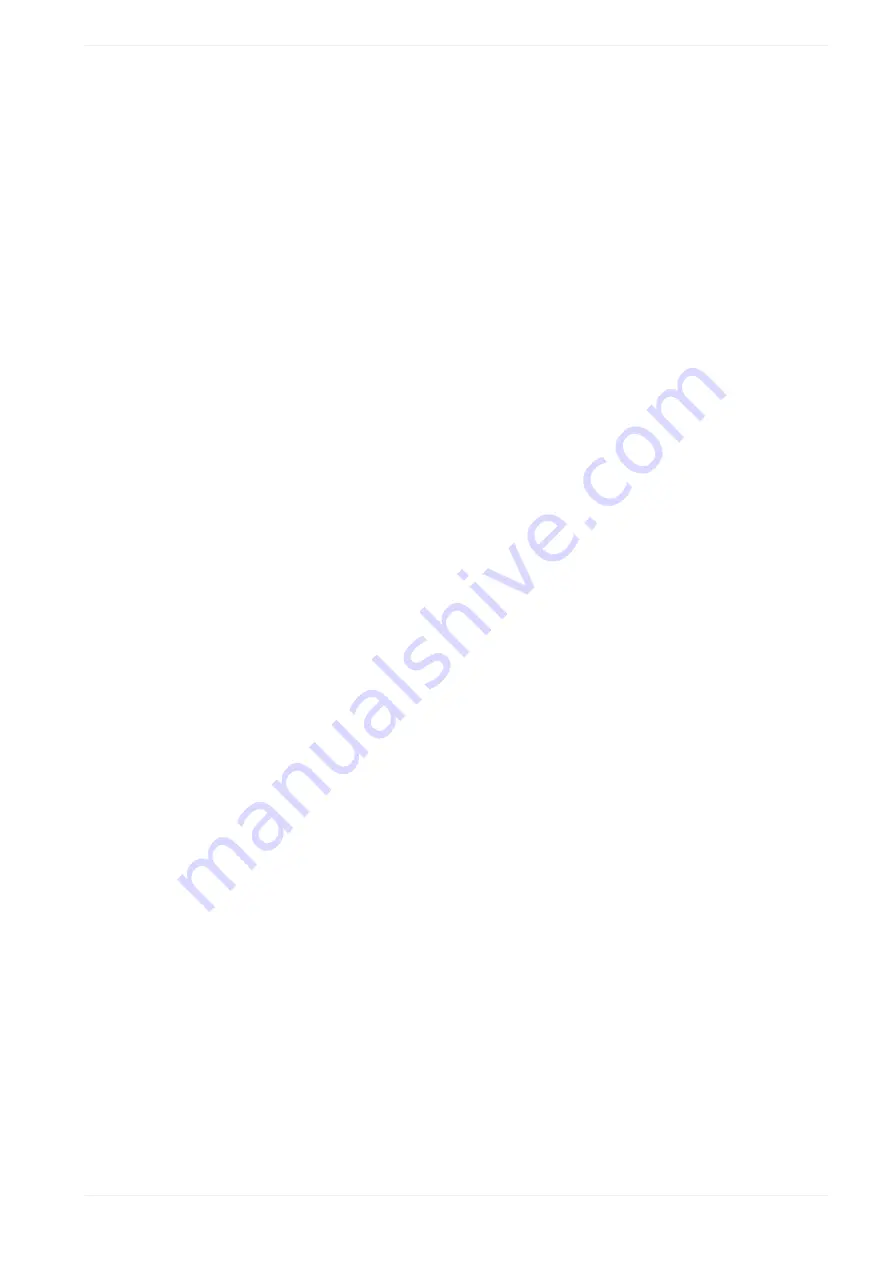
23 On-the-fly marking
Remarks
• When only one phase of the encoder is used, connect the encoder signal to ENCODER A
IN (X13) and connect ENCODER B IN (X14) to IN COM.1 (X2).
• Make sure the encoder frequency does not exceed 100kHz per phase.
• In some cases, the influence of line speed fluctuations may be reduced by lowering
the encoder resolution. However, a minimum encoder resolution of 25pulses/mm is
recommended.
• Adjust the setting value of the encoder resolution by checking the marking quality.
‒ When the character spacing is too wide, increase the value.
‒ When the character spacing is too narrow, decrease the value.
“Distance line speed sensors [mm]”
If “Line speed control” is set to “2 sensors input”, specify the distance between the sensors.
Under “Distance line speed sensors [mm]”, enter a value.
Connect the first sensor in moving direction to ENCODER A IN (X13) and the second sensor
to ENCODER B IN (X14) of the TERMINAL connector. Turn on ENCODER B IN (X14) within
10s from the signal input at ENCODER A IN (X13).
“2 Sensors input time-out [s]”
For “2 Sensors input time-out [s]”, specify the timeout period between turning on ENCODER
B IN (X14) and the marking trigger, e.g. signal input at TRIGGER IN (X5).
The warning E607 occurs if the marking trigger does not turn on within the set timeout period
from turning on the second sensor (ENCODER B IN (X14)).
For details about the control procedure and timing chart of the 2 sensors input, refer to the
“Setup and Maintenance Guide” of your laser marking system.
Related topics
Line speed control setting “2 sensors input”
On-the-fly-marking settings for one file
ME-NAVIS2-OP-1
243