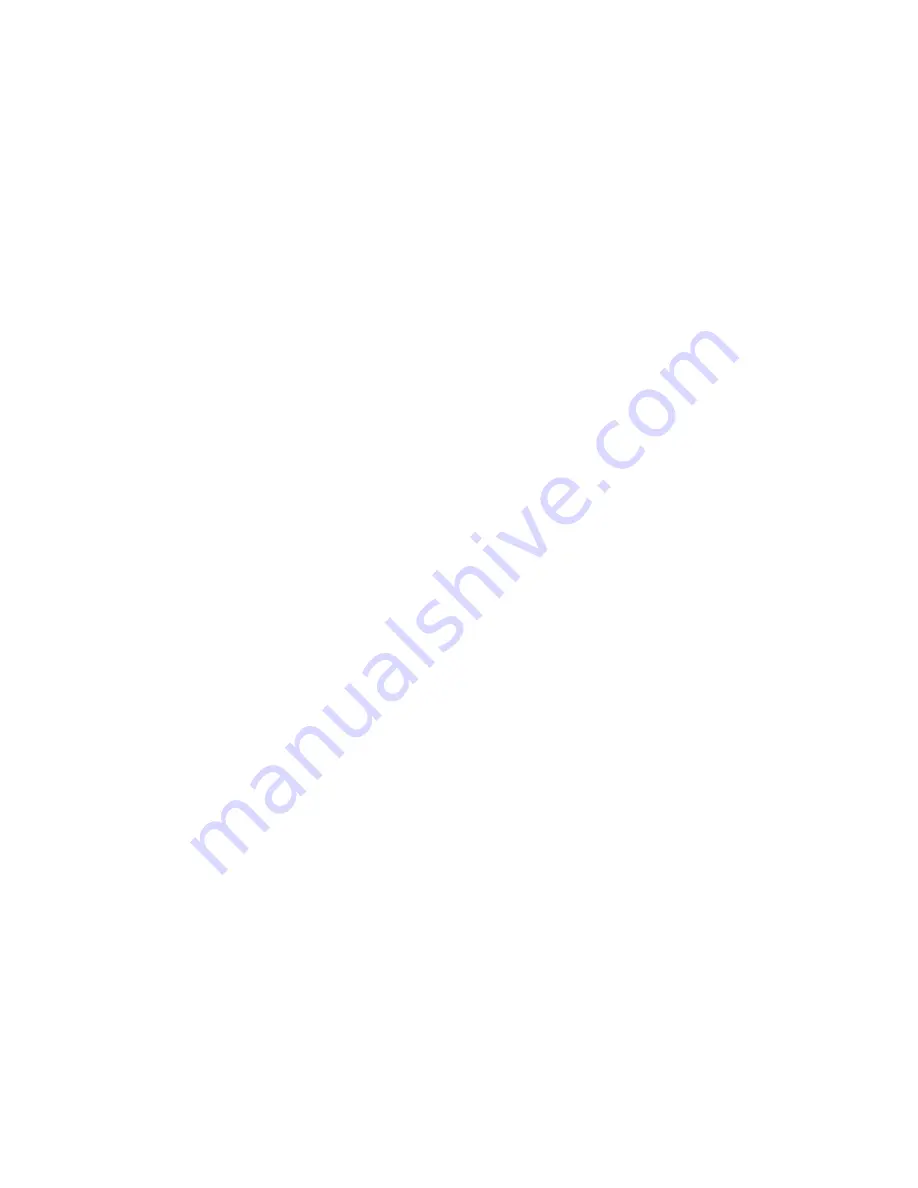
RP0176-2003
NACE International
21
10.4.2.2 Because this coating cannot be applied
in the fabrication yard, it is normally restricted to
straight runs of tubular members.
10.4.2.3 A minimum of 50 mm (2.0 in.) should be
left uncoated at each end of a tubular member to
prevent damage to the chloroprene during the
welding operations.
10.4.3 High-build organic coatings
10.4.3.1 These coatings are usually filled with sil-
ica glass-flake or fiberglass.
10.4.3.2 These coatings are typically applied to
thicknesses of 1 to 5 mm (40 to 200 mils) over an
abrasive blast-cleaned surface.
10.4.3.3 Because this coating may be applied in
the fabrication yard after assembly, joints may be
protected as well as straight tubular runs.
10.4.3.4 To improve inspection possibilities, an
antifouling coating may be applied on the coated
members. Antifouling coatings are effective up to
about 10 years.
10.4.4 High-performance structure coating systems
250 to 500 µm (10 to 20 mils)
10.4.4.1 Although some high-performance coating
systems currently used to protect the atmospheric
zone have performed reasonably well in the splash
zone, they are not suited as a primary control
measure for long-life structures.
10.4.5 Heat-shrink sleeves. NOTE: Heat-shrink
sleeves have not performed well in the North Sea.
10.4.5.1 Heavy plastic sleeves that shrink when
exposed to an elevated temperature and are pre-
coated internally with a sealant adhesive have
been used to protect straight tubulars in the splash
zone. If the sleeve is slightly damaged, the visco-
elastic nature of the sealant in combination with
the remaining radial shrink forces of the sleeve
causes the sealant to flow to the damage site and
effectively seal over the damage. Surface prepar-
ation to remove rust and coarse roughness is re-
quired.
10.4.6 Thermal-sprayed aluminum
10.4.6.1 Thermal-sprayed aluminum (either flame
or arc) applied to 200 µm (8 mils) and sealed with
a silicone sealer have been used in the splash
zone. Good surface preparation and cleanliness
are essential. The coating should be applied in a
minimum of two passes. The sealer seals the por-
osity of the coating and enhances service life and
appearance. U.S. Military Specification MIL-STD-
2138
12
offers guidelines for application and quality
control.
10.4.6.2 Coating adhesion should exceed 7,000
kPa (1,000 psi). Laboratory adhesion tests may
be performed using ASTM C 633.
13
Field testing
for adhesion may be performed with commercial
instruments.
10.4.6.3
Thermal-sprayed aluminum has also
been used in submerged and marine atmospheric
services. For submerged areas this system is a
candidate for areas in which protective CP poten-
tials may be difficult to achieve, such as the under-
side of clamps and other geometrically shielded
areas.
10.4.7 Petrolatum/wax-based tape systems
10.4.7.1 Petrolatum/wax-based coating systems
with appropriate jacketing for mechanical protec-
tion may be employed.
10.4.7.2 Proper consideration shall be given to the
mechanical stresses to be encountered in service
by the coating system, and the protective jacketing
system shall be selected to assure adequate
mechanical protection.
________________________________________________________________________
Section 11: Maintenance of Splash Zone Corrosion Control Measures
11.1 This section lists inspection procedures and follow-up
maintenance necessary to ensure continued protection of
the structural steel located in the splash zone.
11.2 Inspection
11.2.1 The splash zone interval should be visually in-
spected annually to determine whether corrosion con-
trol is still effective. If failure has occurred, the extent of
damage to underlying structural members should be
assessed and corrective action taken.
11.2.2 When wear plates are used and the protective
coating system has either deteriorated or been mech-
anically damaged, periodic wall thickness measure-
ments should be made to determine that the loss does
not exceed the corrosion allowance.
Summary of Contents for CP 1
Page 1: ...CP 1 Cathodic Protection Tester Course Manual February 2005 NACE International 2000 ...
Page 265: ......
Page 266: ......
Page 267: ......
Page 268: ......
Page 301: ...RP0169 2002 32 NACE International ISBN 1 57590 035 1 ...
Page 535: ...TM0101 2001 24 NACE International ISBN 1 57590 137 4 ...