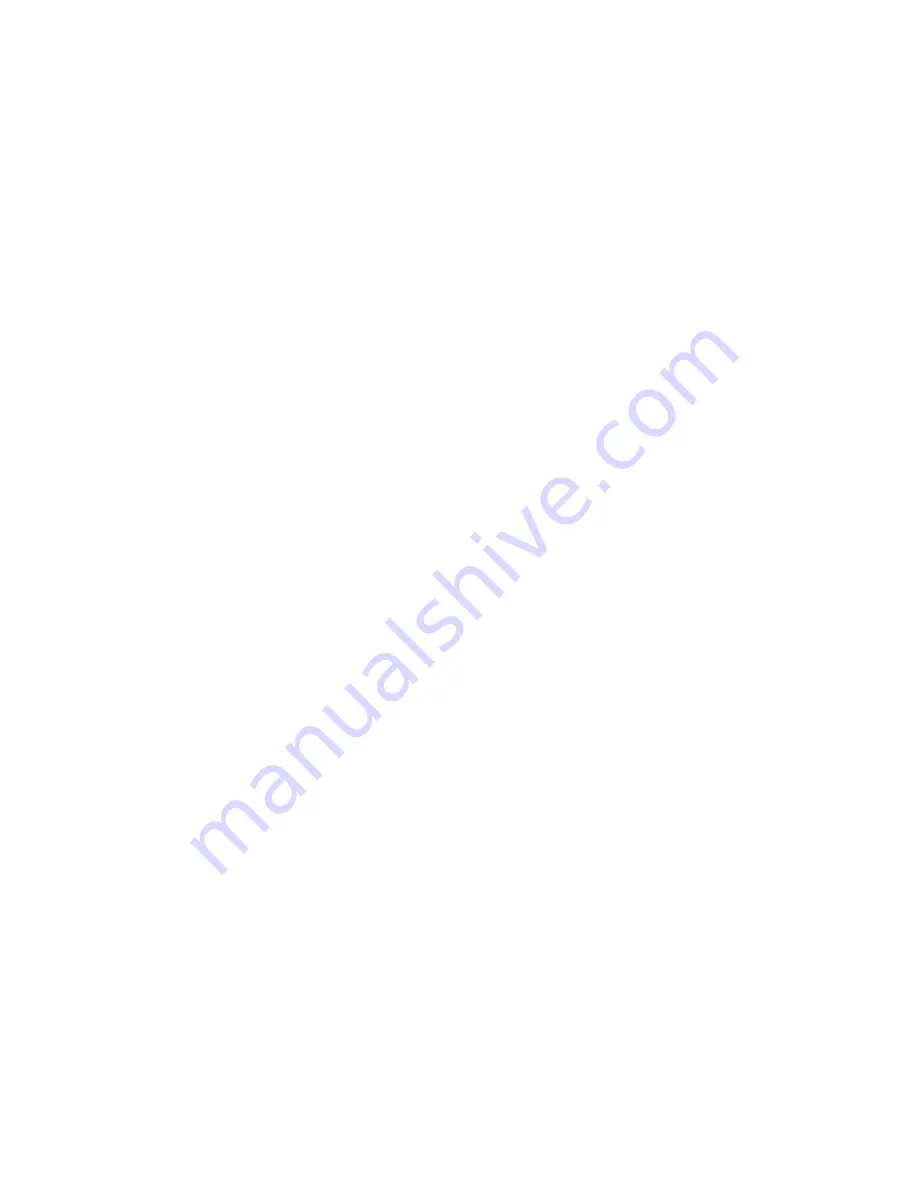
RP0176-2003
NACE International
25
excellent preconstruction primers because of their
abrasion and impact resistance and ability to pro-
tect the steel during long construction cycles.
However, care must be taken to ensure that the
zinc-primed surface is clean prior to topcoating.
Fresh-water washing or power scrubbing may be
required to remove contaminants.
13.3.2.3 Organic inhibitive primers—These mater-
ials may be solvent-based, chemically cured coat-
ings, or thermoplastics, which form films by solvent
evaporation. Chemically cured coatings generally
require mixing of a second component for curing.
Characteristically, these coatings include inhibiting
pigments that must meet regulatory standards and
limitations and be environmentally safe. On con-
tact with moisture, the pigments generate either
alkaline or ionic conditions that retard the corro-
sion of the base metal. Because these primers
generally contain reactive pigments and are only
part of a protective coating system, they must be
protected with topcoats to perform as effective
environmental barriers. Primers must conform to
all applicable regulations regarding toxicity, safety,
and environmental standards.
