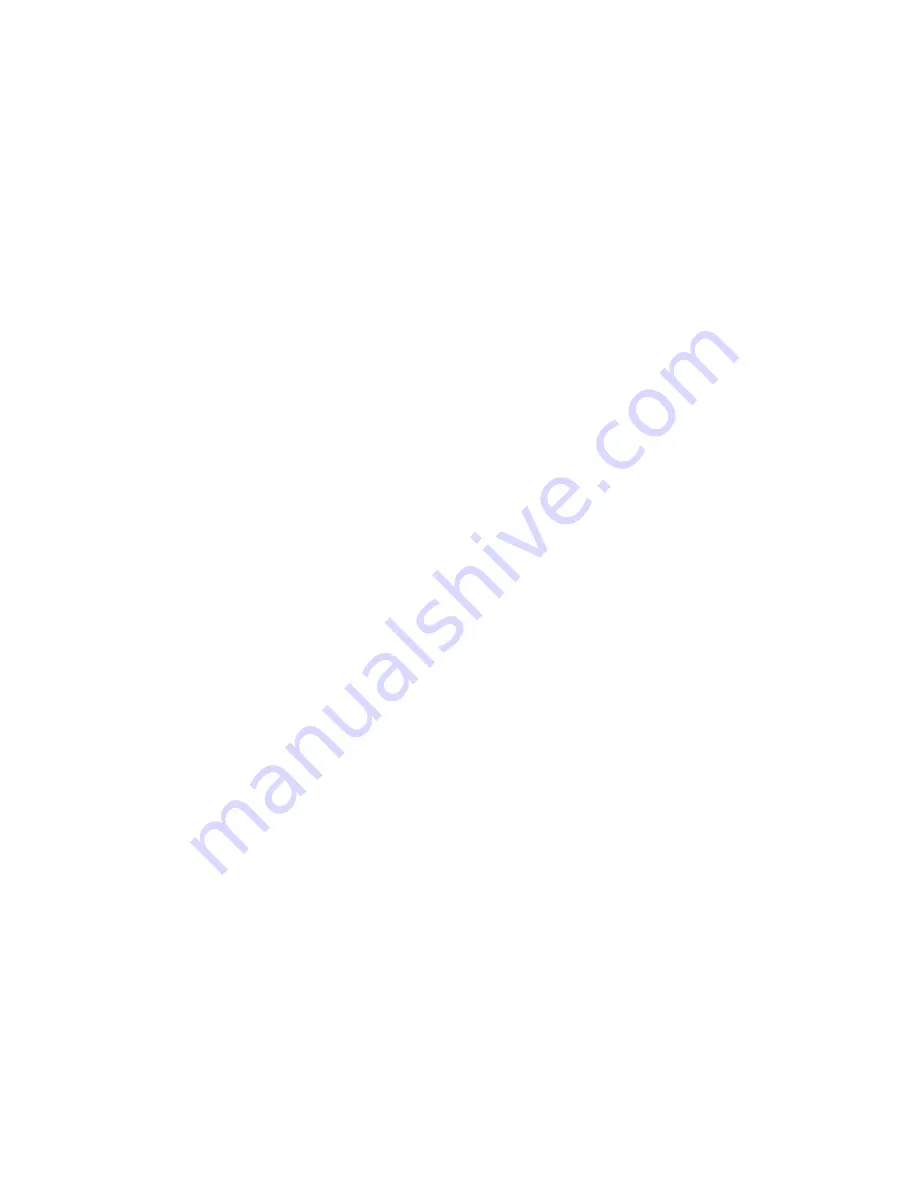
RP0176-2003
22
NACE International
11.3 Repair Methods
11.3.1 UNS N04400 sheathing
11.3.1.1 Tears in the UNS N04400 sheathing
should be trimmed and repaired by welding or
banding a UNS N04400 patch to the affected area.
11.3.1.2 An alternative procedure, which can also
be performed at the water line, involves blast
cleaning the damaged area after trimming the torn
UNS N04400 and hand applying a thick coat of
polysulfide rubber with air cure accelerator or
splash zone barrier compound. The latter is a
polyamide-cured epoxy formulated to displace
water and cure underwater. If the area is exposed
to wave action, it may be necessary to hold these
compounds in place with wire mesh or burlap until
the cure is complete
11.3.2 Vulcanized chloroprene
11.3.2.1 The procedure outlined in Paragraph
11.3.1.2 should be followed.
11.3.3 High-build organic coatings
11.3.3.1 Damaged areas may be repaired by
spray or hand application of the original coating to
an abrasive blast-cleaned surface or as outlined in
Paragraph 11.3.1.2.
11.3.4 Heat-shrink sleeves
11.3.4.1 The steel surface should be cleaned, and
any sharp projections should be removed.
11.3.5 Fiberglass wraps with water-activated resin
11.3.5.1 The steel surface should be cleaned to
remove marine growth, and any sharp projections
should be removed.
11.3.5.2 This system may use an initial sealer
wrap to isolate the steel surface from seawater
effectively. The outer fiberglass wrap provides a
mechanical barrier.
11.3.6 Mastic-backed rubber wraps
11.3.6.1 The steel surface should be cleaned to
remove marine growth, and any sharp projections
should be removed.
________________________________________________________________________
Section 12: Surface Preparation
12.1 Introduction
12.1.1 This section recommends procedures for the
proper surface preparation of structural steel shapes to
be coated for service in the atmospheric zone of fixed
offshore structures.
12.2 General
12.2.1 The objectives of surface preparation for steel
in the atmospheric zone are to provide the necessary
degree of cleanliness and the specified anchor pattern
required for the designed coating system.
12.2.2 Automated blast-cleaning machines are econo-
mically desirable as a means of preparing plate,
beams, and tubular members prior to fabrication.
12.2.3 The completed structure should be inspected
to locate damaged or improperly primed areas prior to
topcoating. Damaged areas and all weld areas require
spot blasting and priming with the same material prior
to completing the coating system.
12.2.4 All surface imperfections such as slivers, lam-
inations, welding flux, weld spatter, and underlying mill
scale exposed before or during operations shall be re-
moved prior to surface preparation.
12.2.5 Surface preparation performed outside should
be completed during daylight hours with the surface
temperature above the dew point for that day, early
enough to permit proper priming of the surface prior to
the development of any moisture or flash rusting of the
prepared surface. Tests for soluble salts should be
performed prior to coating when the presence of any
soluble salt on the prepared surface is suspected.
12.2.6 At the time of surface preparation or priming
the surface temperatures shall be 3°C (5°F) or more
above the dew point. Under no condition should a
steel surface be conventionally coated while it is damp
or wet.
12.2.7 If properly performed with containment, wet
abrasive blasting may provide adequate surface prep-
aration and reduce the dust problem created by dry
blasting. However, if this type of cleaning is used, the
coating systems must be compatible with the rust inhib-
itor used in the water blasting system. The surface
prepared for coating must be dry and contaminant-free
prior to coating.
12.2.8 Solvent or detergent degreasing shall be per-
formed in accordance with SSPC
(9)
SP 1.
14
___________________________
(
9)
SSPC: The Society for Protective Coatings, 40 24
th
St., 6
th
Floor, Pittsburgh, PA 15222-4656.
Summary of Contents for CP 1
Page 1: ...CP 1 Cathodic Protection Tester Course Manual February 2005 NACE International 2000 ...
Page 265: ......
Page 266: ......
Page 267: ......
Page 268: ......
Page 301: ...RP0169 2002 32 NACE International ISBN 1 57590 035 1 ...
Page 535: ...TM0101 2001 24 NACE International ISBN 1 57590 137 4 ...