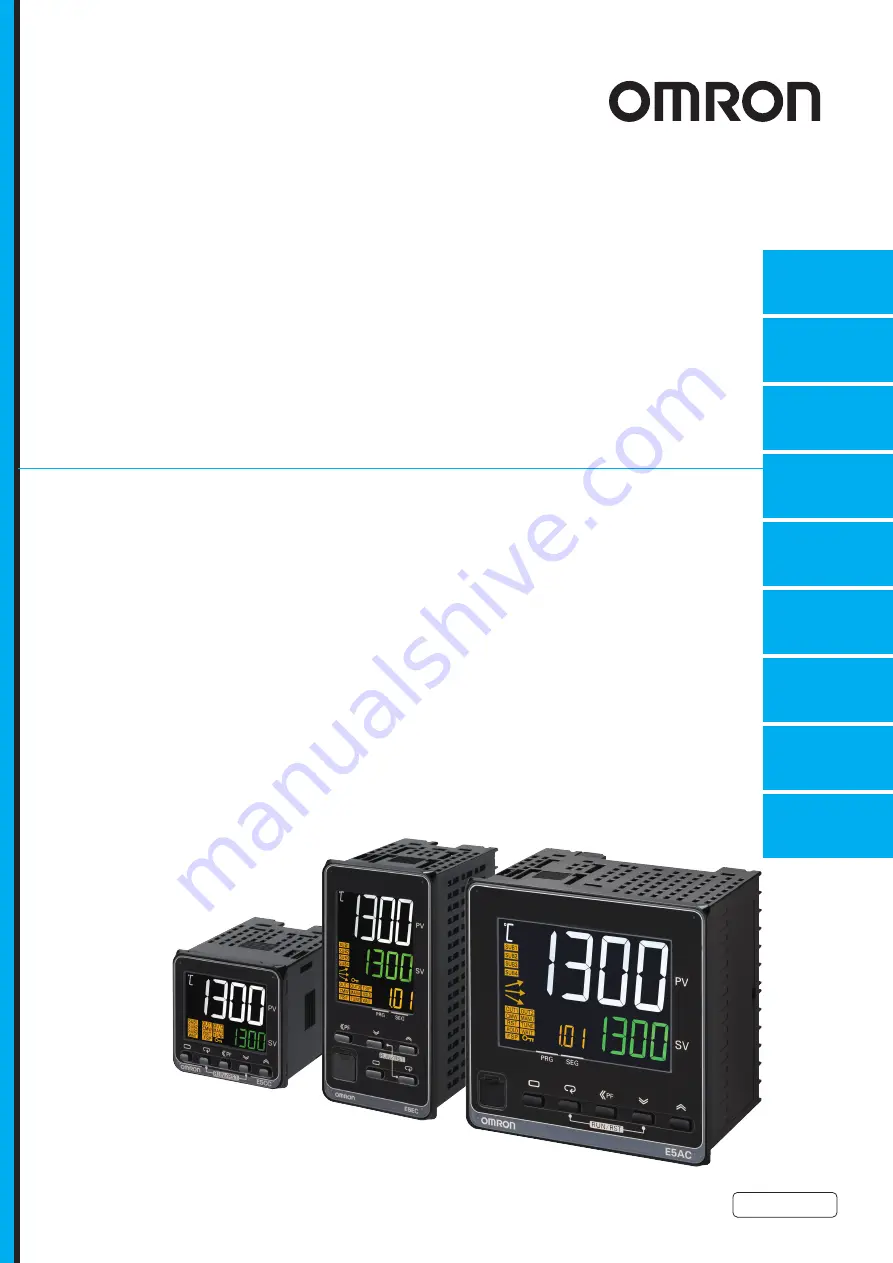
H186-E1-05
1
2
3
5
6
7
A
I
Digital Temperature Controllers
Programmable Type
Communications Manual
E5
@
C-T
Communications
Data for CompoWay/F
CompoWay/F Commu-
nications Procedures
Communications
Methods
Communications
Data for Modbus
Programless
Communications
Component
Communications
Modbus Communica-
tions Procedure
Appendices
Index
4
Summary of Contents for E5CC-T
Page 2: ......
Page 184: ...Index 4 E5 C T Digital Temperature Controllers Programmable Type Communications Manual H186...
Page 185: ......