13.3.3 Topcoats—Primers used for offshore struc-
tures should be overcoated with intermediate and/or
finish coats. These coatings function as barriers, re-
tarding and restricting the permeation of water vapor,
oxygen, and active chemical ions. Topcoats may also
provide added impact resistance and solvent resist-
ance, as well as an aesthetically pleasing finish. Gen-
eric characteristics of topcoats include the following:
13.3.3.1 Chemically Cured Coatings—These mat-
erials are usually epoxies, epoxy phenolics, poly-
esters, or some polyurethanes that are cured by
mixing with a second component commonly called
a “catalyst” or converter. These coatings, which
are often applied in films exceeding 100 µm (4
mils) thickness per coat, have excellent chemical-
resistant properties. Because these materials
continue to cure on exposure, they become
increasingly hard, brittle, and solvent-resistant with
age. Therefore, recoating may require sweep
blasting to achieve good mechanical bonding.
With the exception of some polyurethanes, these
coatings tend to chalk on exposure to ultraviolet
light. These materials tend to be temperature- and
moisture-sensitive during curing and require ade-
quate temperatures and humidity control to cross-
link and develop into chemically resistant films.
13.3.3.2 Solvent-Deposited or Thermoplastic-
Type Coatings—These materials include vinyl
acrylics, vinyls, or chlorinated rubbers. These
coatings dry by the evaporation of solvents, which
distinguishes them from epoxies, polyesters, and
other chemically cured coatings. The change from
a liquid to a solid state is not accompanied by any
chemical change. This mode of drying permits
coating application at relative humidities of up to
90% and temperatures as low as 0°C (32°F).
These coating films generally exhibit excellent re-
sistance to environmental conditions. These sol-
vent-soluble films simplify overcoating by providing
solvent bonding between a refresher and previous
coat. Principal disadvantages of these coating
materials are limited temperature resistance (60 to
77°C [140 to 170°F]), reduced solvent resistance,
and low solids-by-volume content. Because of the
low solids-by-volume content, additional coats may
be required to achieve the desired thickness. Re-
cent technology indicates greater film and solids-
by-volume capabilities may reduce the number of
coats previously required. However, their chem-
ical resistance may be impaired. Furthermore,
regulations regarding volatile organic compounds
(VOC) limitations may prohibit the application of
the materials in some localities.
13.3.4 Thermal-sprayed aluminum
13.3.4.1 Thermal-sprayed aluminum (either flame
or arc) applied to 200 µm (8 mils) and sealed with
a silicone sealer has been used in atmospheric
service for specific applications such as flare
booms. Good surface preparation and cleanliness
are essential. Ninety-nine percent or higher-purity
aluminum or Al-5Mg is most commonly used with
two or more spray passes used in the application.
The sealer enhances service life and appearance.
U.S. Military Specification MIL-STD-2138
12
offers
guidelines for application and quality control.
13.3.4.2 Coating adhesion should exceed 7,000
kPa (1,000 psi) (see Paragraph 10.4.6.2).
13.4 Criteria for Coating Selection
13.4.1 Accelerated tests designed for coating selec-
tion include:
(a) Salt spray testing (4,000 h) in accordance with
ASTM B 117.
22
(b) Weatherometer testing (2,000 h) in accord-ance
with ASTM G 152,
23
ASTM G 153,
24
ASTM G 154,
25
or
ASTM G 155.
26
(c) Humidity cabinet testing (4,000 h) in accordance
with ASTM D 2247.
27
Some operators run combinations of the above tests
on a rotating basis, such as 1,000 h in salt spray, 1,000
h in a weatherometer, followed by an additional 1,000 h
in salt spray, and a final 1,000 h in a weatherometer.
13.4.2 Other coating properties that can be deter-
mined from laboratory tests and that may aid in evalu-
ating materials are:
Summary of Contents for CP 1
Page 1: ...CP 1 Cathodic Protection Tester Course Manual February 2005 NACE International 2000 ...
Page 265: ......
Page 266: ......
Page 267: ......
Page 268: ......
Page 301: ...RP0169 2002 32 NACE International ISBN 1 57590 035 1 ...
Page 535: ...TM0101 2001 24 NACE International ISBN 1 57590 137 4 ...