor reads the back of the forms. This function is only available in Administrator
or Service mode.
Related reference
“Diagnostics - Testing and adjusting the Universal Forms Control (UFC) sensor” on
page 371
Service and administrators use the Diagnostics - Adjusting the universal forms
control module to run diagnostic tests to identify problems with the Universal
Forms Control (UFC) sensor. Instructions are displayed about how to execute the
selected test.
Adjusting the Universal Forms Control (UFC) sensor in look up
mode
Follow these steps to set the UFC sensor to read registration or side verify marks
from below the forms (same side printing only). This function is only available in
Administrator or Service mode.
Before you begin
Before adjusting the UFC sensor, follow the steps in “Selecting the Universal Forms
Control (UFC) sensors” on page 198.
Note:
The Side 2 Verify with the Look Up sensor is only available in same side
printing mode. Duplex print with Side 2 Verify requires the Look Down sensor be
used.
Chapter 5. Working with forms
203
Summary of Contents for InfoPrint 4100 TD3
Page 1: ...Operating the InfoPrint 4100 InfoPrint 4100 Models TS2 TD3 4 TS3 and TD5 6 S550 1298 02...
Page 2: ......
Page 3: ...Operating the InfoPrint 4100 InfoPrint 4100 Models TS2 TD3 4 TS3 and TD5 6 S550 1298 02...
Page 8: ...vi Operating the InfoPrint 4100...
Page 12: ...x Operating the InfoPrint 4100...
Page 14: ...xii Operating the InfoPrint 4100...
Page 60: ...46 Operating the InfoPrint 4100...
Page 268: ...254 Operating the InfoPrint 4100...
Page 360: ...346 Operating the InfoPrint 4100...
Page 407: ...Administrator panel Chapter 8 Help topics for the InfoPrint 4100 operator console 393...
Page 408: ...394 Operating the InfoPrint 4100...
Page 461: ......
Page 462: ...Program Number 5765 G79 5765 G74 Printed in USA S550 1298 02...