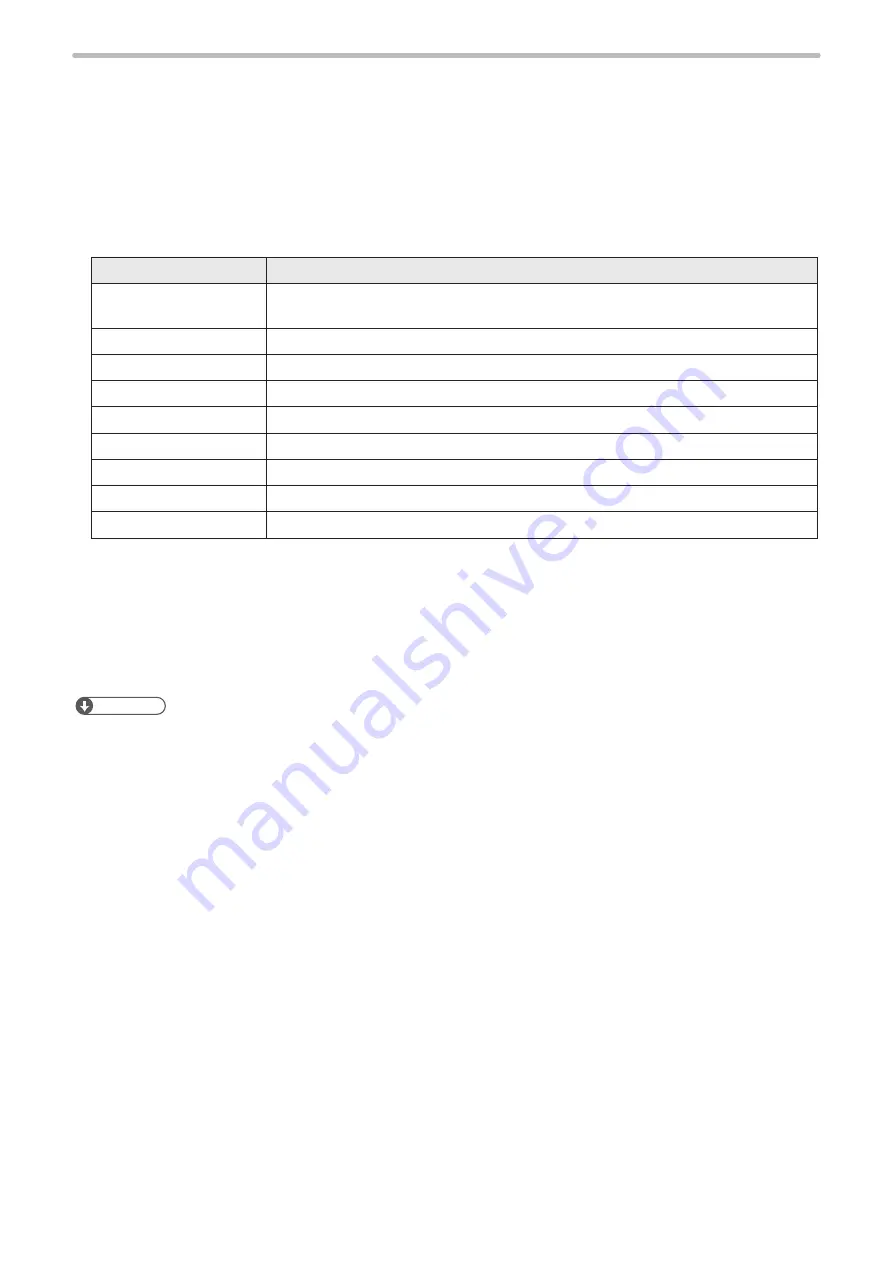
63
2-6-4 Connection of PC (Laser marker NAVI smart)
This product is set and operated with the PC with the PC configuration software “Laser Marker NAVI smart” installed and
the laser marker connected.
Installation of laser marker NAVI smart
• “Laser Marker Smart Utility” that contains the software including Laser Marker NAVI smart and PDF manuals is available
from our Internet website. Refer to “1-2-4 Download software and manual” (P.25).
• Install the Laser Marker NAVI smart in the following environment. For details about installation, please refer to the “Laser
Marker NAVI smart Operation Manual”.
Item
Installation requirements
OS *1
Microsoft
®
Windows
®
11 Pro 64bit
Microsoft
®
Windows
®
10 Pro 32bit, 64bit
Free area on hard disk
512MB or more
USB port *2
USB 2.0
LAN *3
10BASE-T or 100BASE-TX
Memory capacity
2GB or more
CPU
Equivalent to or higher than Intel Core i3
Display resolution
1366 x 768 pixels or above
Display size
10.6 inch or above
Others
Pointing device such as a mouse, character input device such as a keyboard
*1 : OS versions of which Microsoft has ended support are excluded. The CPU type, memory capacity, hard-
disk space, and display function required to operate each OS should be provided in accordance with the
recommendation of Microsoft. Laser Marker NAVI smart can be installed in English, German, Simplified Chinese
or Japanese. It is preferred that the OS language corresponds to the installation language. If the OS language is
other than these supported languages, install Laser Marker NAVI smart in English.
*2 : We do not guarantee the connection of all PC and laser marker.
*3 : Specifications to be observed for Ethernet connection.
ンㄆㄇㄆㄓㄆㄏㄆ
• If PC goes into “Sleep” when the laser marker and PC are connected online, the online connection between them is
disabled.
If PC goes into sleep state in the REMOTE mode or RUN mode, the PC is disconnected but the operation state of the
laser marker (REMOTE mode or RUN mode state) are maintained.
• To maintain the online connection, release the sleep setting of the PC.
ME-LPRH-SM-3
Summary of Contents for LP-RH Series
Page 19: ...1 Product Overview ME LPRH SM 3...
Page 42: ...2 Laser Marker Installation ME LPRH SM 3...
Page 68: ...3 Operation Method ME LPRH SM 3...
Page 90: ...4 External Control Using I O ME LPRH SM 3...
Page 138: ...5 External Control by Communication Commands ME LPRH SM 3...
Page 147: ...6 Link Control with External Devices ME LPRH SM 3...
Page 172: ...7 Maintenance ME LPRH SM 3...
Page 201: ...Troubleshooting ME LPRH SM 3...
Page 236: ...Index ME LPRH SM 3...
Page 239: ......