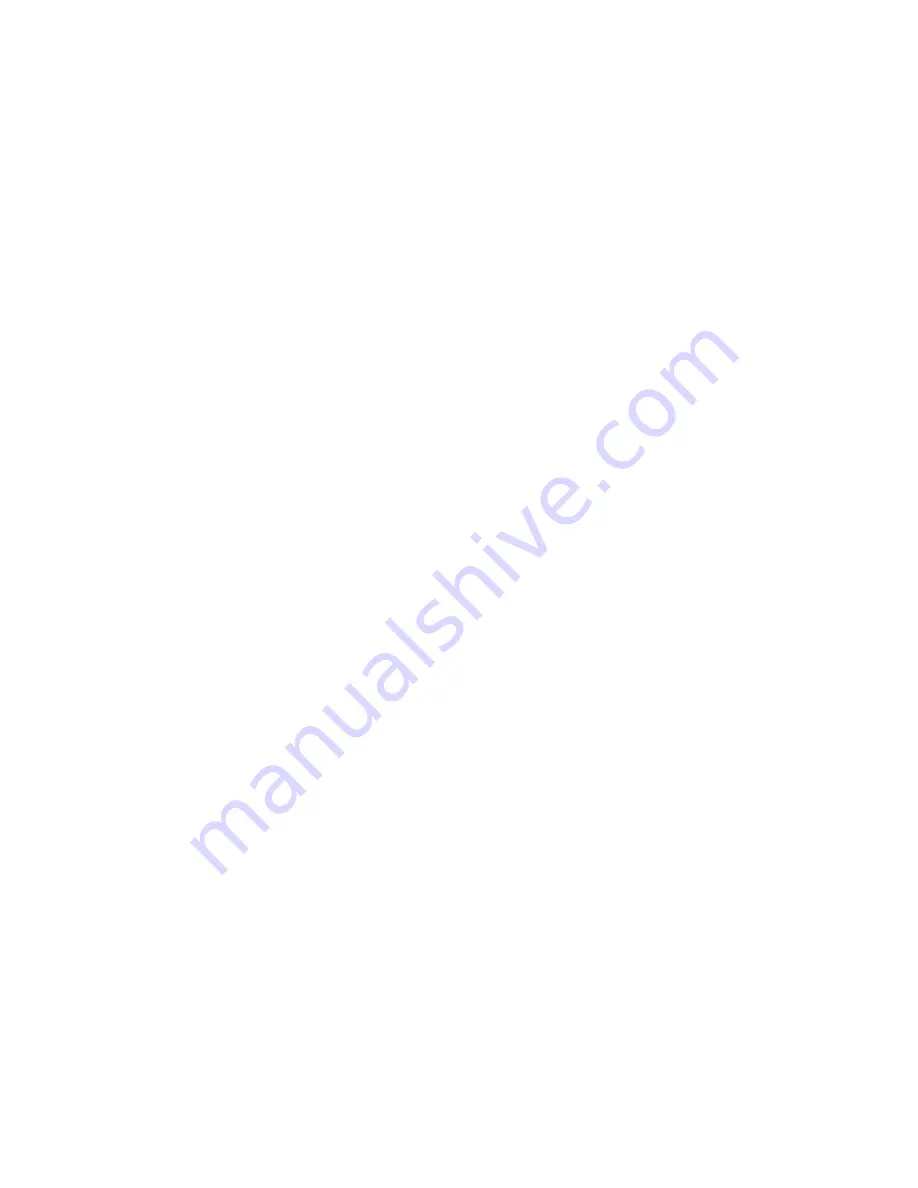
RP0200-2000
NACE International
3
4.3.4 If spiral welding or spiral-weld pipe is used for
the casing pipe, internal weld beads should be
ground down to allow proper pulling or sliding of the
carrier pipe to prevent damage to the isolators and
coating.
4.4 Installation of Carrier Pipe
4.4.1 Before the installation of isolating spacers, the
carrier pipe coating shall be electrically inspected
(i.e., holiday tested or “jeeped”) using an approved
electrical holiday detector and in accordance with
NACE Standard RP0274
3
or RP0490.
