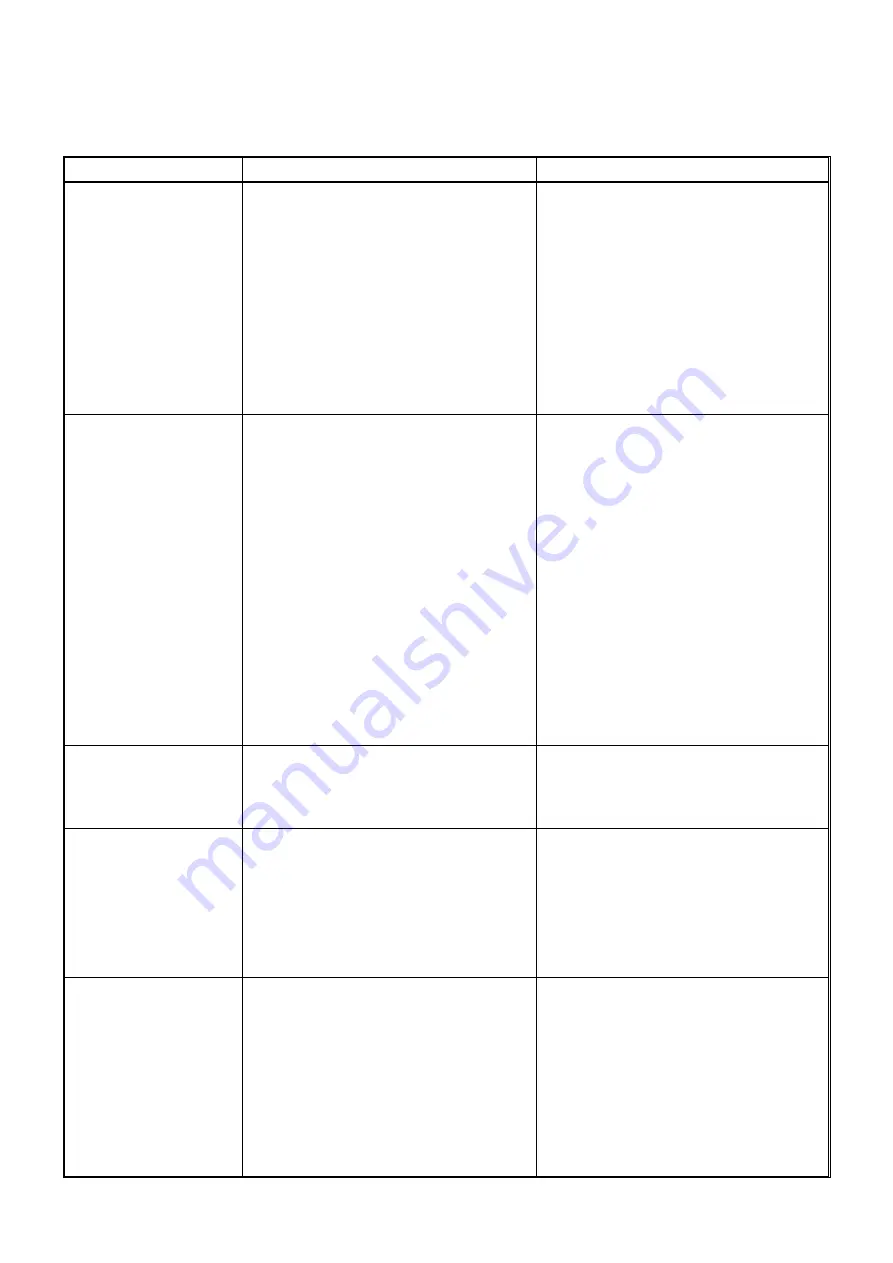
2-60
6.4 FAILURE CAUSE AND COUNTERMEASURE
While each of the items indicated in the following table appears to be an independent problem, two or more of them
may occur concurrently.
Accordingly, employ such a method that the causes can be removed one by one.
Abnormal Phenomenon
Cause
Remedy
Oil leakage from a spool
seal area.
・
Sealing parts are scratched, or the seal lip
is worn out after serving for a long period
of time.
・
The sliding area of spool seal is scratched
from the outside (impact dent, scratch
blemish, etc.).
・
Mounting of the cover accommodating
sealing parts is strained.
・
The paint applied on the spool seal sliding
area is still sticking.
・
The tank circuit pressure has risen to
exceed the withstanding performance of
the sealing parts.
・
Replace with new ones.
・
Repair or replace the spool.
・
Correct it to the normal shape, while
checking the seal lip for its abrasion state.
・
Remove it by using diluent, or remove it
mechanically. Be cautious of possible
damage to the spool surface or seal lip.
・
Remove any object that increases the flow
resistance.
Spool sliding is not
smooth.
・
A foreign object is caught in the spool
sliding section.
・
Loss of oil film between the spool and
body due to an abnormal oil temperature
rise
・
Failure in lubrication due to degradation of
hydraulic oil
・
Abrasion of spool caused by a long time
use or uneven loading
・
The spool is bent by an external force.
・
Distortion of the whole valve body caused
by the stain on the mounting face.
・
Excessive tightening of valve mounting
bolts
・
Oil deposition inside each spring cover on
the spool operating side and on the other
side.
・
Overhaul the setup and repair or replace.
・
Take necessary measures to lower the oil
temperature. Also, if the relief valve is
operating frequently, check for the cause
and decrease the frequency.
・
Not only the oil replacement, but the
overhaul of the circuit may be required.
・
Check the spool diameter and determine if
it should be replaced.
・
Check the spool for its straightness and
other characteristics, and repair or replace
it as required.
・
Loosen the mounting bolts and check for
any cause of strain.
・
Re-tighten them with the specified torque.
