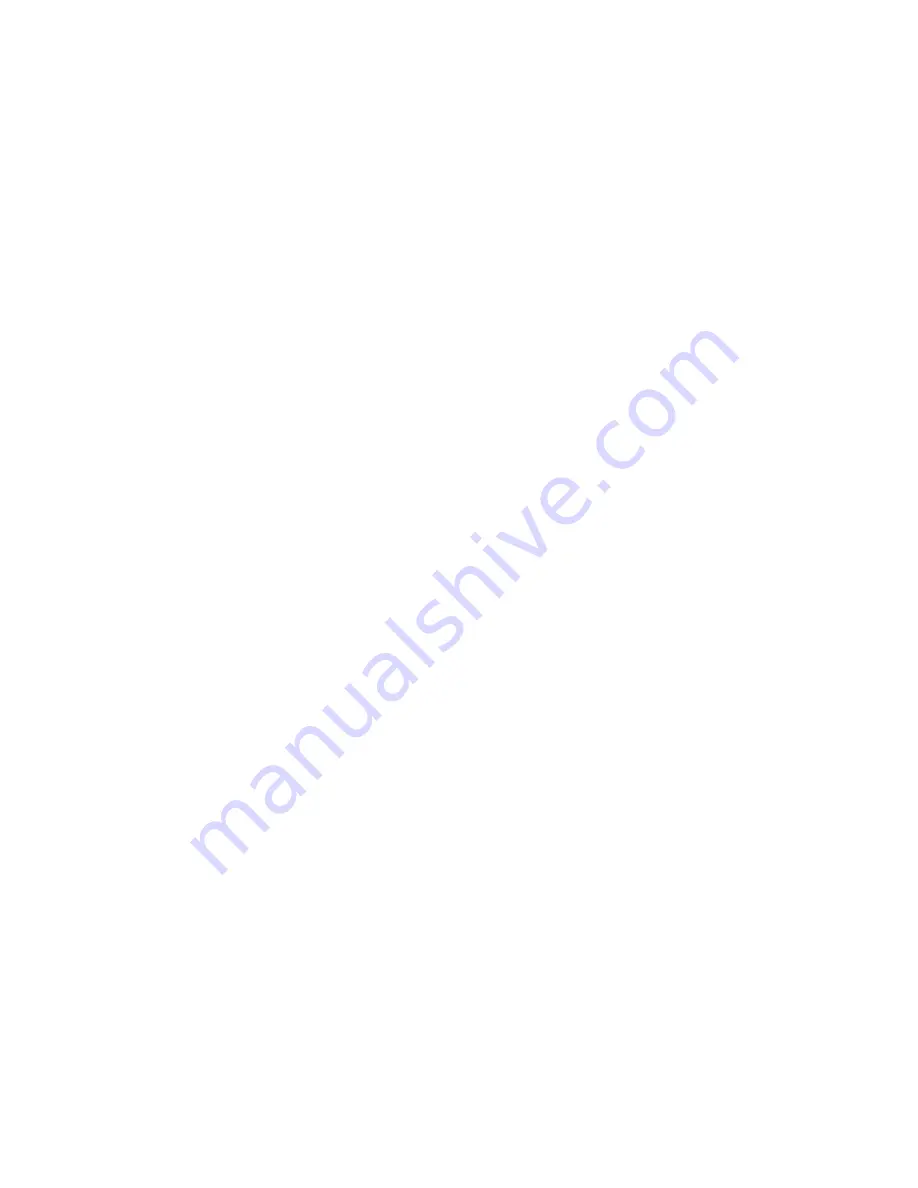
RP0200-2000
4
NACE International
4.7.2 Split-casing extensions are normally specified
to match the size of the existing casing.
Occasionally the configuration of the existing pipeline
requires the installation of an oversized casing
extension. In this case, a standard-welded or conical
reducer may be used to achieve the size transition.
4.7.3 The carrier pipe section to be cased shall be
carefully excavated. The carrier pipe shall be
cleaned, properly coated where necessary, and
properly supported to prevent possible damage due
to sagging. After existing casing seals and vents are
removed, the vent-pipe hole shall be capped with a
steel plate. To prevent coating damage, the carrier
pipe shall be protected during burning and welding
operations with an insulating shield of nonflammable
material.
4.7.4 The existing casing ends shall be prepared for
welding in accordance with applicable specifications.
The carrier pipe coating shall be inspected and
repaired. The electrical-isolating and spacing
materials shall be installed in accordance with
applicable specifications.
4.7.5 The pipe to be used in the casing extension
shall be specified to provide metallurgical and
physical compatibility with the existing casing.
If a manufactured split casing is not used, splitting of
the casing shall be performed in a manner that
minimizes warping or disfigurement of the pipe.
Hinges are sometimes welded to the casing to
maintain proper alignment of the casing halves
during installation. The new casing vent hole shall
be cut using the procedure described in Paragraph
4.3.3.
4.7.6 The split casing shall be carefully positioned
over the existing carrier pipe in a manner that avoids
any damage to the pipe, coating, or spacing
materials. Seam welding shall be performed in
accordance with applicable specifications. The
casing seams are often tack welded at specified
intervals prior to the continuous welding operation to
prevent warping. During this welding operation,
nonflammable, insulating backing material shall be
used to protect seam areas on the carrier pipe while
the split casing halves are being properly supported.
The installation of new vent piping, test leads, and
backfilling shall be performed in accordance with
Paragraphs 4.3.3, 4.5, and 4.6, respectively.
_______________________________________________________________________
Section 5: Maintenance And Repair
5.1 Actions necessary in the course of pipeline
maintenance may include:
•
Eliminating metallic contact
•
Removing the casing
•
Replacing the carrier pipe
•
Providing supplemental cathodic protection to the
casing
•
Filling the casing with a dielectric material
•
Installing a new crossing
•
Monitoring the condition of the casing
•
Coating or recoating the carrier pipe
•
Replacing
end
seals
•
Removing electrolyte from inside the casing
5.2 Maintenance of cased crossings is sometimes
necessary. Typical situations include:
•
Corrosion or other damage to the carrier pipe or
casing pipe is indicated by inspection.
•
Casing extension or removal is necessary.
•
The casing is in electrical metallic contact with
(shorted to) the carrier pipe.
•
The casing becomes filled or partially filled with
electrolyte and an internal “electrolytic” contact
develops.
5.2.1 The casing could have come into electrical
contact with the carrier pipe in several ways:
•
The carrier pipe moved in the casing, causing it
to come into metallic contact with the casing at
some point; such contact often occurs at the
ends of the casing.
•
Spacing materials failed during or after the
original installation of the pipeline.
•
The pipe was inadequately supported within the
casing, allowing it to sag and come into metallic
contact with the bottom of the casing.
•
The carrier pipe was intentionally shorted or
installed without isolators.
•
A foreign object such as a shovel or other
metallic material present at the construction site
was accidentally left in the casing.
•
A short developed between the test lead and the
vent pipe or the casing test leads.
5.3 Maintenance of Vents and Test Leads: Maintenance
of casing vents includes coating at the soil/atmosphere
interface and painting, repair, or replacement of vents
and vent caps. Test leads shall be checked annually to
determine their integrity.
Summary of Contents for CP 1
Page 1: ...CP 1 Cathodic Protection Tester Course Manual February 2005 NACE International 2000 ...
Page 265: ......
Page 266: ......
Page 267: ......
Page 268: ......
Page 301: ...RP0169 2002 32 NACE International ISBN 1 57590 035 1 ...
Page 535: ...TM0101 2001 24 NACE International ISBN 1 57590 137 4 ...