4
The casing
isolators shall be installed according to the
manufacturer’s instructions and in the quantity
recommended by the manufacturer. The inspector
shall ensure that the installation is conducted in a
manner that does not damage the carrier pipe
coating. Isolator runners (skids) shall be oriented
properly. Bolts, if present, should not remain at the
bottom (6 o’clock) position. If possible, end caps
shall be installed on the carrier pipe to aid in smooth
push/pull operations.
4.4.2 Casing isolators shall be carefully selected to
ensure they have the mechanical strength required to
withstand the actual installation considering all
conditions including pipe weight, length of casing,
conditions of weld beads, deflections in the casing,
and other field conditions. Selection should include
an evaluation of the ability of the casing isolators to
provide electrical isolation after enduring the rigors of
installation. (See NACE Standard RP0286 for
additional information.)
4.4.3 The casing shall be visually inspected and, if
necessary, cleaned (swabbed) immediately prior to
installing the carrier pipe to remove any
debris/foreign material.
4.4.4 The carrier pipe shall be installed by a crane or
side-boom tractor using slings or belts that do not
interfere with the isolators or damage the coating. If
attached to the end caps, the pull cable shall be fed
through the casing in a manner that does not
damage the casing. The alignment of the pipe and
casing must be ensured both prior to and during
insertion of the carrier pipe into the casing. During
the installation operation, it must be ensured that
there is no isolator and/or spacer displacement or
damage to the carrier pipe coating. The push/pull
operation shall continue in a smooth motion until the
carrier pipe is properly positioned.
NOTE: Casing isolating spacers may slide along the
carrier pipe during installation if not installed
properly, if the casing is bent, or if the installation is
out of line. Inadequate support of the pipe allows the
pipe to sag and make metallic contact with the
casing. The inspector should be aware of this
potential problem during the installation.
4.4.5 The cased crossing shall be tested in
accordance with Section 5 to confirm that the casing
and carrier pipe are not electrically shorted. The
carrier pipe and casing shall be cleaned as
necessary for the installation of the end seals in
accordance with design specifications and the
manufacturer’s recommendations. All coating
damage shall be repaired in accordance with the
coating vendor’s or applicable specifications.
4.4.6 The previous sections on handling pipe are
also applicable to the installation of uncoated carrier
pipe.
4.5 Test Leads: Test lead wires shall be installed on the
carrier pipe using a thermite weld or other approved
process. Test lead wires are required on the carrier pipe
at both ends of the casing. In the event that the original
cable is lost or damaged, a spare lead wire may be
installed to perform the tests in Appendix B and to
confirm the integrity of the other lead. The test lead-to-
pipe connection shall be properly coated and any damage
to the pipe or pipe coating shall be repaired in
accordance with applicable specifications. Wrapping the
test leads around the vent pipe shall be avoided to
prevent the possibility of electrical shorting. Test lead
wires are required for the casing if nonmetallic vent pipes
are installed or if the metallic vent pipes use mechanical
couplings/fittings. The use of color-coded test lead wires
is desirable.
4.6 Backfilling: The casing and carrier pipe shall be
backfilled with debris-free material. The carrier pipe and
casing shall be supported using earth-filled bags,
compacted earth, or other methods to prevent settlement
during the backfilling operation. Caution must be
exercised to prevent test-lead damage, which is a
common cause of shorting. Testing as described in
Section 5 shall be performed upon completion of the
backfilling operation.
4.7 Split-Casing Extensions and Installations
4.7.1 Extension of existing casings or construction of
new casings on existing pipelines often involves
installation by the split-casing/split-sleeve method.
This method is required if the pipeline cannot be
taken out of service and the subsequent blow-down
(gas), or drain-up (liquid), and cutting out of the road
crossing to allow a casing to be slipped over the
pipeline is not feasible or cost-effective.
Summary of Contents for CP 1
Page 1: ...CP 1 Cathodic Protection Tester Course Manual February 2005 NACE International 2000 ...
Page 265: ......
Page 266: ......
Page 267: ......
Page 268: ......
Page 301: ...RP0169 2002 32 NACE International ISBN 1 57590 035 1 ...
Page 535: ...TM0101 2001 24 NACE International ISBN 1 57590 137 4 ...