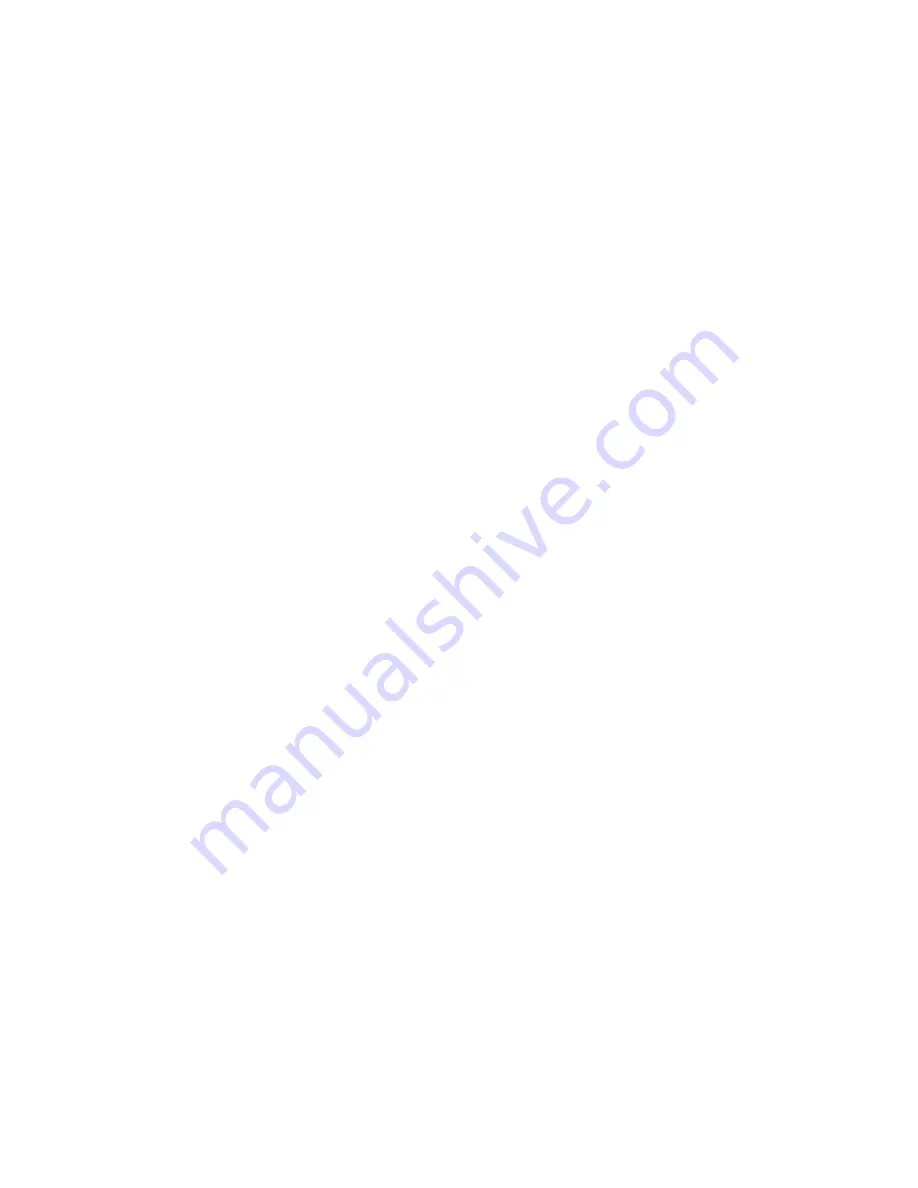
RP0176-2003
4
NACE International
3.3 Atmospheric Zone
3.3.1 This zone of an offshore structure extends up-
ward from the splash zone. It is exposed to sun, wind,
spray, and rain.
3.3.2 Corrosion in this zone is typically controlled by
the application of a protective coating system (see Sec-
tion 12). Steel surface areas requiring coating should
be minimized and/or made accessible by:
3.3.2.1 Substituting tubular members for other
structural shapes.
3.3.2.2 Seal welding and “boxing in” structural
units.
3.3.2.3 Eliminating skip welding.
3.3.2.4 Eliminating close-fitting and faying sur-
faces.
