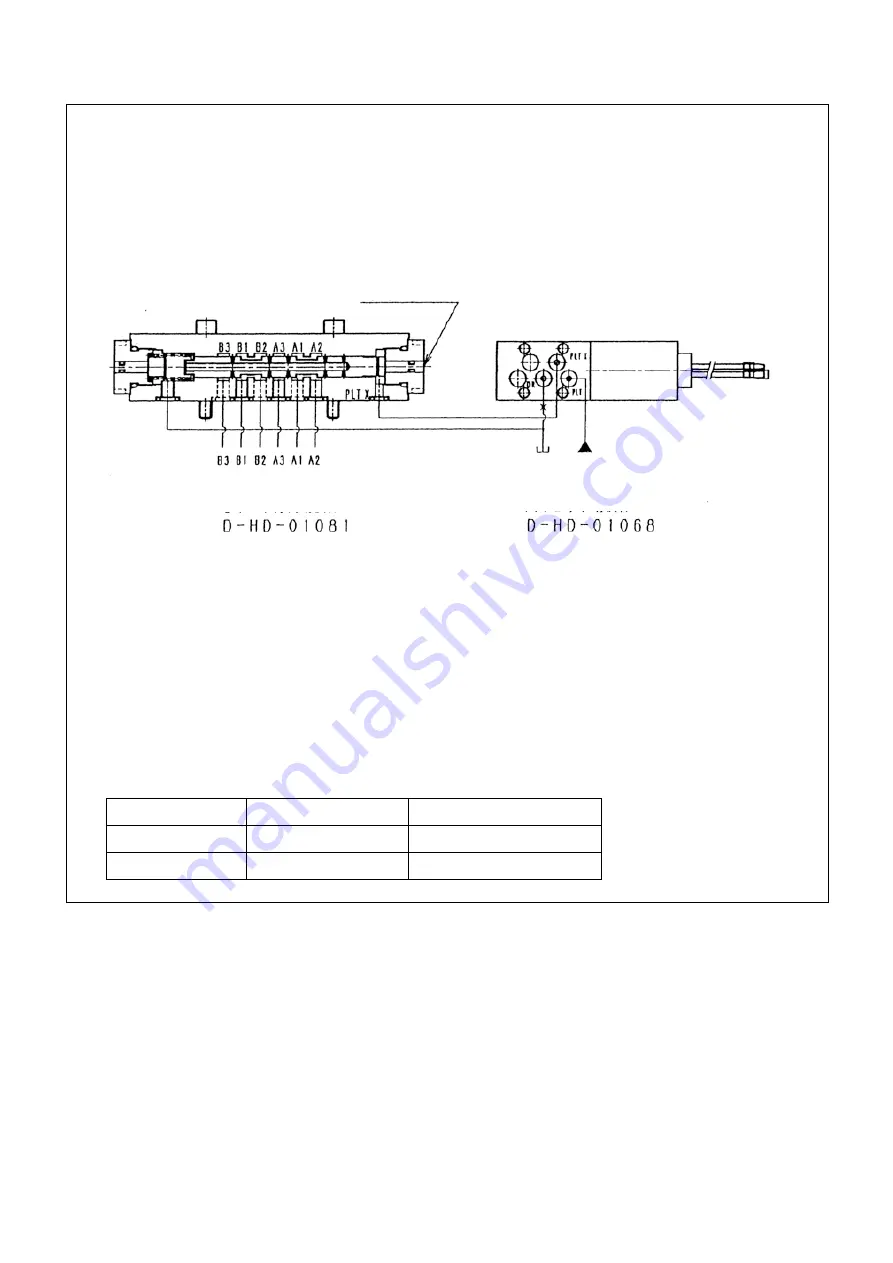
2-86
9.4 METHODS FOR OPERATION ADJUSTMENT
6-port directional switching valve (D-HD-01081)
1) Pilot switching valve: Energizing the solenoid of D-HD-01068 allows the PLT X port of pilot
switching valve to generate and apply pressure to the PLT X port of 6-port directional switching
valve: D-HD-01081.This pilot pressure pushes the spool of 6-port directional switching valve to
generate the flow of A1 to A3, and B1 to B3 in order to allow actuators to work. Turning off the
power supply to the solenoid causes the spring to push back the spool of 6-port switching valve
to result flows of A1 to A2 and B1 to B2.
2) When electrical checking cannot be exercised, pressing the manual operating pin of 6-port
directional switching valve enables the checking of operation.
Precautions:
1) If tightened excessively, a mounting bolt may give rise to strain in the body, resulting in
malfunctioning. Limit the tightening torque of a mounting bolt within a range of 6 to 8 N·m.
2) When tightening a mounting bolt, pay attention to prevent the O-ring from being squeezed out
and the valve from being dropped or mounted in a wrong direction.
