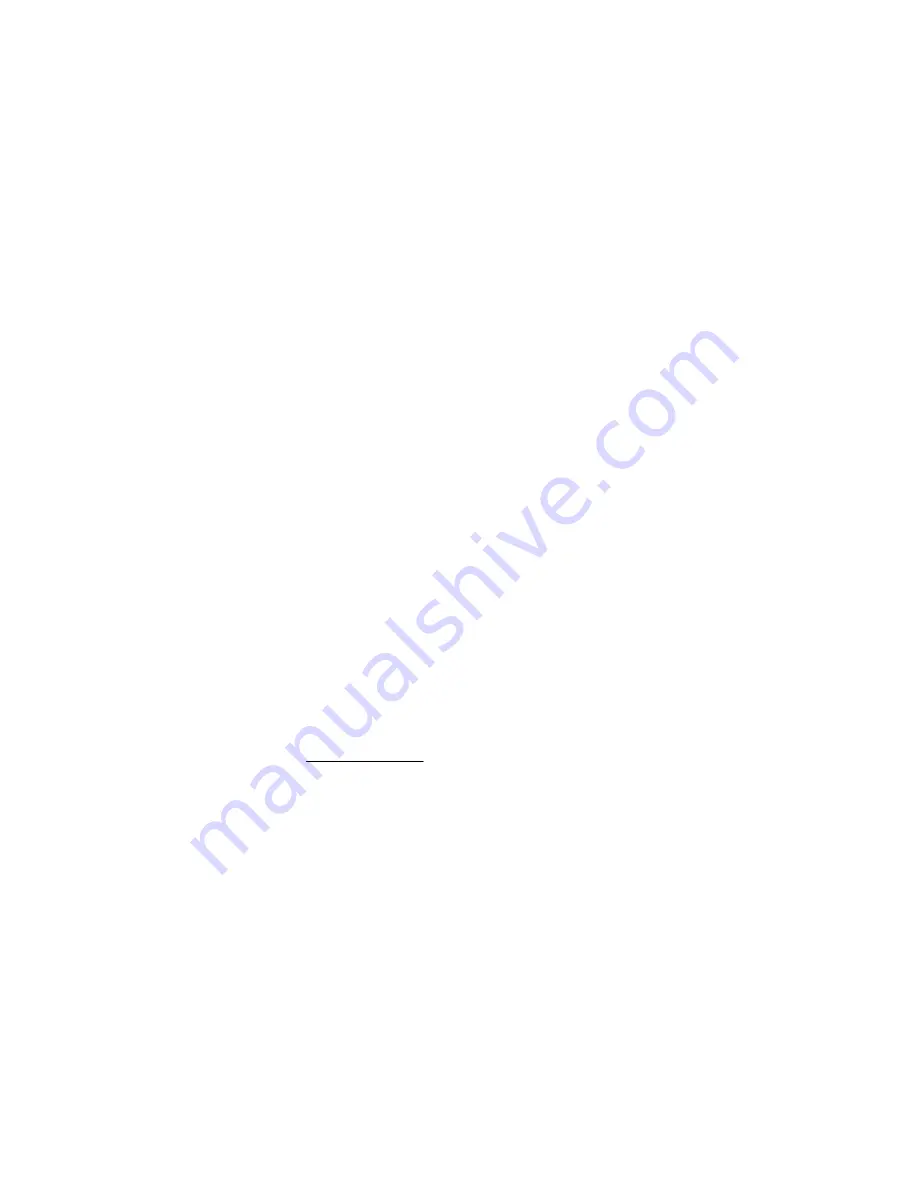
RP0200-2000
NACE International
7
_______________________________________________________________________
Appendix A: Typical Casing-Filling Procedures
Preparation
Casing Vent Pipes
A vent pipe shall be installed on each end of the casing,
and an opening in the casing at the vent-pipe connection
shall be provided. The opening shall be adequate in size
to allow for the flow of casing filler into the casing (a
minimum vent pipe opening of 5 cm [2 in.] is
recommended). Greater flexibility in the fill operation is
provided by installing a bottom-vent pipe on the lower
elevation of the casing and a top-vent pipe at the higher
elevation. The vent pipes and the casing annulus must
be free of restrictions to allow adequate flow of the
casing-filler material.
Casing End Seals
Casing end seals shall be inspected to ensure their
integrity and ability to contain the casing-filler material
during installation. If necessary, new casing end seals
shall be installed prior to the filling operation.
Fill Procedure
Filler Material
Casing-filler material is composed mainly of petrolatum
wax or petroleum-based compounds and contains
corrosion inhibitors, plasticizers, and thermal extenders.
The following are recommended characteristics for filler
material:
•
A minimum congeal point of 41
°
C (105
°
F), in
accordance with ASTM D 938
5
•
A 50 minimum cone penetration, in accordance with
ASTM D 937
6
•
Is nonhazardous and nonflammable
•
Is not water-soluble
A heated, insulated tanker with a permanent, variable-
flow pump should be used to fill the casing. For drum
installation, a 10:1 ratio mastic pump with inductor plate
is required.
An environmentally acceptable corrosion inhibitor may be
poured down the fill-vent pipe just prior to the installation
of the casing filler.
Hoses shall be connected to the fill-vent pipe. The filler
material shall be pumped into the casing until it is full. If
the casing contains water, the casing filler shall be
installed through the vent pipe at the high elevation of the
casing.
Vapor Phase Inhibitor
A vapor phase inhibitor may be injected into the casing
annulus through the vent pipes. The inhibitor is allowed
to vaporize and coat the carrier pipe. Periodically the
inhibitor must be replenished.
Analysis of Casing Filler Material
Upon completion of the filling procedure, casing-fill percentage should be calculated using Equation (A1).
Percentage
Fill
Casing
100
Volume
l
Theoretica
Volume
Actual
=
×
This calculation gives a rough approximation of the effectiveness of the casing filling. Individual casing-fill percentages may
vary considerably.
Casing-fill percentages may be unusually low because of:
•
A casing length that is smaller than that depicted on
the as-built drawings
•
Variations in the thickness of the coating on the
carrier pipe
•
Accumulation of dirt, mud, etc., in the casing
•
Water entrapped in the casing during the fill
•
Failure to take into account the displacement of the
isolators
Casing-fill percentages of individual casings may be
unusually high because of:
•
Discrepancies on the as-built drawings
•
Holes in the casing
•
Leaks in the casing end seals
Taking the average of several individual casing-fill
percentages provides a useful measure of the overall
performance of the casing-filling procedure. An average
casing-fill percentage lower than 85% is considered
questionable and should be investigated.
(A1)
Summary of Contents for CP 1
Page 1: ...CP 1 Cathodic Protection Tester Course Manual February 2005 NACE International 2000 ...
Page 265: ......
Page 266: ......
Page 267: ......
Page 268: ......
Page 301: ...RP0169 2002 32 NACE International ISBN 1 57590 035 1 ...
Page 535: ...TM0101 2001 24 NACE International ISBN 1 57590 137 4 ...