・
Overhaul the setup and repair or replace
the seal.
Fails to travel (but
pressure rises).
・
The spool fails to perform the specified
stroke (6 mm).
・
The crawlers are overloaded.
・
The circuit is clogged with foreign objects
or piping is folded and bent.
・
Inspect the traveling lever link and repair
as required.
・
Check for any obstacle and clean it.
・
Check the piping for any bent or foreign
matter, and repair and clean as required.
The spool cannot be kept
at the neutral position.
・
The excessive gap between spool and
body causes an excessive leak.
・
The spool has not returned to the neutral
position correctly.
・
A foreign object is caught in the seat area
of port relief valve and anti-cavitation
valve, or the seat is damaged.
・
Replace the spool, or replace the valve
block assembly.
・
Manual operation: Inspect the traveling
lever link and repair as required.
・
Hydraulic operation: Check the pilot
pressure.
・
Overhaul the setup and repair or replace.
Fails to travel (and
pressure does not rise).
・
A foreign object is caught in the seat area
of relief valve, or the seat is damaged.
・
Loosening of relief valve adjusting screw
・
A foreign object is caught in the seat area
of port relief valve and anti-cavitation
valve, or the seat is damaged.
・
The spool fails to perform the specified
stroke (6 mm).
・
Oil flow rate from the pump is insufficient.
・
Overhaul the setup, check for foreign
matters, repair and clean or replace it.
・
Give an additional tightening to the
adjusting screw.
・
Overhaul the setup, check for foreign
matters, repair and clean or replace it.
・
Manual operation: Inspect the traveling
lever link and repair as required.
・
Hydraulic operation: Check the pilot
pressure.
・
Check the pump and repair it as required.
Summary of Contents for MK0003
Page 2: ......
Page 8: ...0 6...
Page 12: ...1 4 2 DIMENSIONAL DRAWING OF OUTRIGGER WIDTH...
Page 17: ...1 9 4 WORKING RADIUS LIFTING HEIGHT...
Page 18: ...1 10 Working range diagram Outrigger extended to maximum Main boom 1 section...
Page 19: ...1 11 Working range diagram Outrigger extended to maximum Main boom 2 sections...
Page 20: ...1 12 Working range diagram Outrigger extended to maximum Main boom 2 5 sections...
Page 21: ...1 13 Working range diagram Outrigger extended to maximum Main boom 3 sections...
Page 22: ...1 14 Working range diagram Outrigger extended to minimum Main boom 1 section...
Page 23: ...1 15 Working range diagram Outrigger extended to minimum Main boom 2 sections...
Page 24: ...1 16 Working range diagram Outrigger extended to minimum Main boom 2 5 sections...
Page 25: ...1 17 Working range diagram Outrigger extended to minimum Main boom 3 sections...
Page 26: ...1 18 5 RATED TOTAL LOAD CHART...
Page 32: ...2 4...
Page 33: ...2 5 1 HYDRAULIC CIRCUIT DIAGRAM 200 1176600...
Page 34: ...2 6...
Page 35: ...2 7 2 HYDRAULIC PIPING DIAGRAM 2 1 CRANE ROTATING PART 200 1171800...
Page 41: ...2 13 2 2 CONTROL LINE A...
Page 43: ...2 15 2 3CONTROL LINE B Perform spiral winding on the entire perimeter of the hose of this part...
Page 45: ...2 17 2 4 TRAVEL LINE...
Page 47: ...2 19 2 5 OUTRIGGER LINE...
Page 49: ...2 21 2 6 PT LINE 102 1152000 4...
Page 69: ...2 41...
Page 70: ...2 42...
Page 71: ...2 43...
Page 76: ...2 48 4 8 ENGINE ACCESSORIES 102 1149200...
Page 90: ...2 62 7 2 INTERNAL STRUCTURE...
Page 120: ...2 92 Part B Writing method for wire number Two places...
Page 123: ...2 95 Figure 1 Index point Figure 2 Connection diagram...
Page 166: ...2 138 15 4 APPEARANCE OF OUTRIGGER ON REAR LEFT SIDE 200 2167300...
Page 173: ...2 145 17 ELECTRIC CIRCUIT DIAGRAM 200 1176500 01...
Page 174: ...2 146 18 ELECTRIC SYSTEM 18 1 1 WIRE HARNESS OF MACHINE BODY 1 200 1172200 1...
Page 176: ...2 148 18 1 2 WIRE HARNESS OF MACHINE BODY 2 200 1172200 2...
Page 179: ...2 151 19 CONTROL ASSEMBLY 19 1 CONTROLLER 1 TTC60 Pin arrangement...
Page 180: ...2 152 TTC60 I O...
Page 181: ...2 153 2 TTC36X Pin arrangement...
Page 182: ...2 154 TTC36X lower part I O...
Page 209: ...2 181 19 2 5 LIST OF CONTROLLER INPUT MONITORING...
Page 210: ...2 182 19 2 6 LIST OF CONTROLLER ANALOG INPUT OUTPUT MONITORING...
Page 245: ...3 9 1 2 3 ANGLE METER 360 S200M3297000...
Page 274: ...3 38...
Page 293: ...4 19 8 SERVICE LOCATIONS...
Page 294: ...4 20...
Page 296: ...5 2 1 ELECTRICAL MOTOR UNIT ASSEMBLY Unit weight 180 kg...
Page 324: ...5 30...
Page 325: ...5 31 4 ELECTRICAL DIAGRAM S200M3122000 01...
Page 326: ...5 32 S200M3122000 02...
Page 336: ...6 8 1 3 2 INTERNAL STRUCTURE OF WINCH MOTOR...
Page 345: ...6 17 4 WORKING RADIUS LIFTING HEIGHT OF ONE FALL WINCH...
Page 348: ......