3) This valve has been manufactured by high-precision machining. If it is clogged with a foreign
matter, even if it is a minute particle, the spool may fail to move and may no longer perform the
valve functions. To allow it to work normally, execute a sufficient flushing of piping and use a
strainer and filter with pores no larger than 100
μ
.
4) For the hydraulic oil, we recomment oils conforming to ISO VG32, ISO VG46, or an equivalent
one.
5) To maintain the specified viscosity, be cautious of oil temperature. Use hydraulic oils within the
temperature range specified below: (Recommended values)
Oil type
Oil temperature
Viscosity
ISO VG32
0 to 60°C
Approx. 15 to 340 mm
2
/s
ISO VG46
6 to 65°C
Approx. 18 to 340 mm
2
/s
Manual operation pin
6-port directional switching valve
Pilot switching valve
Summary of Contents for MK0003
Page 2: ......
Page 8: ...0 6...
Page 12: ...1 4 2 DIMENSIONAL DRAWING OF OUTRIGGER WIDTH...
Page 17: ...1 9 4 WORKING RADIUS LIFTING HEIGHT...
Page 18: ...1 10 Working range diagram Outrigger extended to maximum Main boom 1 section...
Page 19: ...1 11 Working range diagram Outrigger extended to maximum Main boom 2 sections...
Page 20: ...1 12 Working range diagram Outrigger extended to maximum Main boom 2 5 sections...
Page 21: ...1 13 Working range diagram Outrigger extended to maximum Main boom 3 sections...
Page 22: ...1 14 Working range diagram Outrigger extended to minimum Main boom 1 section...
Page 23: ...1 15 Working range diagram Outrigger extended to minimum Main boom 2 sections...
Page 24: ...1 16 Working range diagram Outrigger extended to minimum Main boom 2 5 sections...
Page 25: ...1 17 Working range diagram Outrigger extended to minimum Main boom 3 sections...
Page 26: ...1 18 5 RATED TOTAL LOAD CHART...
Page 32: ...2 4...
Page 33: ...2 5 1 HYDRAULIC CIRCUIT DIAGRAM 200 1176600...
Page 34: ...2 6...
Page 35: ...2 7 2 HYDRAULIC PIPING DIAGRAM 2 1 CRANE ROTATING PART 200 1171800...
Page 41: ...2 13 2 2 CONTROL LINE A...
Page 43: ...2 15 2 3CONTROL LINE B Perform spiral winding on the entire perimeter of the hose of this part...
Page 45: ...2 17 2 4 TRAVEL LINE...
Page 47: ...2 19 2 5 OUTRIGGER LINE...
Page 49: ...2 21 2 6 PT LINE 102 1152000 4...
Page 69: ...2 41...
Page 70: ...2 42...
Page 71: ...2 43...
Page 76: ...2 48 4 8 ENGINE ACCESSORIES 102 1149200...
Page 90: ...2 62 7 2 INTERNAL STRUCTURE...
Page 120: ...2 92 Part B Writing method for wire number Two places...
Page 123: ...2 95 Figure 1 Index point Figure 2 Connection diagram...
Page 166: ...2 138 15 4 APPEARANCE OF OUTRIGGER ON REAR LEFT SIDE 200 2167300...
Page 173: ...2 145 17 ELECTRIC CIRCUIT DIAGRAM 200 1176500 01...
Page 174: ...2 146 18 ELECTRIC SYSTEM 18 1 1 WIRE HARNESS OF MACHINE BODY 1 200 1172200 1...
Page 176: ...2 148 18 1 2 WIRE HARNESS OF MACHINE BODY 2 200 1172200 2...
Page 179: ...2 151 19 CONTROL ASSEMBLY 19 1 CONTROLLER 1 TTC60 Pin arrangement...
Page 180: ...2 152 TTC60 I O...
Page 181: ...2 153 2 TTC36X Pin arrangement...
Page 182: ...2 154 TTC36X lower part I O...
Page 209: ...2 181 19 2 5 LIST OF CONTROLLER INPUT MONITORING...
Page 210: ...2 182 19 2 6 LIST OF CONTROLLER ANALOG INPUT OUTPUT MONITORING...
Page 245: ...3 9 1 2 3 ANGLE METER 360 S200M3297000...
Page 274: ...3 38...
Page 293: ...4 19 8 SERVICE LOCATIONS...
Page 294: ...4 20...
Page 296: ...5 2 1 ELECTRICAL MOTOR UNIT ASSEMBLY Unit weight 180 kg...
Page 324: ...5 30...
Page 325: ...5 31 4 ELECTRICAL DIAGRAM S200M3122000 01...
Page 326: ...5 32 S200M3122000 02...
Page 336: ...6 8 1 3 2 INTERNAL STRUCTURE OF WINCH MOTOR...
Page 345: ...6 17 4 WORKING RADIUS LIFTING HEIGHT OF ONE FALL WINCH...
Page 348: ......