3.3.2.5 Providing padeyes to make scaffolding
and maintenance painting easier.
3.3.3 Nonferrous and nonmetallic materials minimize
atmospheric corrosion problems. For example, quart-
ers modules and lifeboats are available in aluminum
and composite materials such as glass-reinforced poly-
ester (GRP). Corrosion-resistant materials and compo-
sites can be used for handrails, electrical conduit, stair
treads, and deckplates. When dissimilar metals are
used, care must be taken to prevent galvanic corrosion
of the active component. Composite materials such as
GRP may be substituted for metals when resistance to
corrosion and/or weight reduction is desired. Safety
aspects regarding the use of these materials should be
considered.
3.3.4 Drilling fluids can damage protective coating sys-
tems and nonferrous metals such as aluminum and
zinc. Solid decks, splash walls, and a good drainage
system minimize coating damage and pollution caused
by drilling fluids.
3.4 Submerged Zone—External Areas
3.4.1 This zone extends downward from the splash
zone and includes any portion of the structure below
the mudline. Corrosion control for the external areas of
the submerged zone should be achieved through the
application of cathodic protection (CP) or by CP in con-
junction with coatings. To simplify the application of
effective cathodic protection, the following design fea-
tures are recommended:
3.4.1.1 Tubular members should be used wher-
ever possible. Recessed corners in channels and
“I” beams are difficult to protect. The crevice
formed by placing angles or channels back-to-
back cannot be reliably protected, and such con-
struction should not be used.
3.4.1.2 For structures in which fatigue or corro-
sion fatigue is a critical factor, welds may be stress
relieved to reduce the likelihood of fatigue or corro-
sion fatigue failures in the heat-affected zone
(HAZ). This may be important in cold-water envi-
ronments, where polarization tends to develop
slowly, or in partially shielded areas on a structure.
See API
(1)
RP 2A-WSD
4
and RP 2A-LRFD.
5
3.4.1.3 All weld joints should be continuous. Skip
and tack welding should not be used. If lap joints
are used, both edges should be continuously
welded. Bolted and riveted fittings should be
avoided.
3.4.1.4 Ballast control valve reach rods should be
designed so that they can be removed after a
structure has been set, whenever practical. If left
in place, they may shield adjacent structural mem-
bers from the CP current. Loose reach rods can
also cause chafing damage to the structure.
3.4.1.5 Piping, such as grout lines, well cutting
lines, discharge lines, water supply casings, and
pipeline risers, if clustered around a large struc-
tural member, can cause shielding and interfere
with the flow of CP current. Piping not needed for
continued operations should be removed if econo-
mically feasible. Lines not cheduled for removal
should be located to avoid CP shielding. A mini-
mum clear spacing of 1.5 diameters of the smaller
pipe should be provided. Coatings may be used
to minimize CP shielding.
3.4.1.6 Supplemental or replacement impressed
current anodes are sometimes required after a
structure has been placed in service. Designers
should consider providing spare “J” tubes for pul-
ling cables for add-on anodes and/or providing
brackets, guides, or clamps to facilitate such an-
ode additions or replacement.
3.4.1.7 Structure pilings should be protected by
the structure CP system. Piles driven through
jacket legs are normally bonded to the jacket by
welding, and thus receive CP. Skirt piles are typi-
cally driven inside submerged piling grout tubes
and then are grouted in place. Skirt piles may be
electrically connected to the jacket by means of
guide shoes, centralizers, or other acceptable bon-
ding methods. Corrosion rates below the mudline
are considered to be low. However, mudline cor-
rosion can be significant for structures with long
lifetimes. All mudline members, critical to the inte-
grity of the offshore structure, should be properly
connected to the CP system.
___________________________
(1)
American Petroleum Institute (API), 1220 L St. NW, Washington, DC 20005.
Summary of Contents for CP 1
Page 1: ...CP 1 Cathodic Protection Tester Course Manual February 2005 NACE International 2000 ...
Page 265: ......
Page 266: ......
Page 267: ......
Page 268: ......
Page 301: ...RP0169 2002 32 NACE International ISBN 1 57590 035 1 ...
Page 535: ...TM0101 2001 24 NACE International ISBN 1 57590 137 4 ...