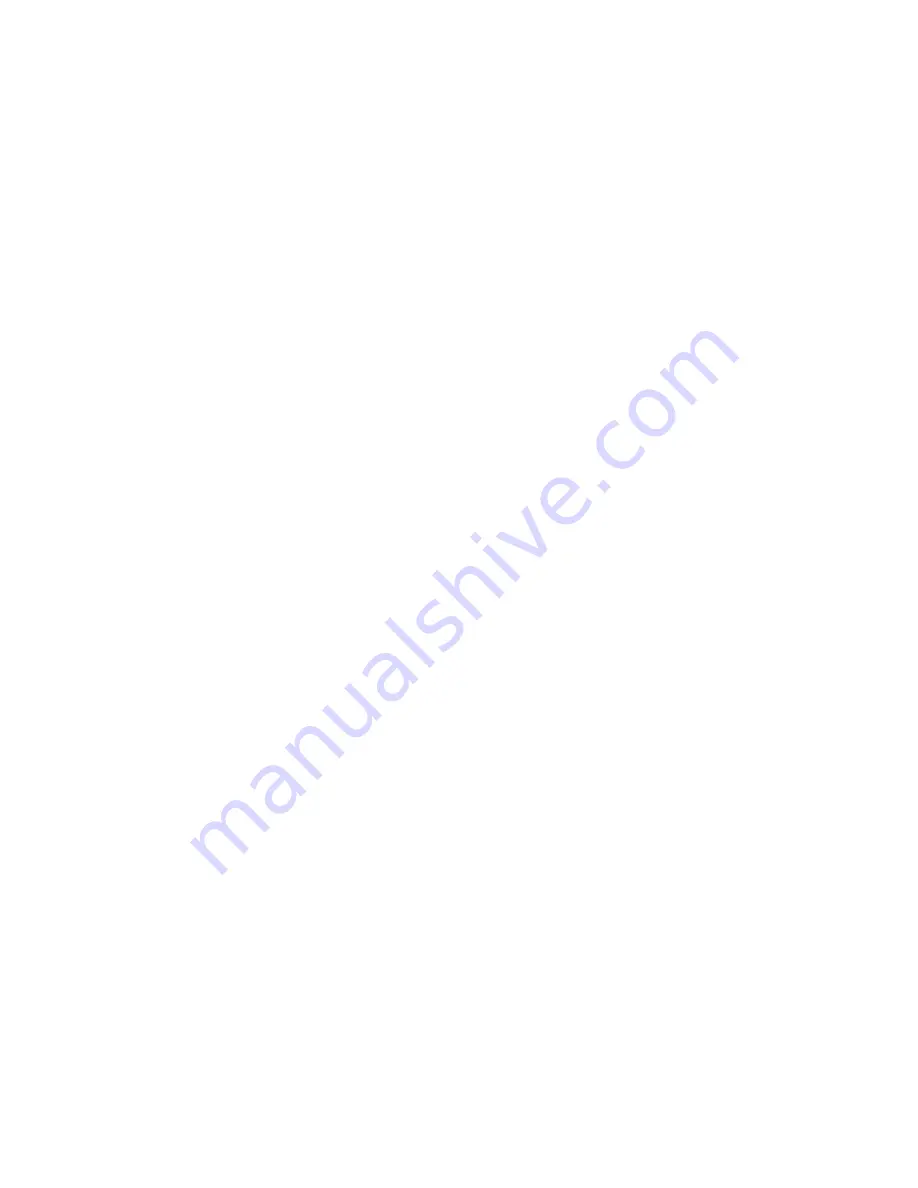
RP0196-2004
NACE International
3
3.3 Uncoated Steel Tanks
3.3.1 It is feasible to design a CP system to provide
complete protection for uncoated submerged surfaces
of steel tanks (see Section 4).
3.3.2 It may be more practical to protect a bare or
poorly coated steel tank with an impressed current
system. This method is described in NACE Standard
RP0388.
1
3.4 Economic Considerations
3.4.1 For coated steel tanks, the cost of CP should be
compared with the cost of recoating and metal loss. In
addition to extending the life of existing coatings, CP
reduces the need for recoating, repairs, leakage, and
replacement caused by metal loss at holidays in the
coating.
3.4.2 Metal loss can be reduced by the application of
CP where the submerged surfaces are not coated or
where the coating has deteriorated to the point that
these surfaces can be considered uncoated. The cost
of installing CP, projected maintenance costs, and
monitoring costs should be compared with the cost of
coating maintenance, metal loss, service disruption,
reduction in tank life, and water quality degradation.
3.5 Operational Considerations
3.5.1 Removing the tank from service for coating
maintenance or repairing corrosion damage can be
eliminated or postponed if the CP system is designed
and operated properly.
________________________________________________________________________
Section 4: Design of Galvanic Anode CP Systems
4.1 General
4.1.1 The elements that the corrosion engineer must
consider when designing galvanic anode CP systems
for steel water storage tanks are outlined in this
section.
4.1.2 In the design of a galvanic anode system, the
following items must be considered:
(a) Health and safety,
(b) Compliance with local and national regulations,
3
(c) Design of the tank (accessibility, crevices, shielded
areas, baffles, and compartments),
(d) Present and future condition of the coating and the
generic type of coating employed,
(e) Whether the water is subject to freezing,
(f) Driving voltage of various galvanic anode
materials,
(g) Galvanic anode material, configuration, and circuit
resistance,
(h) Galvanic anode life and ease of replacement,
(i) Ancillary
equipment,
(j) Reference electrode location(s),
(k) Possibility of vandalism, and
(l) Water chemistry and temperature.
4.1.3 Whenever possible, the design should be based
on standard galvanic anode shapes and sizes.
4.1.4 Selection of materials and system design shall
strive to provide the best economic balance between
the installation cost and the maintenance cost over the
design life of the system.
4.2 Design Information
4.2.1 Before a galvanic anode CP system is designed,
the following information should be obtained:
(a) Dimensions of the tank, including inlet/outlet
columns, if any,
(b) Area of continuously and intermittently submerged
steel surfaces,
(c) Flow patterns, recirculation, and the presence and
design of internal heaters and baffling,
(d) Chemical analysis of the water and variation with
seasons,
(e) Conductivity range, pH, and velocity of water,
(f) Frequency and rate of emptying and filling the
tank,
(g) Type, condition, and age of internal coating
system,
(h) Condition of internal steel surfaces exposed to the
water,
(i) Whether the water is subject to freezing,
(j) Water temperature range, and
Summary of Contents for CP 1
Page 1: ...CP 1 Cathodic Protection Tester Course Manual February 2005 NACE International 2000 ...
Page 265: ......
Page 266: ......
Page 267: ......
Page 268: ......
Page 301: ...RP0169 2002 32 NACE International ISBN 1 57590 035 1 ...
Page 535: ...TM0101 2001 24 NACE International ISBN 1 57590 137 4 ...