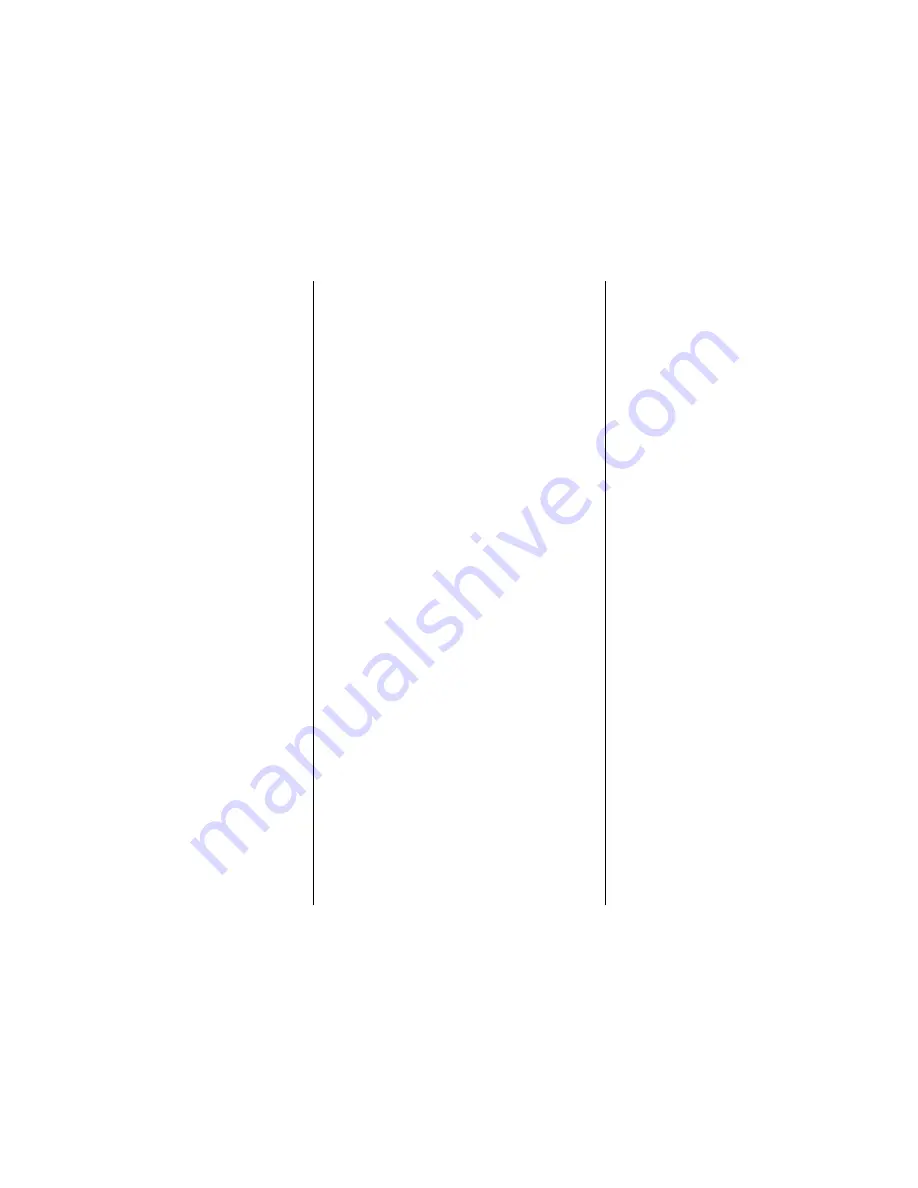
6
About the EPP Airframe
Your EPP parts are 1.3 lbs/cu.ft., so that
makes them light weight yet still posses
enough structural integrity to take a
great deal of abuse without breaking.
If you ever break a foam component you
can use a variety of adhesives to fix a
break. Use epoxy or expanding
polyurethane glues, like Gorilla Glue®,
in areas you want to make stiffer. Use
flexible glues like the polyurethane
sealant used to attach the skins or
products like Zap-A-Gap™, Goop™, or
silicone-based adhesive to keep a repair
area capable of flexing. You can even
use regular CA glue as it will not harm
EPP. CA glues vary so testing is
suggested.
Your airfoil components come with their
foam saddles. After assembly, you can
use this extra foam for repairs (to
replace heavily damaged sections of the
airframe), transportation cushioning, etc.
Unlike expanded polystyrene
(Styrofoam™), EPP is not adversely
affected by gasoline or glo fuels,
however, due to its cellular structure, the
foam could absorb liquids so those
areas exposed to fluids, (under the
lower cowl, nose wheel cavity and fuel
tank area) should be coated with a thin
coat of epoxy to act as a barrier.
In the back of this manual there is an
inventory of all provided EPP
components. Please check that your kit
includes these parts before you begin
assembly.
About the Polycarbonate Skins
This material is amazingly durable
compared to other plastics used in the
modeling industry. Here are some facts
about polycarbonate and our use of this
material as model aircraft skin.
Do not apply solvents like M.E.K.,
acetone, turpentine or toluene to the
skins as this will cause them to crack.
To clean bare polycarbonate use
products like mineral spirits or mild
cleaning agents like Windex. To learn
more about polycarbonate’s
compatibility with other chemicals go to:
http://www.sheffieldplastics.com/web_do
cs/BRO002.pdf
Applying paint to the skins will protect
the polycarbonate from fuel residue, so
only run an installed engine on a model
with primer or paint. As with most
plastics, polycarbonate could tear if a
crack is present so radius corners of cut
lines, where possible.
We form the skins using both male and
female vacuum form molds, therefore,
some skins may have the green
protective film on the outside surface
and the clear protective film on the
inside. Other skin parts may be the
opposite. Some skins may not have film
on one side and some skins may have
no film at all. Your parts may look
different from parts shown in this
manual.
Throughout the manual we will direct
you to trim the skins to fit a specific
airframe part. We will use primarily two
terms; rough trim and finish trim. Rough
trim is basically cutting off the remaining
flashing – the part of the plastic that is
not part of the formed skin detail,
whereas finish trimming will involve
measurements, trial fitting, marking and
cutting to final shape. Since you won’t
initially know where a certain part needs
to be finished trimmed, your rough trims
should maximize the material that can
be distinguishable as the part’s skin. If
you make a mistake and remove too
much material you could use scrap
plastic to make a scale-like panel or call
us and we can get a replacement skin to
you quickly. We suggest you retain all
cut off plastic pieces (except the very
small remnants) so you can use the
excess as scrap when needed during
the assembly process or a future crash
repair.
The skins are primarily .010” thick. This
is good from a weight standpoint.
Additionally, the use of this thin material
as skin will produce the slightly wavy
appearance similar to the aluminum
surface on a full-size aircraft. The
model’s surfaces will not be perfectly
smooth. Smooth surfaces are a
condition we have come to expect in
model aviation, however such conditions
rarely occur in full-scale and certainly
Summary of Contents for T-34C TURBO MENTOR
Page 190: ...191 This Page Intentionally Left Blank ...
Page 191: ...192 Fin Rudder Template ...
Page 192: ...193 This Page Intentionally Left Blank ...
Page 193: ...194 ...
Page 194: ...195 This Page Intentionally Left Blank ...
Page 195: ...196 Laser Cut Parts Diagram ...